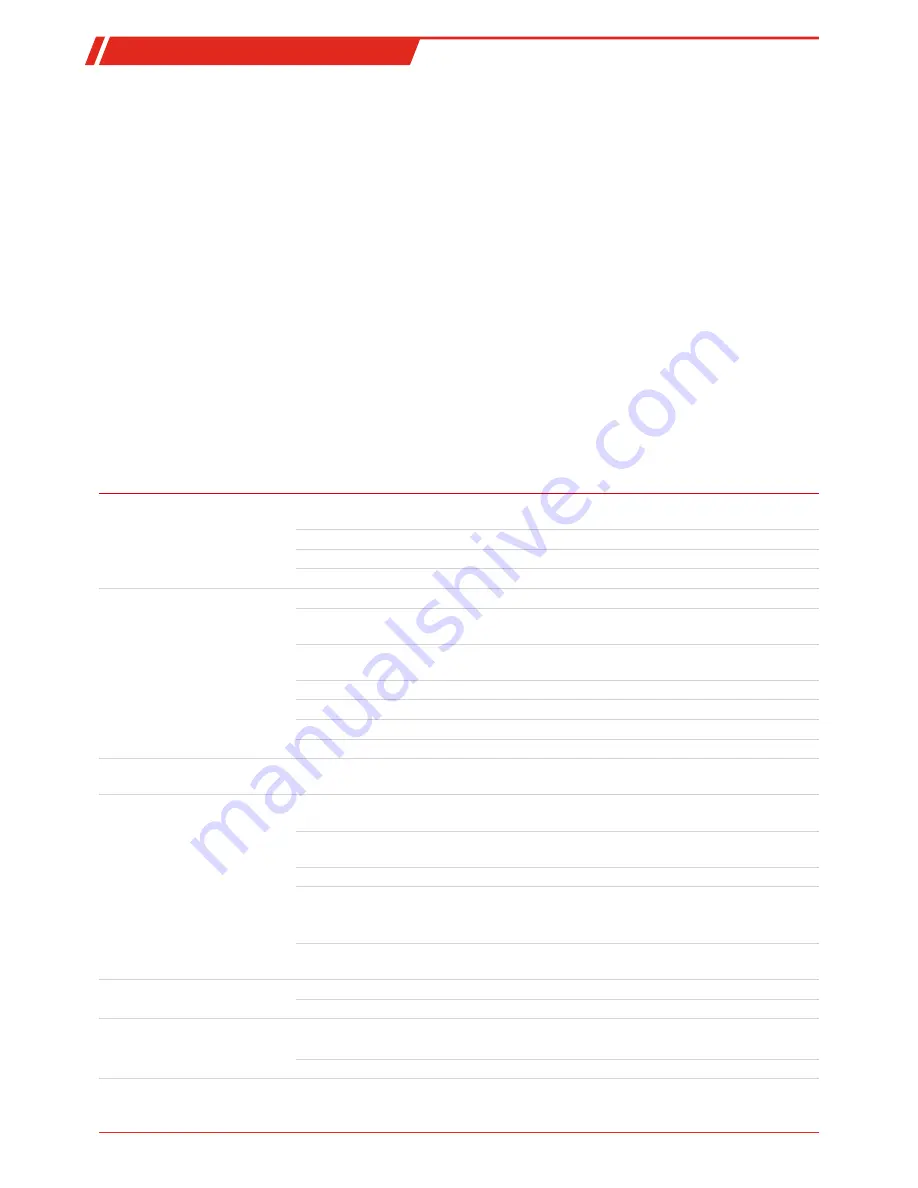
PCS.base
7 Service and repair
This chapter contains information on troubleshooting and correction should an error occur during operation.
Repairs to the unit must be performed by Bühler authorised personnel.
Please contact our Service Department with any questions:
Tel.: +49-(0)2102-498955
or your agent
If the equipment is not functioning properly after correcting any malfunctions and switching on the power, it must be inspected
by the manufacturer. Please send the equipment inside suitable packaging to:
Bühler Technologies GmbH
- Reparatur/Service -
Harkortstraße 29
40880 Ratingen
Germany
Please also attached the completed and signed RMA decontamination statement to the packaging. We will otherwise be unable
to process your repair order.
You will find the form in the appendix of these instructions, or simply request it by e-mail:
.
7.1 Troubleshooting
Problem / malfunction
Possible cause
Action
No LED lights up
– Mains voltage interrupted
– Connect to mains; check the plug is correctly
inserted
– Defective fuse
– Check fuse and replace if necessary
– Defective LED
– Send in cooler
– Internal error
– Send in cooler
Flashing red LED
(f = 1 Hz)
Excess / insufficient temperature
– Operating point not yet reached
– Wait (max. 15 min)
– Cooling output too long despite the
cooler running
– Be sure the vents are not covered (heat
buildup)
– Flow rate / dew point / gas temperature
too high
– Maintain limits / install pre-separator
– Installed fan stopped
– Check and replace if necessary
– Faulty control
– Send in cooler
– Short circuit
– Temperature sensor defective: Send in cooler
– Broken wire
– Temperature sensor defective: Send in cooler
Flashing red LED
(f = 5 Hz)
– Internal error
– Send in cooler
Steady red LED
Moisture in the sample gas
(If the moisture detector was
triggered, it must then be dried)
– Cooler overloaded, flow rate / dew
point / gas temperature too high
– Maintain limits / install pre-separator
– Cooling output too long despite the
cooler running
– Be sure not to cover the ventilation slots
(heat buildup); maintain limits
– Condensate trap full
– Empty condensate trap
– Water penetrating from water bag
– Observe delivery rate of peristaltic pumps
– Install condensate drain with downward
slope
– Cable break in the moisture detector
connection line
– Check connection line and plug-in connec-
tion
Condensate inside the gas output – Condensate trap full
– Empty condensate trap
– Cooler overload
– Maintain limits
Reduced gas flow rate
– Gas circuit clogged
– Uninstall and clean heat exchanger
– if necessary, replace filter element
– Condensate output iced over
– Send in cooler
Tab. 1:
Troubleshooting
12
Bühler Technologies GmbH
BE464003 ◦ 11/2017
Summary of Contents for CSPB1 series
Page 22: ......