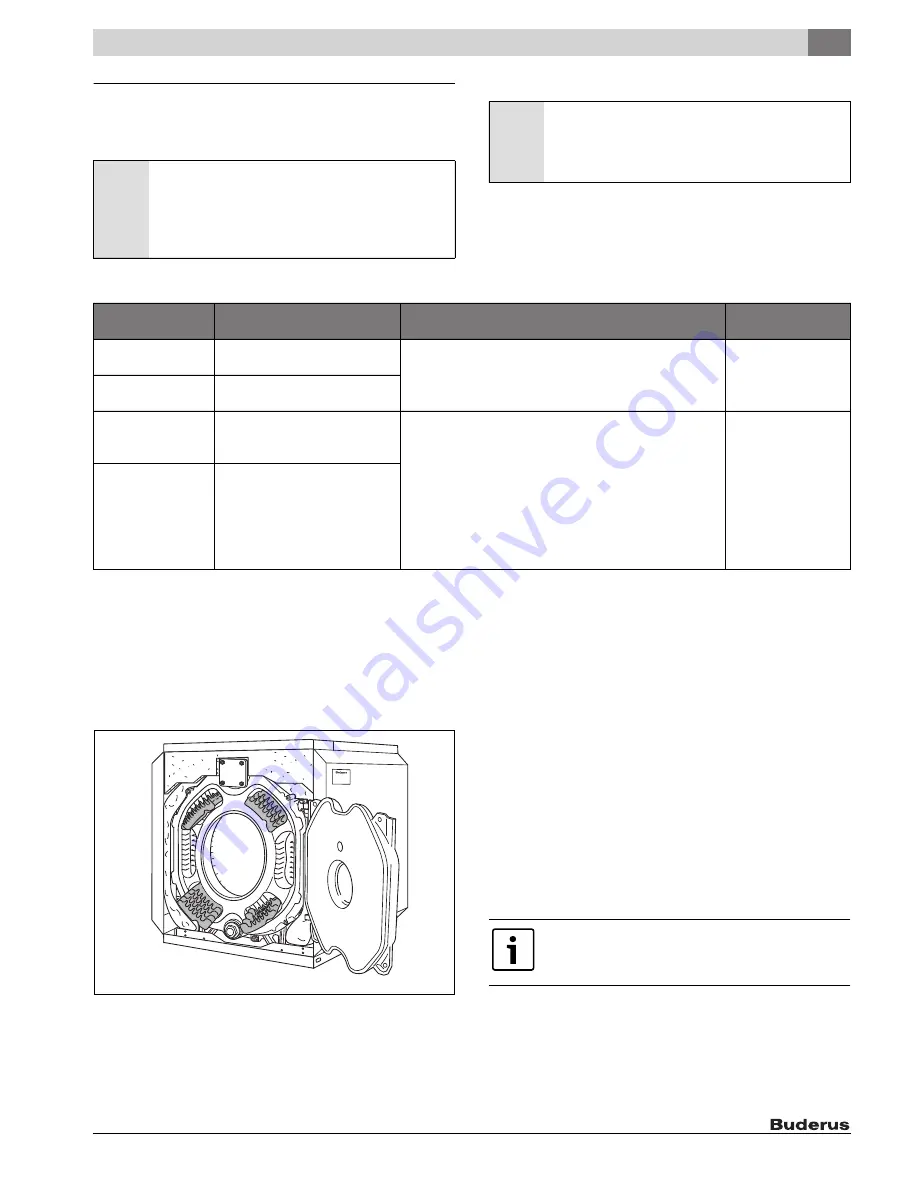
11
System start-up
Logano G315 – 6 720 817 939 (2017/02)
31
11
System start-up
You can connect various control panels to the Logano G315. The
commissioning process for the different types of controls is similar.
▶ Complete the commissioning log (
11.1
Filling the system
Refer to the table below for information about correct use and treatment
of the fill and make-up water.
The pH value of the boiler water increases after the heating system has
been filled. After 3 – 6 months (at the time of the first service), check
whether the pH value of the boiler water has stabilized.
11.2
Commissioning the system
Observe the following when commissioning:
▶ Purge your heating system via its radiators prior to commissioning.
▶ Check that the hot gas baffle plates are inserted correctly
(
Fig. 58 Check position of flue gas baffles
11.3
Start up the control panel
Please see the accompanying technical documentation for the 4000
series control panel you are using for information on how to start it up.
11.4
Initial burner start-up
▶ When commissioning the burner, follow the installation and
maintenance instructions enclosed with the burner.
▶ Fill out the commissioning log in the burner documentation.
If you notice when taking measurements for the commissioning log that
the flue gas temperature is too low for the vent pipe (risk of
condensation), you can raise the flue gas temperature
(
11.5
Raising flue gas temperature
With a new boiler, the flue gas temperature when the boiler temperature
is 176 °F (80 °C) will be around 320 – 356 °F (160 – 180 °C),
depending on the boiler rating.
In two-stage operation the temperature of the flue gas is lower.
You can increase the flue gas temperature further by removing individual
hot gas check plates and hot gas baffle plates or combinations of these.
▶ Take the boiler out of operation in accordance with the operating
instructions.
You can increase the temperature of the flue gas by carrying out the
following measures.
NOTICE:
The boiler can be damaged through heavy dust
deposits!
▶ Do not operate the boiler where heavy dust
contamination persists, e.g. through building work
inside the boiler room.
NOTICE:
Risk of system damage from temperature
stresses.
▶ During operation, only fill the heating system via the
fill valve on the system side.
Overall boiler output
MBH (kW)
Ca (HCO3)2 concentration /
grains per gallon
1)
ppm
Maximum fill and make-up water quantity
Vmax / ft3 ( m³)
Boiler water pH value
341 < Q
1,194
(100 < Q
350)
11.7 (
2.0)
V
max
= three times system volume
8.2–9.5
1,194 < Q
3412
(350 < Q
1000)
8.8 (
1.5)
341 < Q
1,194
(100 < Q
350)
> 11.7 (> 2.0)
8.2–9.5
1,194 < Q
3412
(350 < Q
1000)
> 8.8 (> 1.5)
Table 12 Requirements for fill, make-up and boiler water
1) 1 ft3 = 7.48 gal
V
max
0 0243
Q MBH
Ca HCO
3
2
gr
gal
-------
---------------------------------------------
V
max
0 0313
Q kW
Ca HCO
3
2
mol
m
3
----------
-----------------------------------------------
=
=
6 720 817 939-01.1T
You should only consider modifying the hot gas check
plates as a last resort as once you have reduced the size
of the hot gas check plates you cannot change this back.
Summary of Contents for Logano G315
Page 55: ...Appendix Logano G315 6 720 817 939 2017 02 55 ...
Page 56: ......