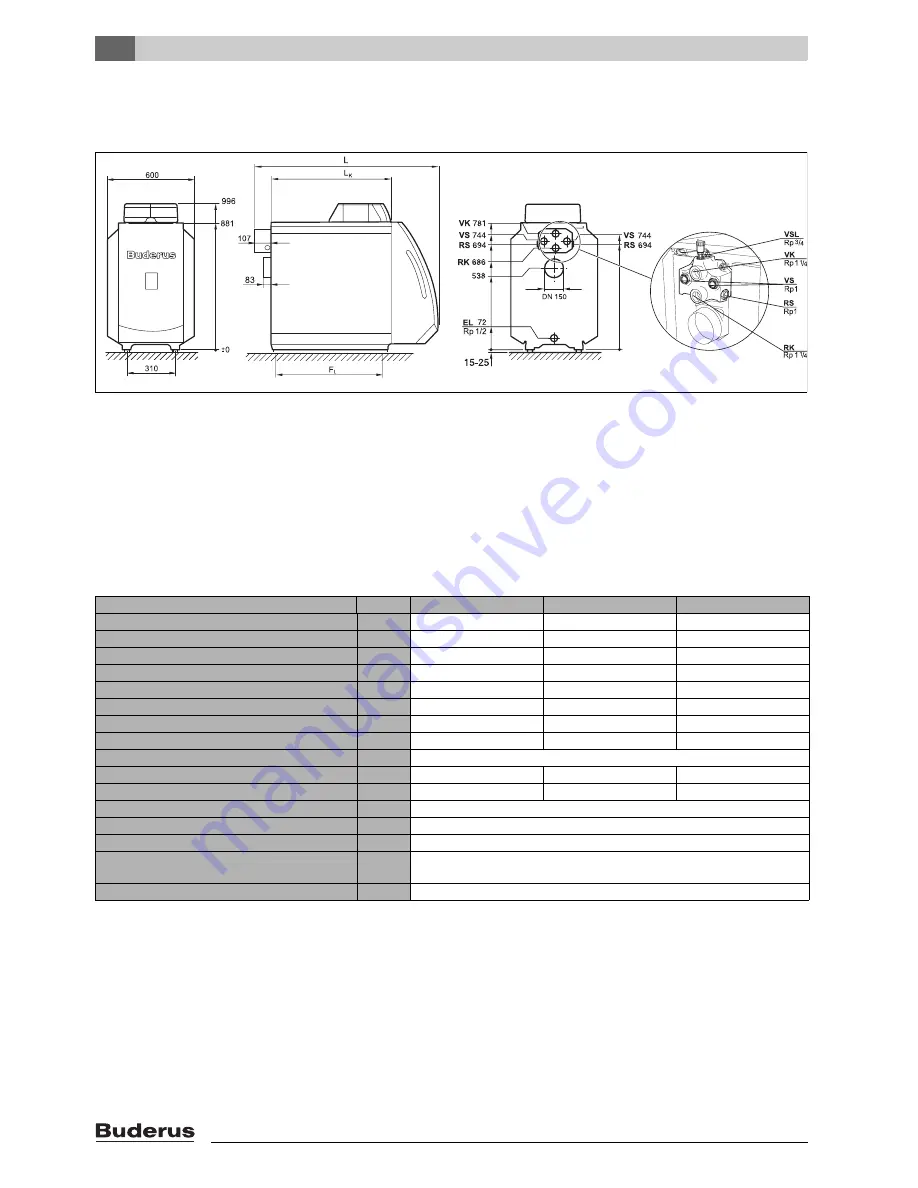
2
Product details
Logano G225/Logano plus GB225 - We reserve the right to make any changes due to technical modifications.
10
2.10
Dimensions and specifications
2.10.1 Logano G225 BE dimensions
Fig. 2
Connections and dimensions (sizes in mm)
Connections (for sizes see tables below):
VK
= Boiler flow
RK
= Boiler return
EL
= Boiler drain (connection for drain tap)
VS
= DHW cylinder flow
RS
= DHW cylinder return
VSL = Pressure relief flow pipe (connection for automatic air
vent valve provided by installer)
Connections and sizes:
6 720 615 876-02.1RS
Boiler size
45
55
68
Oil burner
Type
BE2.3-45
BE2.3-55
BE2.3-68
Boiler sections
Number
4
5
6
Rated output
KW
45
55
68
1)
1) 65 kW (for Spain)
Combustion output
KW
48.1
59.0
73.0
2)
2) 69.8 kW (for Spain)
Boiler water content
l
Approx. 61
Approx. 73
Approx. 85
Gas content
l
68.8
85.1
101.4
Flue gas temperature
3)
3) Flue gas temperature to EN 303.
°C
165
180
180
Flue gas mass flow rate
kg/s
0.0197
0.0242
0.0299
4)
4) 0.0287 kg/s (for Spain)
CO
2
content, oil
%
13.5
Available draught
Pa
50
50
30
Flue gas back pressure
mbar
0.35
0.20
0.35
Permissible flow temperature
5)
5)Safety limit (high limit safety cut-out, STB)
Maximum possible flow temperature = Safety limit (STB) - 10 K
Example: Safety limit (STB) = 100 °C, maximum possible flow temperature = 100 - 10 = 90 °C
The safety limit must meet the national regulations of the country concerned.
°C
100
Permissible operating pressure
bar
4
Maximum time constant of temperature control
s
≤
1
Maximum time constant of temperature
monitor and high limit safety cut-out (STB)
s
≤
1.2
Power supply rating
230 VAC, 50 Hz, 10 A IP 40
Tab. 3
Specifications