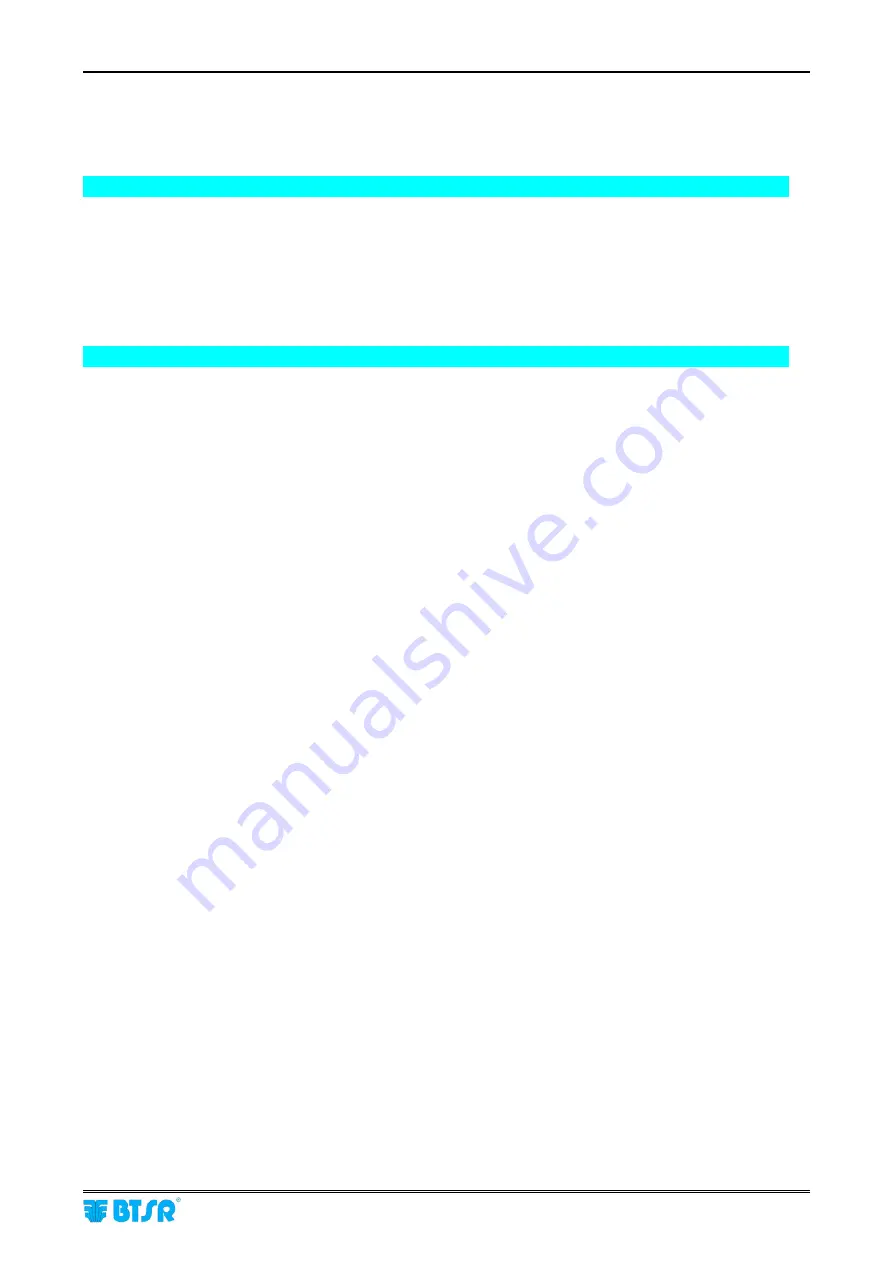
Table of Contents
SMART MATRIX MTC
- iii -
Table of Contents
1 – Connections and Electrical Interface
PC
↔
SMART MATRIX
↔
SM-DIN Connection....................................................................................... 1-1
SMART MATRIX
↔
SM-DIN
↔
IS3W/MTC Connection .......................................................................... 1-2
SM-DIN
↔
Machine Interface ................................................................................................................... 1-3
Interfaccia Sensori ..................................................................................................................................... 1-4
SMART MATRIX
↔
SM-DIN/PC Interface................................................................................................ 1-5
SMART MATRIX MTC Generic Application Diagram................................................................................ 1-6
2 – Operating instruction
SMART MATRIX MTC Operation.............................................................................................................. 2-1
Navigation throughout the Display Windows............................................................................................. 2-2
1 – Navigation inside the Selected Window (STD).................................................................................... 2-3
2 – Windows Swap .................................................................................................................................... 2-4
3 – Entering Alphanumeric Values ............................................................................................................ 2-5
4 – Parameters Saving .............................................................................................................................. 2-5
Immediate Function Activation through the SMART MATRIX Buttons ..................................................... 2-6
Interpretation of Operating Screens .......................................................................................................... 2-7
SMART MATRIX MTC Menu Structure ..................................................................................................... 2-8
Sensor Configuration and Numbering ....................................................................................................... 2-9
DACS devices Configuration and Numbering (
option
) ........................................................................... 2-12
Smart Matrix Code.................................................................................................................................. 2-13
Input/Output Configuration on SM-DIN/Smart Matrix ............................................................................. 2-14
Speed Setting (option)............................................................................................................................. 2-16
Keycode Setting....................................................................................................................................... 2-17
Communication Test................................................................................................................................ 2-19
Sensor Test ............................................................................................................................................. 2-20
DAC devices test (option)........................................................................................................................ 2-21
Sensor Firmware Upgrade ...................................................................................................................... 2-22
DAC Firmware Upgrade (option) ............................................................................................................. 2-23
SM-DIN/MTC Board Firmware Upgrade.................................................................................................. 2-24
Information reading from SM-DIN/MTC Boards ...................................................................................... 2-25
Information reading from DAC devices.................................................................................................... 2-26
MATRIX LCD Adjustment........................................................................................................................ 2-27
Information about SMART MATRIX MTC................................................................................................ 2-28
Style Programming (IS3W)...................................................................................................................... 2-29
Style Loading ........................................................................................................................................... 2-35
Position setting ........................................................................................................................................ 2-37
Speed Programming (option) .................................................................................................................. 2-39
Speed Loading (option) ........................................................................................................................... 2-42
Graphic display ........................................................................................................................................ 2-44
Efficiency Data......................................................................................................................................... 2-46
Alarm Counter Display (IS3W) ................................................................................................................ 2-48
SMART MATRIX Error Messages ........................................................................................................... 2-50
Errors shown on Display of SM-DIN Boards ........................................................................................... 2-52
Summary of Contents for SMART MATRIX MTC
Page 1: ...SMART MATRIX MTC Operating Manual ENGLISH Rev 1 0 September 2010 ...
Page 3: ...Introduction i ...
Page 4: ......
Page 9: ...Connections and Electrical Interface 1 ...
Page 10: ......
Page 17: ...Operating Instructions 2 ...
Page 18: ......
Page 71: ...System Information 3 ...
Page 72: ......