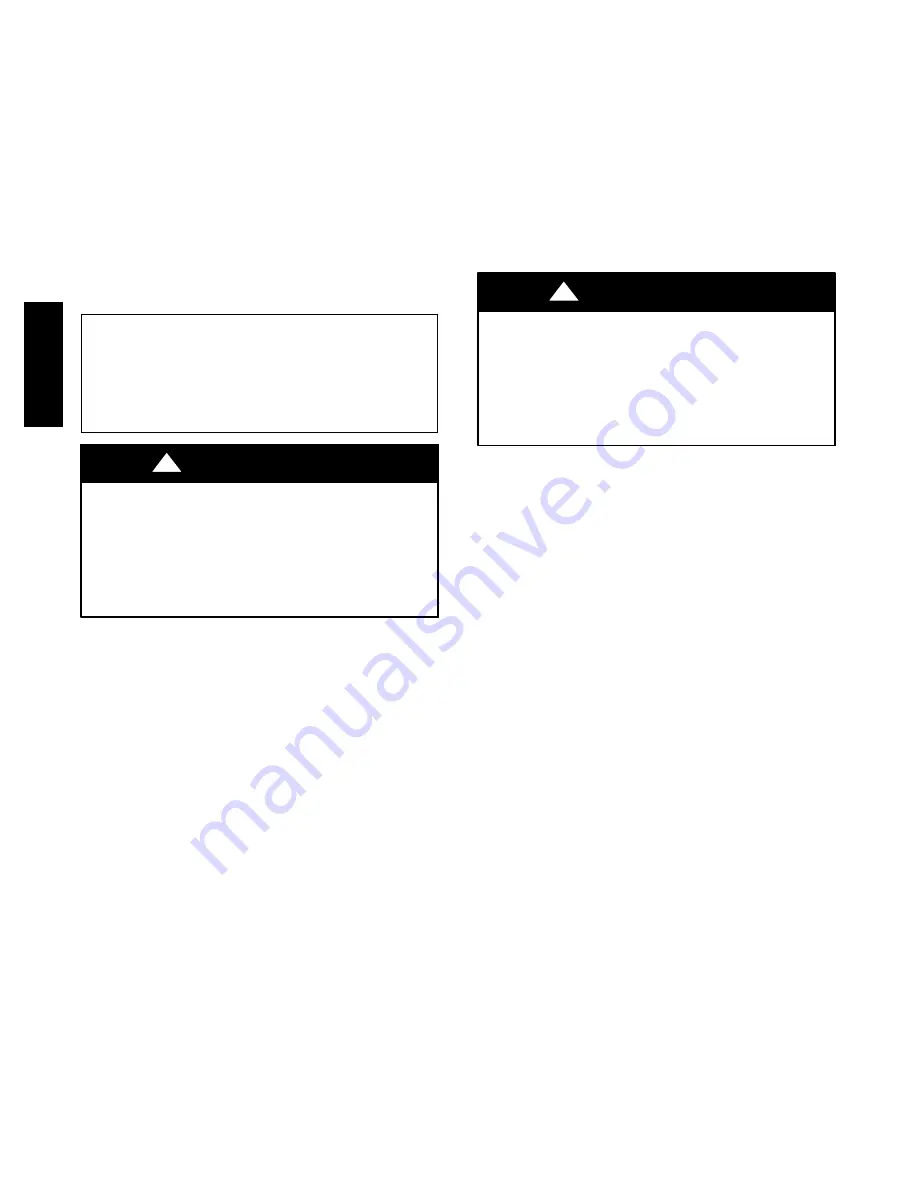
26
Step 9 — Wind Baffles for Low Ambient Control
Models 569J***B and 569J***E include the factory
installed 32LT Motormaster Low Ambient Control. Model
569J*12F (with hot gas bypass option) also includes the
32LT Motormaster Low Ambient Control as a standard
feature.
Units with 32LT Motormaster control require the addition
of wind baffles to ensure full range low ambient
operation. Material data and dimensions for wind baffles
are included in the Appendix C section, Low Ambient
Control, starting on page 50. Fabricate the wind baffles
and mount per instructions.
PRE-START-UP
IMPORTANT
: Before beginning Pre-Start-Up or
Start-Up, review Start-Up Checklist at the back of this
book. The Checklist assures proper start-up of a unit
and provides a record of unit condition, application
requirements, system information, and operation at
initial start-up.
UNIT DAMAGE HAZARD
Failure to follow this caution may result in equipment
damage.
Do not attempt to start the condensing unit, even
momentarily, until the following steps have been
completed. Compressor damage may result.
CAUTION
!
System Check
1. The electrical power source must agree with the unit’s
nameplate rating.
2. Check all air handler(s) and other equipment auxiliary
components. Consult the manufacturer’s instructions re-
garding any other equipment connected to the condens-
ing unit. If the unit has field-installed accessories, be
sure all are properly installed and correctly wired. If
used, the airflow switch must be properly installed.
3. Check tightness of all electrical connections.
4. Be sure liquid line and low side of the system are
properly leak checked and dehydrated.
5. Be sure the unit is properly charged. See “Preliminary
Charge”, below.
6. Open the liquid line and suction line service valves.
7. The crankcase heater must be firmly attached to the
compressor crankcase. Be sure the crankcase is warm
(heater must be on for 24 hours before starting
compressor).
Turn On Crankcase Heater —
Turn on the crankcase heater for 24 hours before starting
the unit to be sure all the refrigerant is out of the oil
. To
energize the crankcase heater, proceed as follows:
1. Set the space thermostat set point above the space
temperature so there is no demand for cooling.
2. Close the field disconnect.
Preliminary Charge —
Before starting the unit, charge liquid refrigerant into the
high side of the system through the liquid service valve. The
amount of refrigerant added must be at least 80% of the
operating charge listed in the Physical Data table (Tables 1A
through 2B, pages 6 through 9). Allow high and low side
pressures to equalize before starting compressor. If pressures
do not equalize readily, charge vapor on low side of system
to assure charge in the evaporator. Refer to GTAC II,
Module 5, Charging, Recover, Recycling, and Reclamation
for liquid charging procedures.
UNIT DAMAGE HAZARD
Failure to follow this caution may result in equipment
damage.
Prior to starting compressor, a preliminary charge of
refrigerant must be added to avoid possible
compressor damage.
CAUTION
!
START-UP
569J Units:
The compressor crankcase heater must be on
for 24 hours before start-up. After the heater has been on
for 24 hours, the unit can be started. If no time elapsed
since the preliminary charge step was completed, it is
unnecessary to wait the 24-hour period.
Preliminary Checks
1. Check that electric power supply agrees with unit
nameplate data.
2. Verify that the compressor crankcase heater is
securely in place.
3. Check that the compressor crankcase heater has been
on at least 24 hours.
4. Recheck for leaks using the procedure outlined in the
Pre-Start-Up section, Leak Test and Dehydration. If
any leaks are detected, repair as required. Evacuate
and dehydrate as described in the Leak Test and De-
hydration section.
5. Ensure that the preliminary charge has been added as
described in the Pre-Start-Up section, Preliminary
Charge.
6. All internal wiring connections must be tight, and all
barriers and covers must be in place.
NOTE
: The 569J units are factory charged with the
required amount of oil. If recharging is required, use
Emkarate RL 32-3MAF for the 569J units.
Compressor Rotation —
On 3--phase units with scroll compressors, it is important to
be certain that the compressor is rotating in the proper
direction. 569J units are equipped with a Comfort Alert
Diagnostic Module (CADM). Alert Code 7 indicates reverse
power phasing.
569J
Summary of Contents for 569J Series
Page 34: ...34 C10925 Fig 29 Typical Single Circuit Single Stage 569J A B Wiring Diagram 569J ...
Page 35: ...35 C150339 Fig 30 Typical Single Circuit Two Stage 569J 07G H Wiring Diagram 569J ...
Page 36: ...36 C12547 Fig 31 Typical Dual Circuit Two Stage 569J D E F Wiring Diagram 569J ...
Page 53: ...53 D K J H G F E C B A C10800 Fig 44 Wind Baffles 569J ...