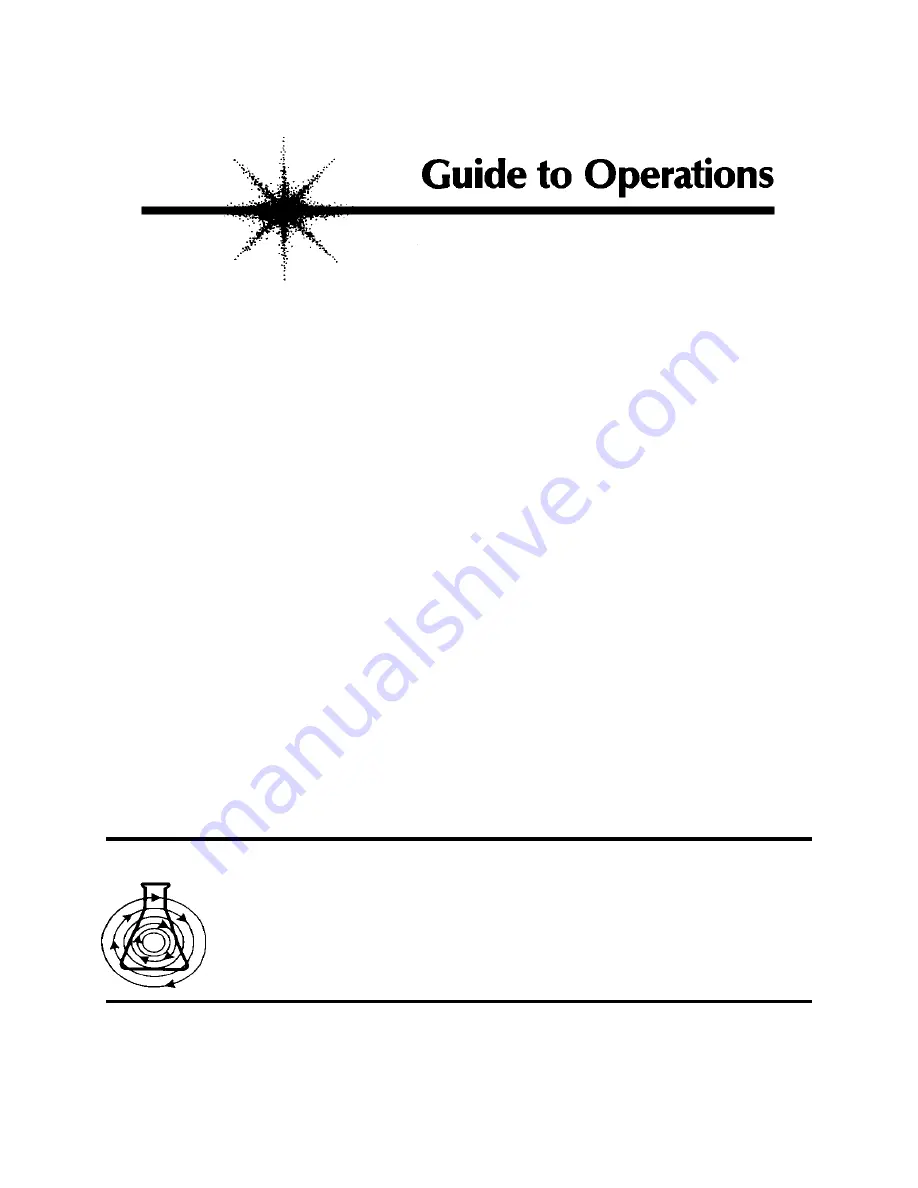
I-26/26R
Large Stackable
Incubator Shakers
MANUAL NO: M1324-0050
Revision B
March 15, 2006
NEW BRUNSWICK SCIENTIFIC CO., INC.
BOX 4005
•
44 TALMADGE ROAD
•
EDISON, NJ 08818-4005
Telephone: 1-732-287-1200
•
1-800-631-5417
Fax: 732-287-4222
•
Telex: 4753012 NBSCO
Internet: http://www.nbsc.com
•
E-mail: [email protected]