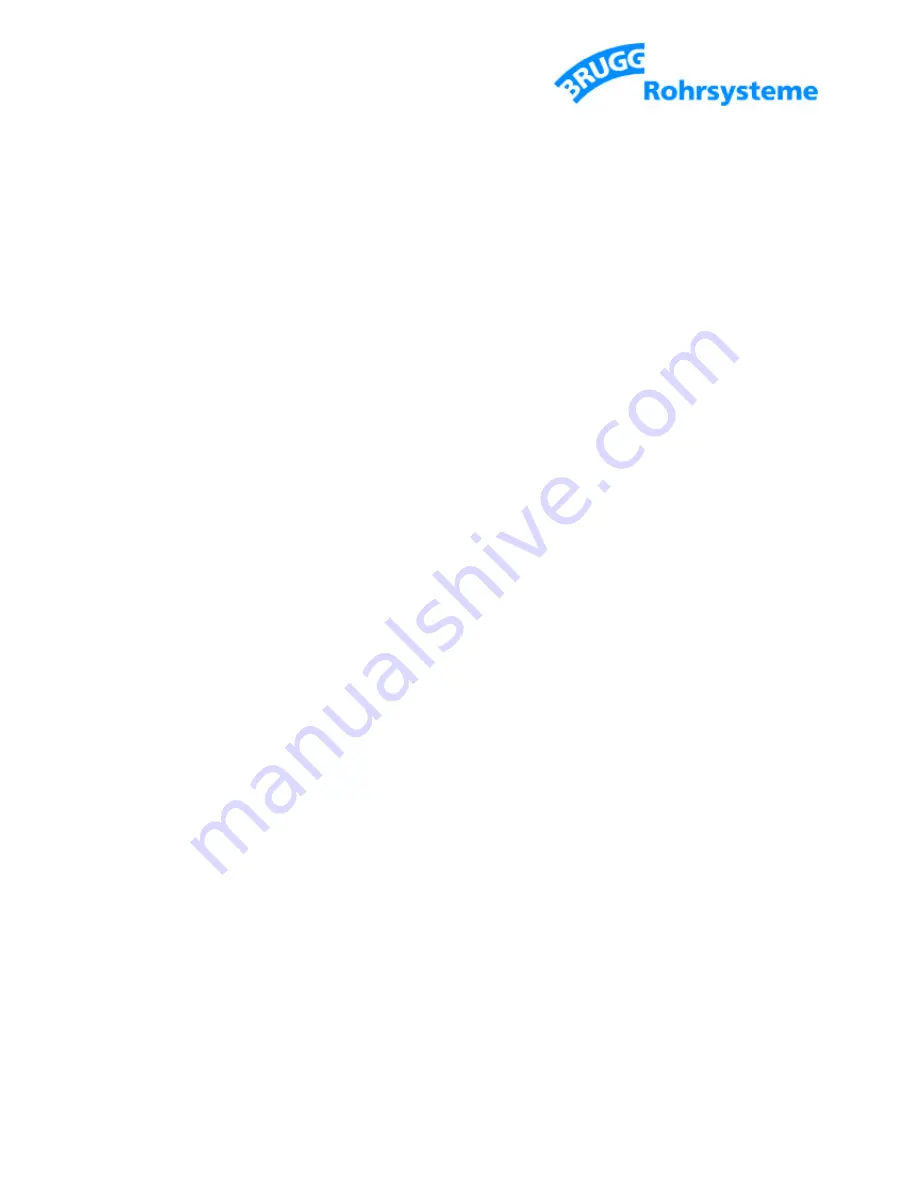
BRUGG Rohrsysteme GmbH ·- Adolf-Oesterheld-Str. 31 - D-31515 Wunstorf
Tel.: +49 (0) 5031 170-0 Fax: +49 (0) 5031 170-170 e-mail: [email protected]
page 3 of 11
1
Technical data
Power supply:
230V 50Hz max. 3kVA
Initial fuse
16A
Equipment grounding conductor must be connected properly!
Clear sinusoidal voltage is essential whenever the welding machine is
powered by a generator!
General specifications:
weight: approximately 16 kg:
dimensions: 350 x 250 x 250 mm (H x W x L)
Initial value:
max. 52V 50Hz 50A
2
Important safety information
Only use manufacturer-approved joints when operating this equipment. Operators
must observe equipment technical data and this operating manual as well as use
genuine spare-parts and accessories. Do not use this equipment for purposes not
designated in this instruction manual. Improper use or handling releases the
manufacturer of any and all liability.
To ensure that the internal safety features are fully enabled, ensure that the
equipment is adequately grounded. The operator is responsible for ensuring that the
joint connections do not fall off. Contact with the output terminal during welding
procedures can lead to serious injury.
Any form of manipulation or removal of protective features is prohibited.
In addition to the operating and safety rules in this manual, the operator must
observe all statutory and otherwise binding safety and environmental regulations.
These regulations can, for example, pertain to the handling of hazardous substances
or the availability of/the wearing of protective gear.
Always check the operative features of all safety fixtures after servicing or
maintenance.
The operator must ensure that mains supply is conform with the specifications listed
under chapter 1. All supply lines must match outlet terminal.
Only use the genuine spare parts listed in this manual.