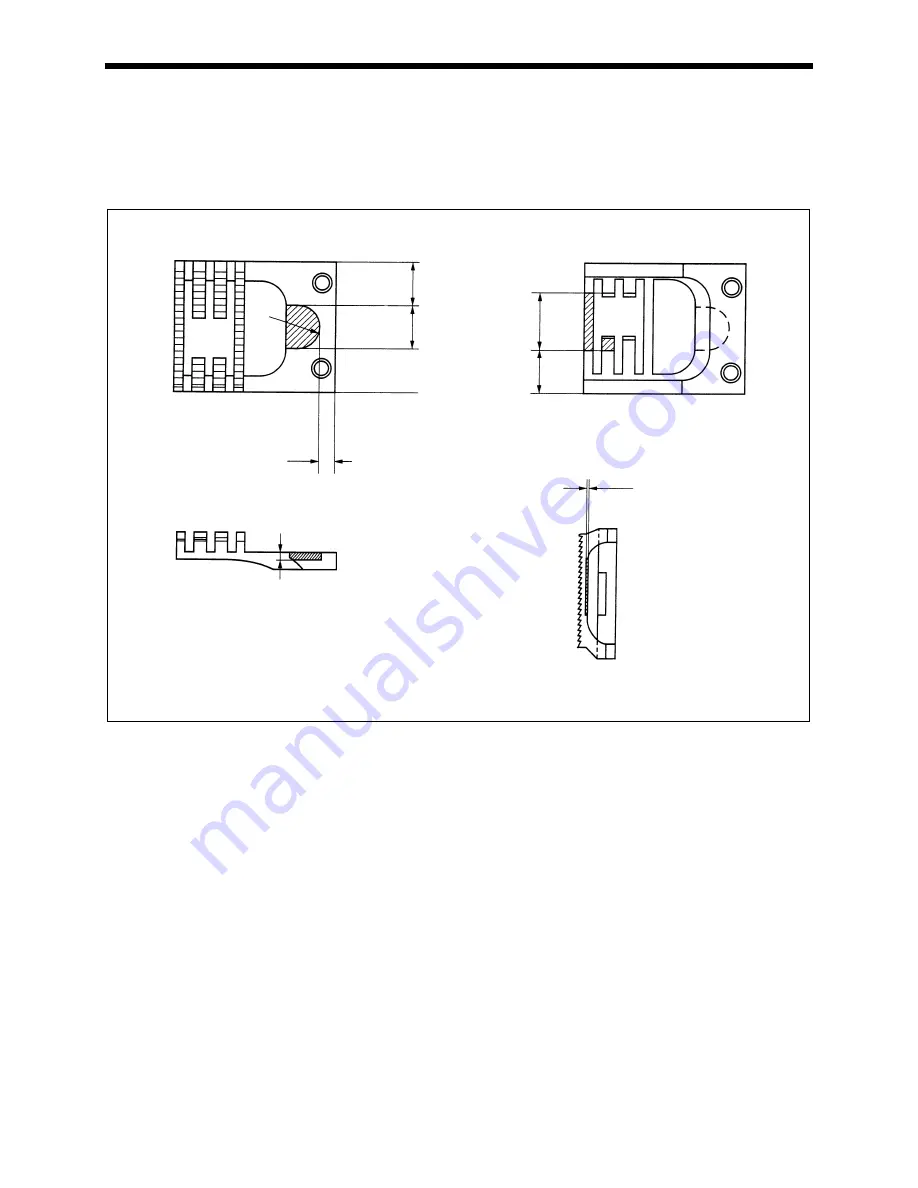
Z-8550A, 8560A
14. WHEN USING A NON-STANDARD FEED DOG (8560A only)
73
14. WHEN USING A NON-STANDARD FEED DOG
(8560A only)
When using a non-standard feed dog, modify it as shown below.
* Using a non-standard feed dog without modifying it will break the movable and fixed knives.
1405M
0.5
15
R5.5
11
11
11
4
2