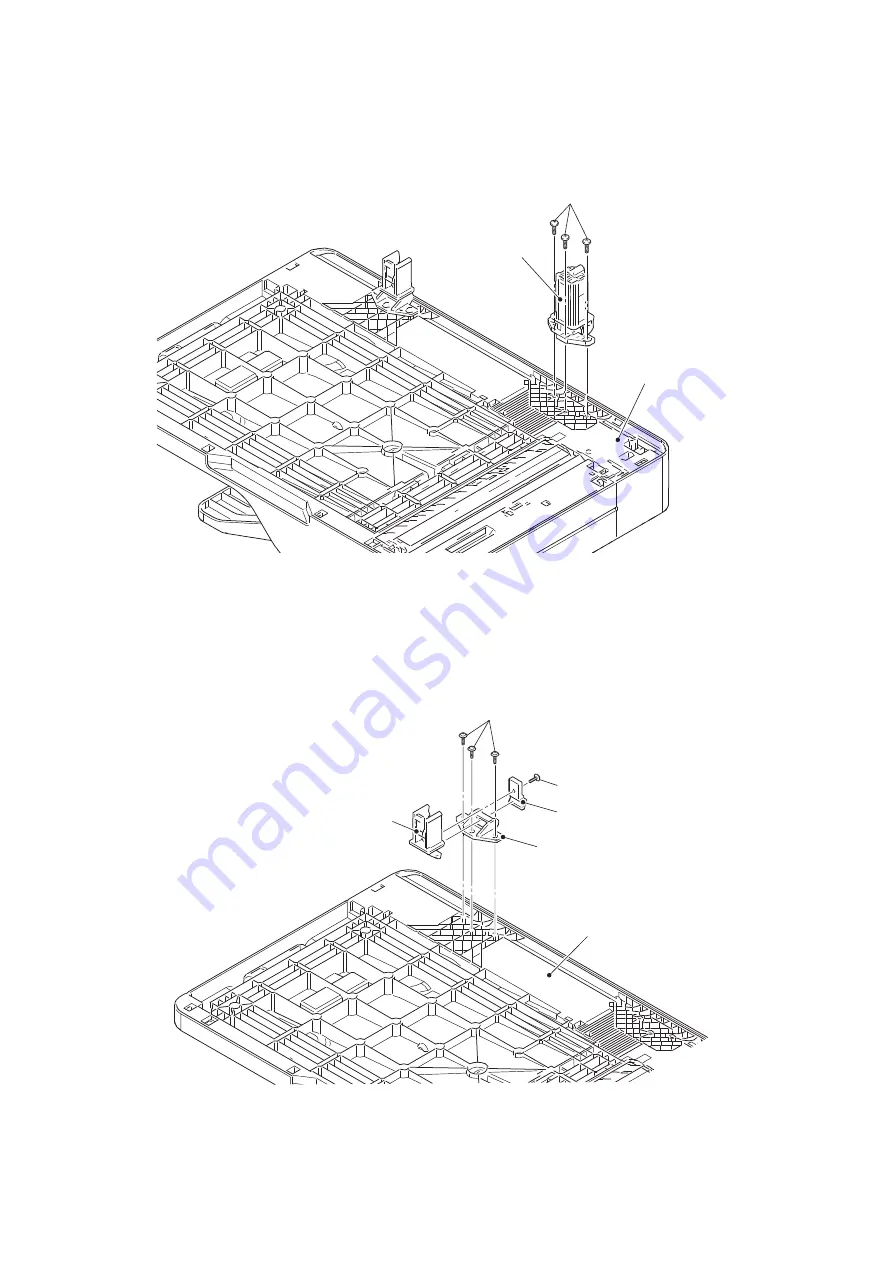
3-45
Confidential
9.11.2 Hinge L ASSY, Hinge R, Hinge R support, Hinge arm R
(1) Remove the three taptite bind B M4x12 screws to remove the hinge L ASSY from the
ADF unit.
Fig. 3-35
(2) Remove the taptite cup B M3x10 screw to remove the hinge R support and hinge R from
the hinge arm R.
(3) Remove the three taptite cup B M3x10 screws to remove the hinge arm R from the ADF
unit.
Fig. 3-36
Taptite bind B M4x12
Hinge L ASSY
ADF unit
Taptite cup B M3x10
Taptite cup B M3x10
Hinge R support
Hinge R
Hinge arm R
ADF unit