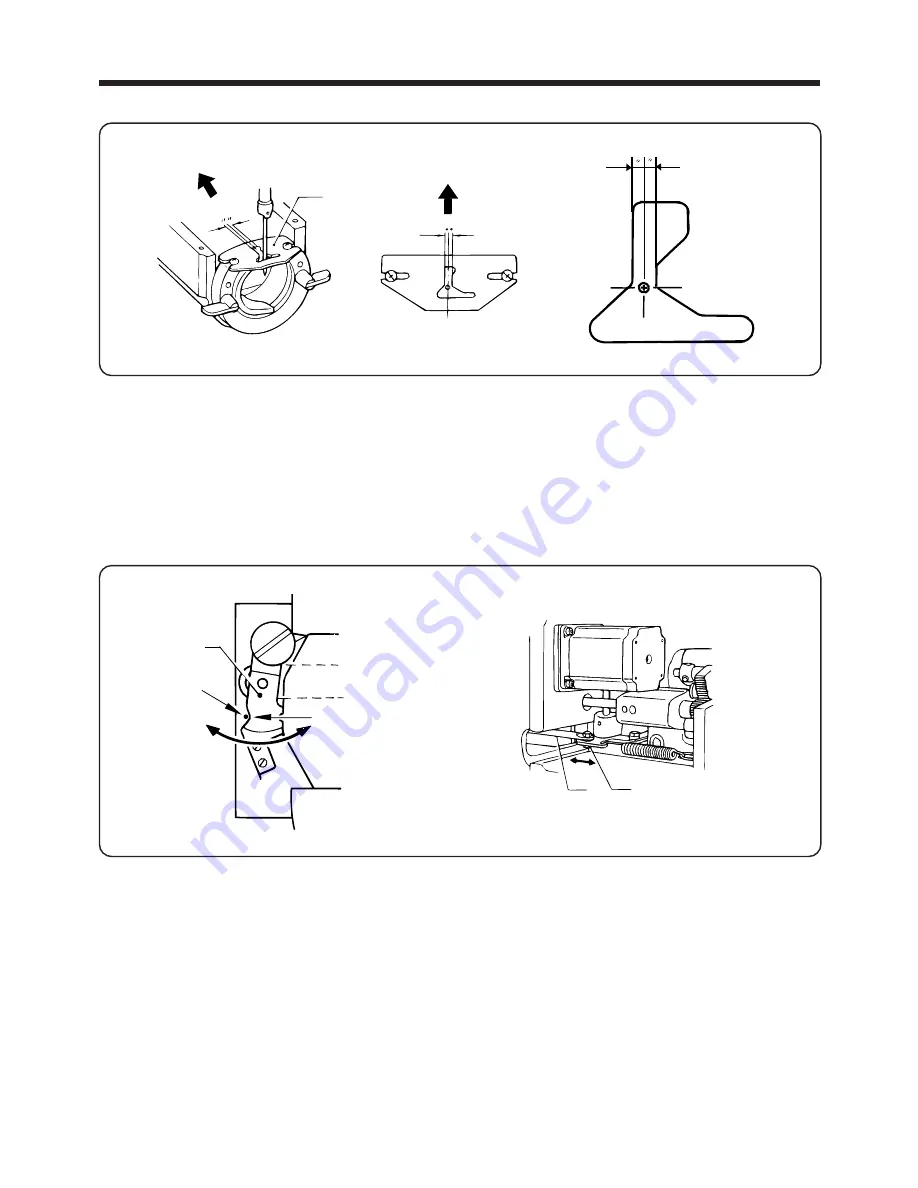
5. STANDARD ADJUSTMENT (MACHINE HEAD)
5-6. Adjusting the shuttle hook thread guide
Install the shuttle race thread guide
q
by pushing it in the direction of the arrow so that the needle groove is
aligned with the center of the needle plate hole.
NOTE: If the shuttle race thread guide is in the wrong position, thread breakages, soiled thread or catching of
the thread may occur.
5-7. Adjusting the movable knife
5-7-1. First bar tacking
1. Tilt back the machine head. (Refer to "5-1. Tilting back the machine head.")
2. Loosen the nut
w
and move thread trimmer rod L
e
to the left or right to adjust so that the V section
A
of the
movable knife
q
is aligned with the index mark
B
on the needle plate when the machine is at the stop
position.
―
40
―
BAS-705
w
e
q
B
q
A