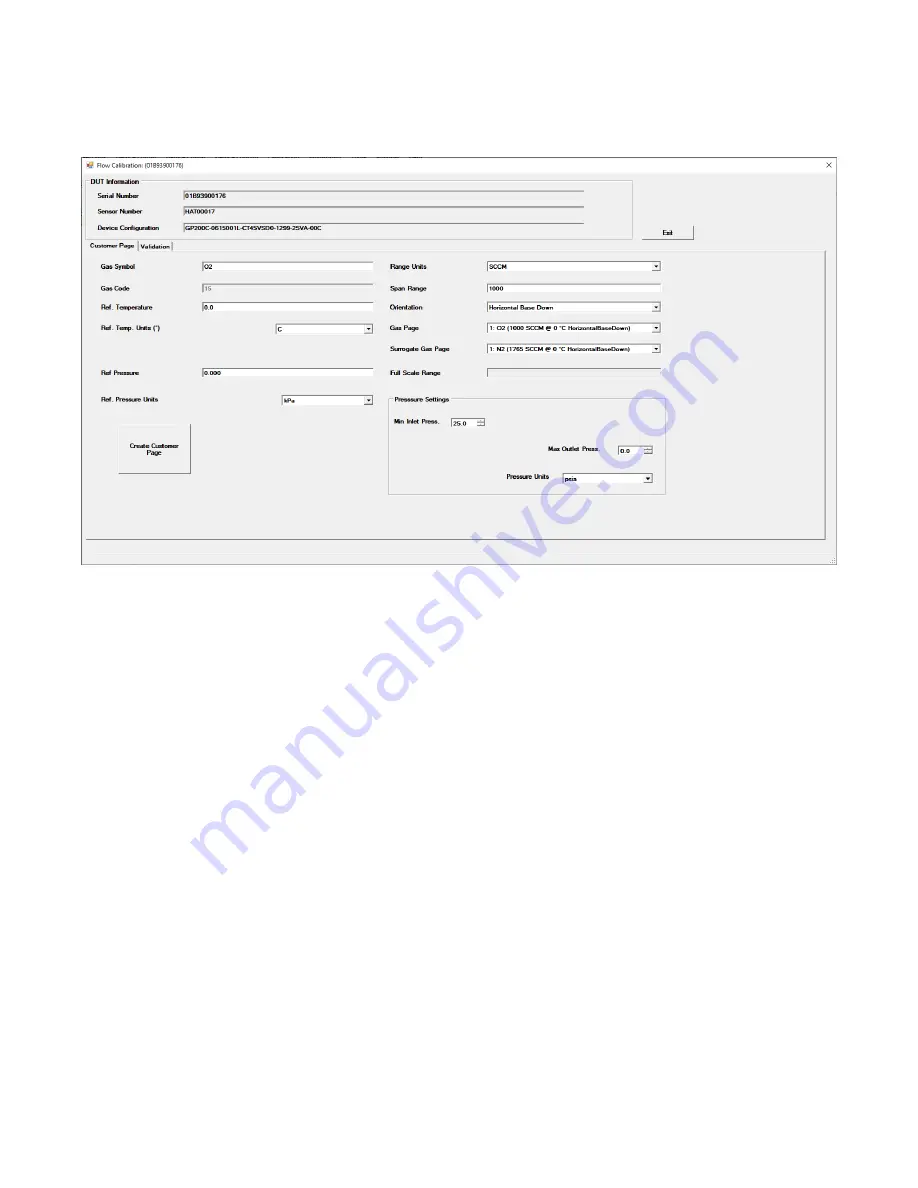
Figure 2-11 Changing Gas Pages using BEST
GP200 Warping in the Brooks Expert Support Tool
For GP200 devices, an adjustment called “Warping” allows a
user to adjust the device’s response to match their standard,
such as within a certain environment. The user enters
performance data of their device as measured in their
environment, then the software uses a curve fit to adjust the
device’s response accordingly. Warping requires a Brooks
Expert Support Tool license. For GP200 devices, a warp
adjustment is added to the device’s factory calibration and
can be cleared from a flow page without affecting the factory
calibration. The same flow page may then be used again
without the warp adjustment.
24
Summary of Contents for GP200 Series
Page 1: ...Installation Operation Manual GP200 Series Metal Sealed Pressure Based Mass Flow Controllers ...
Page 10: ...Table 1 3 Specifications for GP200 Series Section 1 Introduction 6 ...
Page 11: ...Section 1 Introduction 7 ...
Page 12: ...Figure 1 1 Dimensions of GP200 Series Downport Configurations Section 1 Introduction 8 ...
Page 13: ...Figure 1 2 Dimensions of GP200 Series VCR Configurations Section 1 Introduction 9 ...