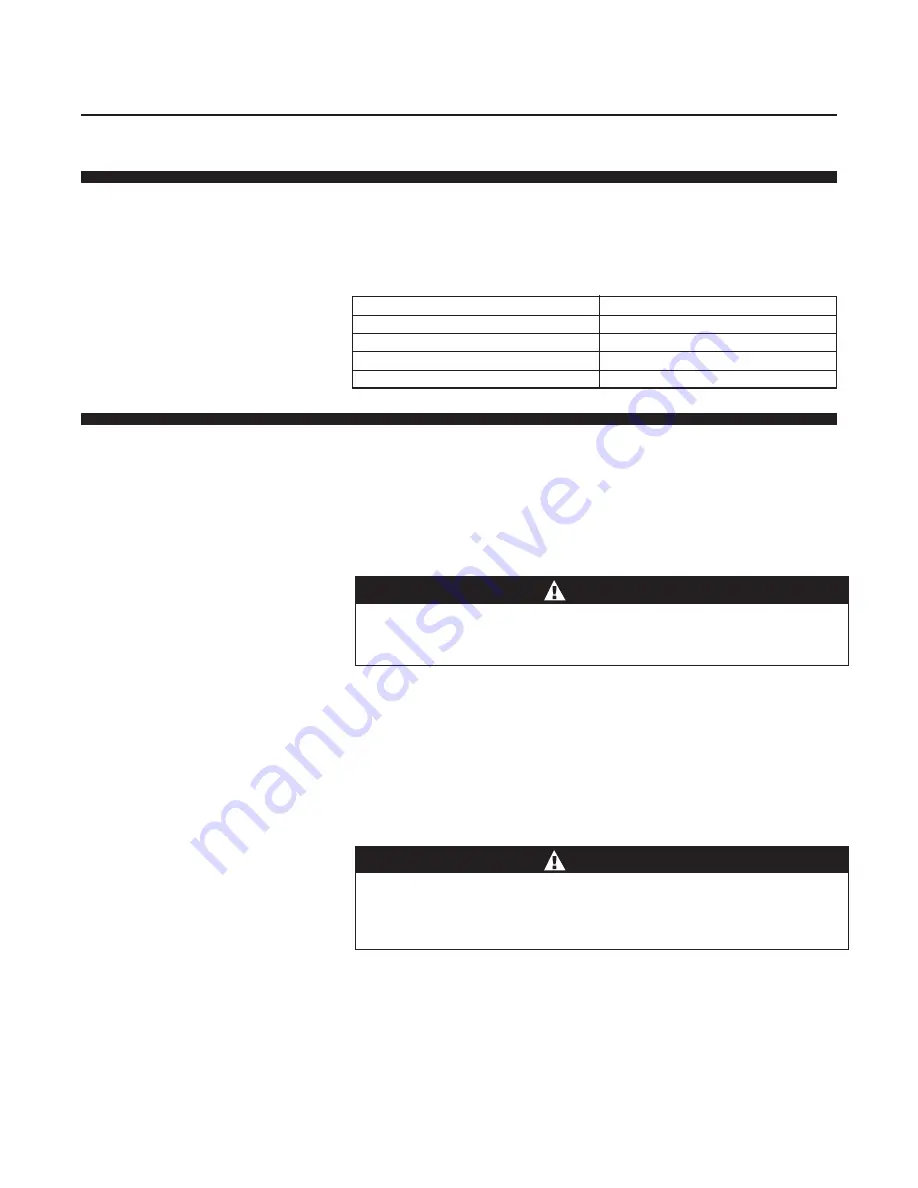
2-3
Brooks
®
Models 5964, 5850EM
Section 2 Installation
Installation and Operation Manual
X-TMF-5964-5850EM-MFC-eng
Part Number: 541B121AHG
November, 2008
2-7 In-Line Filter
It is recommended that an in-line filter be installed upstream from the
controller to prevent the possibility of any foreign material entering the
flow sensor or control valve. The filtering element should be replaced
periodically or ultrasonically cleaned.
Maximum Flow Rate
Recommended Filter
100 sccm
1 micron
500 sccm
2 micron
1 to 5 slpm
7 micron
10 to 30 slpm
15 micron
2-8 Installation
Prior to installation, make certain all piping is clean and free of
obstructions, for tubing installations. Install the piping in such a manner
that permits easy access to the instrument if it needs to be removed for
cleaning or test bench troubleshooting. For surface mount (downported)
devices verify that the seal cavities are clean and free of lateral
scratches.
When installing the controller, care should be taken that no
foreign materials enter the inlet or outlet of the instrument. Do not
remove the protective end caps until time of installation.
CAUTION
Recommended installation procedures:
a. The Model 5964/5850EM should be located in a clean, dry atmo-
sphere relatively free from shock and vibration.
b. Leave sufficient room for access to the electrical components, span
and zero potentiometers.
c. Install in such a manner that permits easy removal if the instrument
requires servicing.
When used with a reactive (sometimes toxic gas) contamination
or corrosion may occur as a result of plumbing leaks or improper
purging. Plumbing should be checked carefully for leaks and the
instrument purged with clean, dry N
2
before use.
CAUTION
d. The Model 5964/5850EM Mass Flow Controller can be installed in
any position. However, mounting in orientations other than the
original factory calibration (see calibration data sheet) can result in a
0.5% maximum full scale shift after re-zeroing.
Table 2-1 Recommended Filter Size