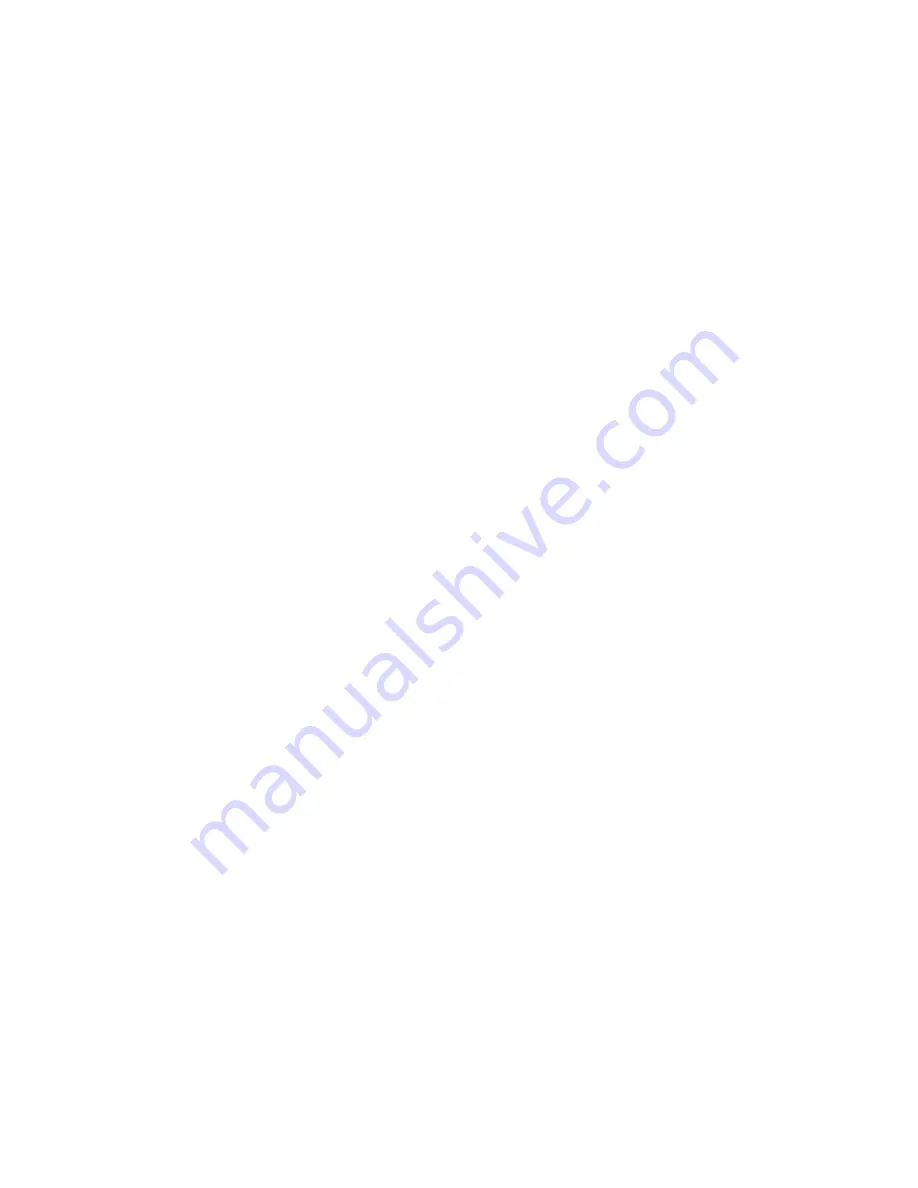
3-32
ROTATION GEARBOX INSTALLATION
AT TIME OF ROTATION BEARING INSTALLATION
The spacing between the rotation bearing and rotation gearbox is preset and non
adjustable. However, a set procedure is necessary at the time of assembly. The following
sequence should be followed when replacing the rotation bearing:
1.
Set the turntable upside down on the floor and loosely mount the rotation bearing and
gearbox on the turntable with the "high point" of the bearing against the pinion. This
is the painted tooth on the bearing. (The outer race bolts should be inserted in their
holes in the bearing before mounting the bearing.)
2.
Release the gearbox brake with a portable hand pump (300 psi (20.7 bar) minimum).
This will let the pinion teeth center between the "high point" teeth on the bull gear.
With the brake released the pinion will move. Use a pry bar to rotate the pinion teeth
until contact is made. This will leave some clearance on the other side of the tooth
for inserting a feeler gauge.
3.
While the bearing inner race bolts (turntable bolts), and gearbox bolts are installed,
but loose, use a large "C" clamp to snug the pinion and rotation gear teeth together.
With the bearing teeth and pinion teeth still clamped, tighten the turntable rotation
bearing bolts and gearbox bolts.
4.
Check the tooth parallel contact by sliding a 0.002" (0.05 mm) feeler gauge between
the bearing and pinion teeth. If the 0.002 (0.05 mm) gauge slides completely down
the full length of the tooth, try a 0.003 (0.07 mm) gauge. If the 0.003 (0.07 mm)
gauge will go completely down the length of the tooth, try a 0.004 (0.1 mm) gauge
(maximum acceptable). The 0.004 (0.1 mm) gauge may start but should not slide
completely to the other end of the tooth face. If the gauge will start but stops partly
down the face of the tooth, the rotation gearbox must be shimmed. A gauge larger
than 0.004 (0.1 mm) should not be able to slide completely down the tooth face. If
the clearance is great enough to allow this to happen, consult factory before
proceeding.
5.
0.005" (0.13 mm) shims (P/N 209-00302) are provided to go under the gearbox
mounting flange to set tooth parallelism. These must be used in equal numbers
under two adjacent gearbox bolts. The shims will tilt the pinion shaft about 25%.
(Example: 0.020 (0.5 mm) shims under the gearbox mounting flange will tilt the
bottom of the pinion shaft about 0.005" (0.13 mm).) The mounting flange should be
shimmed until the face of the teeth have full contact.
6.
Torque the 5/8" bearing bolts or the 5/8" bearing nuts as specified on page 3-28.
Torque the 3/4” gearbox bolts (4) to 200 foot-pounds (270 N-m) (see torque chart).
Then tighten the jackscrews (4) tightly against the gearbox flange and set the lock
nuts.
7.
Install the turntable subassembly with gearbox and bearing included on the chassis
frame. Torque the outer race 5/8" bolts and nuts as specified on page 3-28.
8.
During test of the machine and with the bearing teeth lubricated, check the tooth
match between the gear and pinion teeth. If full tooth contact is not apparent, add
additional shims to the gearbox flange as required.
Summary of Contents for RT-300-2G
Page 6: ...1 2 DIMENSIONAL DATA Courtesy of Crane Market...
Page 7: ...1 3 RT 300 2G TURNING DIMENSIONS Courtesy of Crane Market...
Page 16: ...Courtesy of Crane Market...
Page 24: ...2 8 Courtesy of Crane Market...
Page 33: ...2 17 CAPACITY CHART FOR RT 300 2G Courtesy of Crane Market...
Page 34: ...2 18 CAPACITY CHART FOR RT 300 2G METRIC Courtesy of Crane Market...
Page 55: ...3 9 Courtesy of Crane Market...
Page 66: ...Courtesy of Crane Market...
Page 67: ...Courtesy of Crane Market...
Page 88: ...Courtesy of Crane Market...
Page 89: ...Powered by TCPDF www tcpdf org Courtesy of Crane Market...