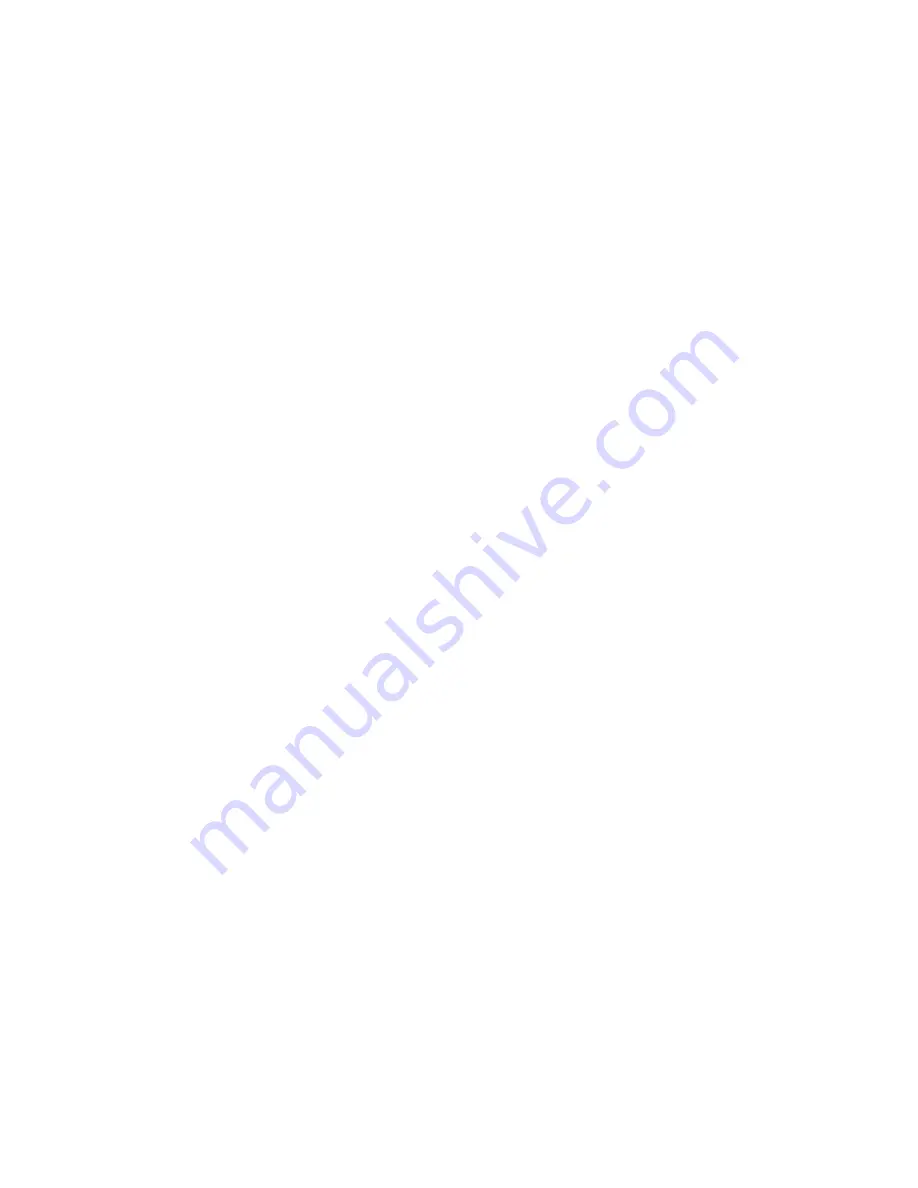
3-19
c. The boom will lower during this procedure. Ensure no personnel are in
potential pinch points, especially around the topping cylinder and between
turret side plates. Ensure that the boom is free of obstructions. Ensure that
the hook will not hit the ground and foul the hoist line.
d. Find the small hoses that connect to the piston sides of the cylinders, and
follow back to the RCL computer. Find the hoses that connect to the rod
sides of the cylinders, and follow back to the computer.
e. Loosen the piston-side fitting at the computer until the boom begins to lower.
Allow the boom to lower 1-2 degrees, or until no more air appears to be
leaking out. Then re-tighten the fitting. Use a bucket or other means to
catch as much oil as possible. If little or no air is present in the line, the
boom may not visibly lower before the line is purged.
f. Loosen the rod-side fitting at the computer. The boom should not move.
g. Start the engine.
h. SLOWLY lower the boom until no more air is leaking out of the rod-side
fitting. Oil may come out of the fitting before the boom begins to move. Use
a bucket or other means to catch as much oil as possible.
i. Re-tighten the rod-side fitting.
j. Turn off the engine.
11. Check the level of oil in the hydraulic reservoir and add more if necessary.
12. Set the crane on outriggers. With the boom about halfway extended and about 45°
elevated, lift a load near maximum capacity using the hoist. Raise the boom an
additional 10-15°. Extend the boom. Check for “spongy” operation.
13. If necessary, cycle functions again to remove remaining air.
HYDRAULIC SYSTEM
The RT-300 hydraulic system consists of three open-center circuits, driven by a triple vane
pump. The 40-gallon-per-minute (151 L/min.) section of the pump supplies the three-spool
control valve that controls the intermediate speed hoist and crowd and the boom topping
functions.
The 28-gallon-per-minute (106 L/min.) section supplies the seven-spool control valve (8
spools with auxiliary winch option), which controls the slow speed hoist and crowd and the
swing and outrigger functions. The 28-gpm (106 L/min.) circuit also includes the steering
system, in series, ahead of the seven-spool valve. The steering system is a load-sensing,
demand-type system that takes as much flow as required for steering.
The 14-gpm (53 L/min) section supplies the brake system. The flow passes through an
unloading valve. If the brake system pressures are adequate, the flow is diverted back to
tank to avoid placing unnecessary load on the engine. If the brake system pressures are
low, the unloading valve shifts and allows flow into the brake system accumulators. The
two accumulators are separated in a front/back split, such that each provides flow either to
the front or rear brakes. Flow and pressure to the brake calipers is controlled by a valve
directly connected to the foot pedal in the cab.
The schematic of the hydraulic system is shown on the next page. The steering system is
also shown separately on the following page for clarity. The transmission has its own
hydraulic system that is shown in the transmission maintenance section.
Summary of Contents for RT-300-2G
Page 6: ...1 2 DIMENSIONAL DATA Courtesy of Crane Market...
Page 7: ...1 3 RT 300 2G TURNING DIMENSIONS Courtesy of Crane Market...
Page 16: ...Courtesy of Crane Market...
Page 24: ...2 8 Courtesy of Crane Market...
Page 33: ...2 17 CAPACITY CHART FOR RT 300 2G Courtesy of Crane Market...
Page 34: ...2 18 CAPACITY CHART FOR RT 300 2G METRIC Courtesy of Crane Market...
Page 55: ...3 9 Courtesy of Crane Market...
Page 66: ...Courtesy of Crane Market...
Page 67: ...Courtesy of Crane Market...
Page 88: ...Courtesy of Crane Market...
Page 89: ...Powered by TCPDF www tcpdf org Courtesy of Crane Market...