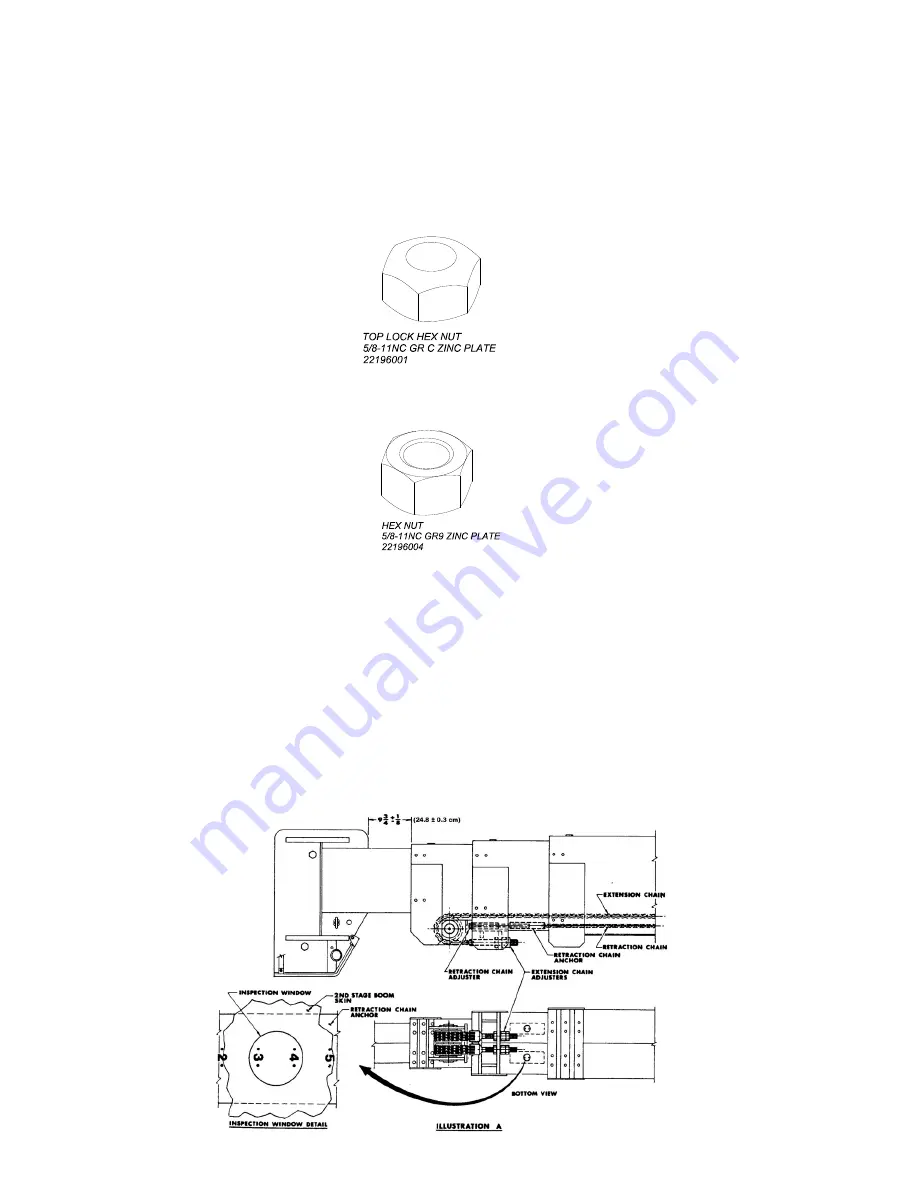
3-28
MECHANICAL ADJUSTMENTS
GENERAL
All fasteners in the RT-300 should be checked, and retightened if required, as a part of the
preventive maintenance program. Particular attention should be given to the axle mounting
bolts, outrigger bolts, pump mounting bolts, rotation bearing bolts, rotation gearbox bolts
and winch bolts. All bolts used in assembly are heat-treated Grade 5 or 8. Torque the
wheel nuts to 475 ft.-lbs. (645Nm). Torque the rotation bearing fasteners as shown below.
Top locking nuts can be identified by the curved top surface. Torque the rotation bearing
mounting bolts to 180 foot-pounds (245Nm) while holding the nuts stationary – or torque
the nuts to 150 foot-pounds (200Nm) while holding the bolts stationary.
Grade 9 hex nuts can be identified by the flat top surface. Torque the rotation bearing
mounting bolts to 175 foot-pounds (240 Nm) while holding the nuts stationary – or torque
the nuts to 140 foot-pounds (190 Nm) while holding the bolts stationary
CROWD CHAIN ADJUSTMENT AT TIME OF ASSEMBLY
Before boom assembly, an exact measurement of the crowd extension and retraction
chains must be determined. Exact length, number of pitches and end configuration must
be assured. (Reference Illustration B)
The 3/8" (1 cm) hardened pins (extension) and 5/16" (8 mm) hardened pins (retraction)
used to secure the chains to the attaching components must be a snug drive fit.
(Reference Illustration B)
Summary of Contents for RT-300-2G
Page 6: ...1 2 DIMENSIONAL DATA Courtesy of Crane Market...
Page 7: ...1 3 RT 300 2G TURNING DIMENSIONS Courtesy of Crane Market...
Page 16: ...Courtesy of Crane Market...
Page 24: ...2 8 Courtesy of Crane Market...
Page 33: ...2 17 CAPACITY CHART FOR RT 300 2G Courtesy of Crane Market...
Page 34: ...2 18 CAPACITY CHART FOR RT 300 2G METRIC Courtesy of Crane Market...
Page 55: ...3 9 Courtesy of Crane Market...
Page 66: ...Courtesy of Crane Market...
Page 67: ...Courtesy of Crane Market...
Page 88: ...Courtesy of Crane Market...
Page 89: ...Powered by TCPDF www tcpdf org Courtesy of Crane Market...