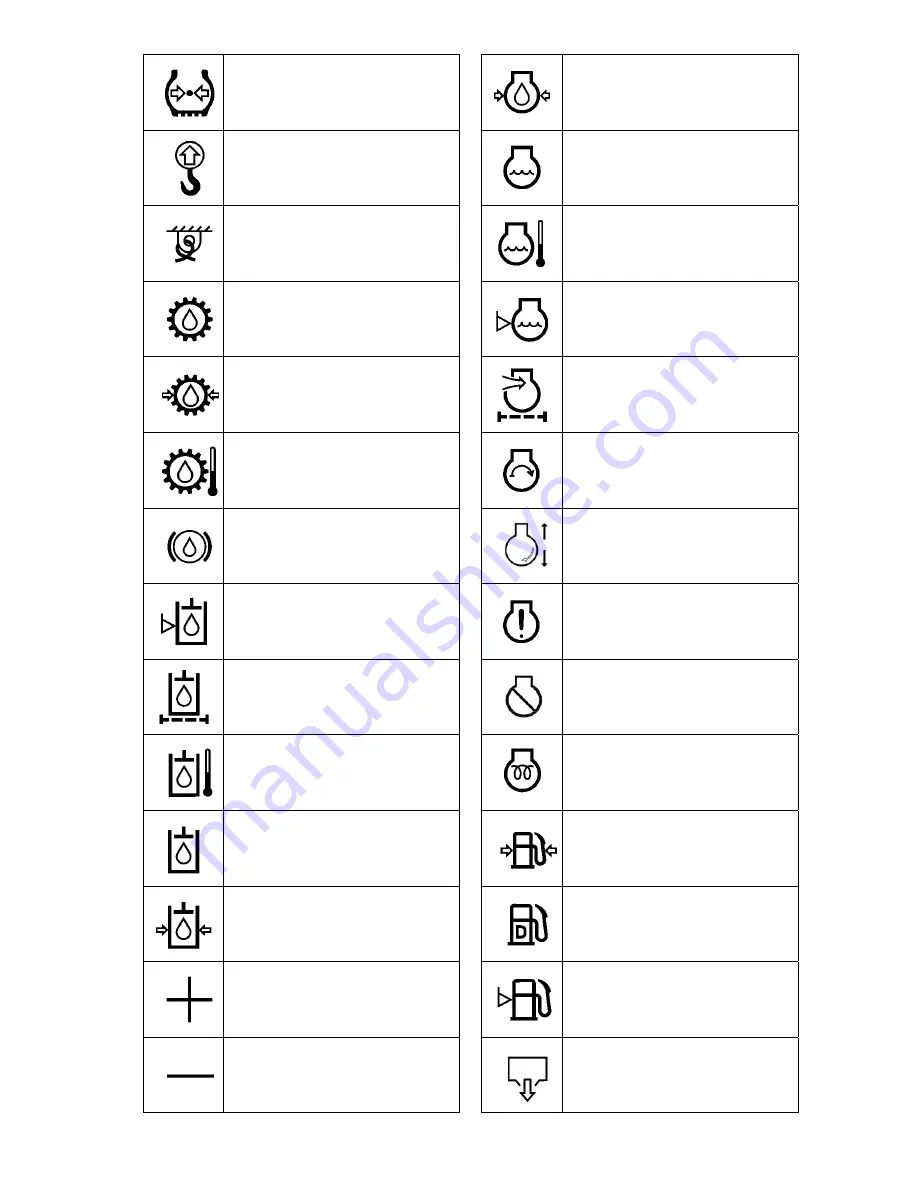
2-2
9
Tire pressure
Engine oil pressure low
Lift point
Engine coolant fill location
Tie-down point
Engine coolant
temperature high
Transmission oil fill location
Engine coolant low level
mark
Transmission oil pressure
Engine air filter restriction
indicator
Transmission oil
temperature
Engine start
Brake fluid fill location
Engine idle set
Hydraulic oil low-level mark
Check engine
Hydraulic oil filter
restriction indicator
Stop engine
Hydraulic temperature
gauge
Wait to start/ engine
preheat/ grid heater/ glow
plug switch
Hydraulic oil temperature
high
Gas fuel only
Hydraulic oil pressure
gauge OR hydraulic oil
pressure low
Diesel fuel only
Positive polarity
Fuel level gauge
Negative polarity
Drain
Summary of Contents for IC-80-3L 4X2
Page 6: ...1 2 IC 80 1L DIMENSIONS Courtesy of CraneMarket com...
Page 7: ...1 3 IC 80 2L DIMENSIONS Courtesy of CraneMarket com...
Page 8: ...1 4 IC 80 3L DIMENSIONS Courtesy of CraneMarket com...
Page 9: ...1 5 IC 80 L TURNING DIMENSIONS Courtesy of CraneMarket com...
Page 20: ...Courtesy of CraneMarket com...
Page 36: ...2 16 Courtesy of CraneMarket com...
Page 37: ...2 17 Courtesy of CraneMarket com...
Page 38: ...2 18 Courtesy of CraneMarket com...
Page 57: ...3 8 IC 80 LUBRICATION CHART Courtesy of CraneMarket com...
Page 62: ...3 13 Courtesy of CraneMarket com...
Page 63: ...3 14 Courtesy of CraneMarket com...
Page 73: ...Courtesy of CraneMarket com...
Page 74: ...Courtesy of CraneMarket com...
Page 75: ...Powered by TCPDF www tcpdf org Courtesy of CraneMarket com...