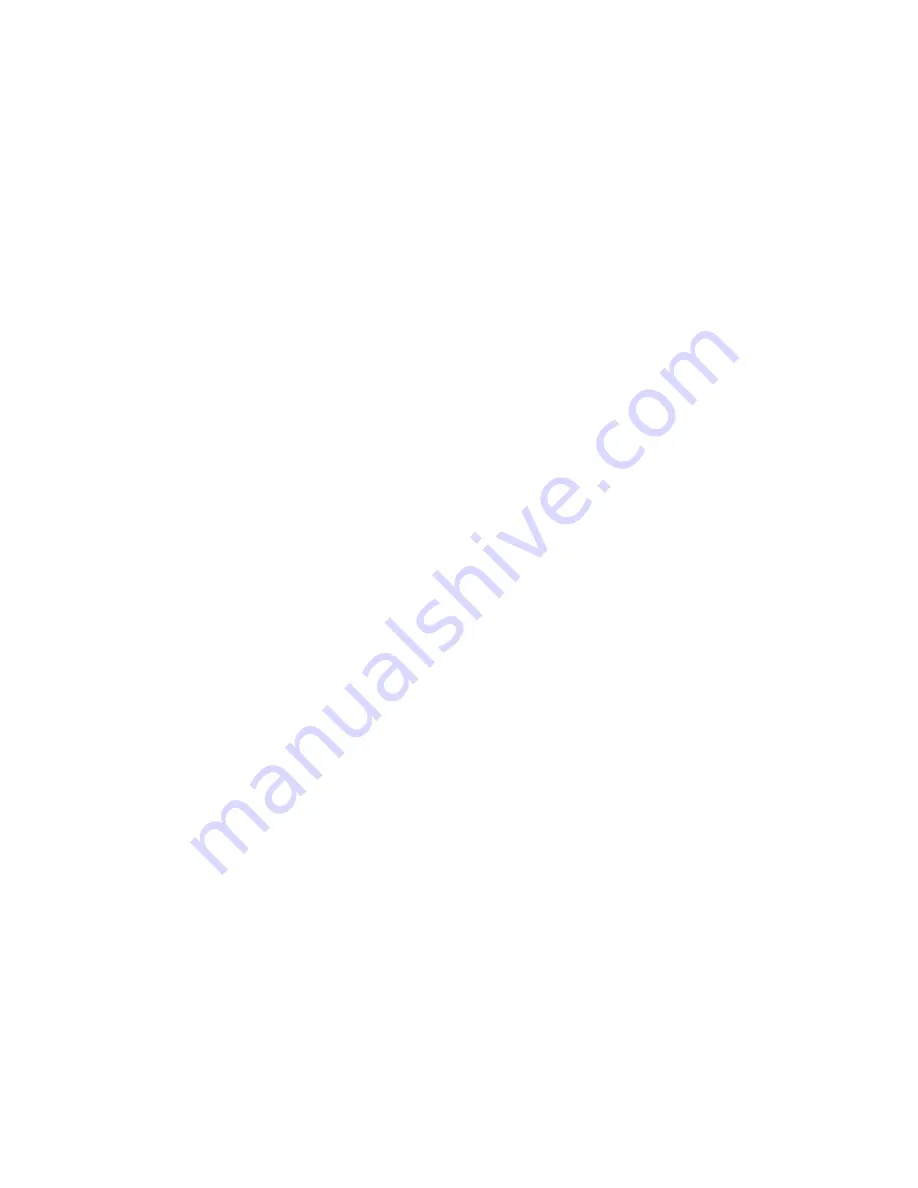
3-2
16. Use a hoist when lifting components that weigh 50 pounds (23 kg) or more. Follow
all hoist and rigging safety rules.
17. Do not use lower grade fasteners if replacements are necessary.
18. When reinstalling wiring or plumbing after repairs, be sure that it will not be
damaged by rubbing against sharp, rough or hot surfaces or edges.
19. Never use a rope clip on live side of the load hoist rope. This will seriously weaken
the rope. Death or serious injury can result from the use of a rope clip on the hoist
rope.
20. Replace any instruction or warning placards that are lost or damaged.
21. Always replace all guards and covers after working on the crane.
22. After working on the hydraulic system, remove air from the lines and cylinders
involved by cycling them full stroke with the engine running until the functions
operate smoothly.
23. When welding on the crane or on anything connected to the crane by wire rope or
other conducting link, disconnect the battery, the Rated Capacity Limiter display
and computer and the engine electronic control module. When welding on the
boom or turntable assembly, remove the cable reel and any other electronic
components bolted to these assemblies.
24. When using pressure spray to clean the crane, cover all electronic components
with sheets of plastic to protect them from spray.
Summary of Contents for IC-35-2F
Page 7: ...1 2 DIMENSIONS AND ORIENTATION IC 35 2F Courtesy of Crane Market...
Page 8: ...1 3 TURNING DIMENSIONS Courtesy of Crane Market...
Page 17: ...Courtesy of Crane Market...
Page 29: ...2 12 CRANE CAPACITY CHART FOR IC 35 2F Courtesy of Crane Market...
Page 30: ...2 12M CRANE CAPACITY CHART FOR IC 35 2F METRIC Courtesy of Crane Market...
Page 31: ...Courtesy of Crane Market...
Page 39: ...Courtesy of Crane Market...
Page 47: ...3 8 IC 35 LUBRICATION CHART Courtesy of Crane Market...
Page 51: ...3 12 JIC SCHEMATIC Courtesy of Crane Market...
Page 52: ...3 12M JIC SCHEMATIC METRIC Courtesy of Crane Market...
Page 53: ...Courtesy of Crane Market...
Page 55: ...3 14 STEERING SYSTEM Courtesy of Crane Market...
Page 57: ...3 16 IC 35 PROPULSION SYSTEM Courtesy of Crane Market...
Page 71: ...Powered by TCPDF www tcpdf org Courtesy of Crane Market...