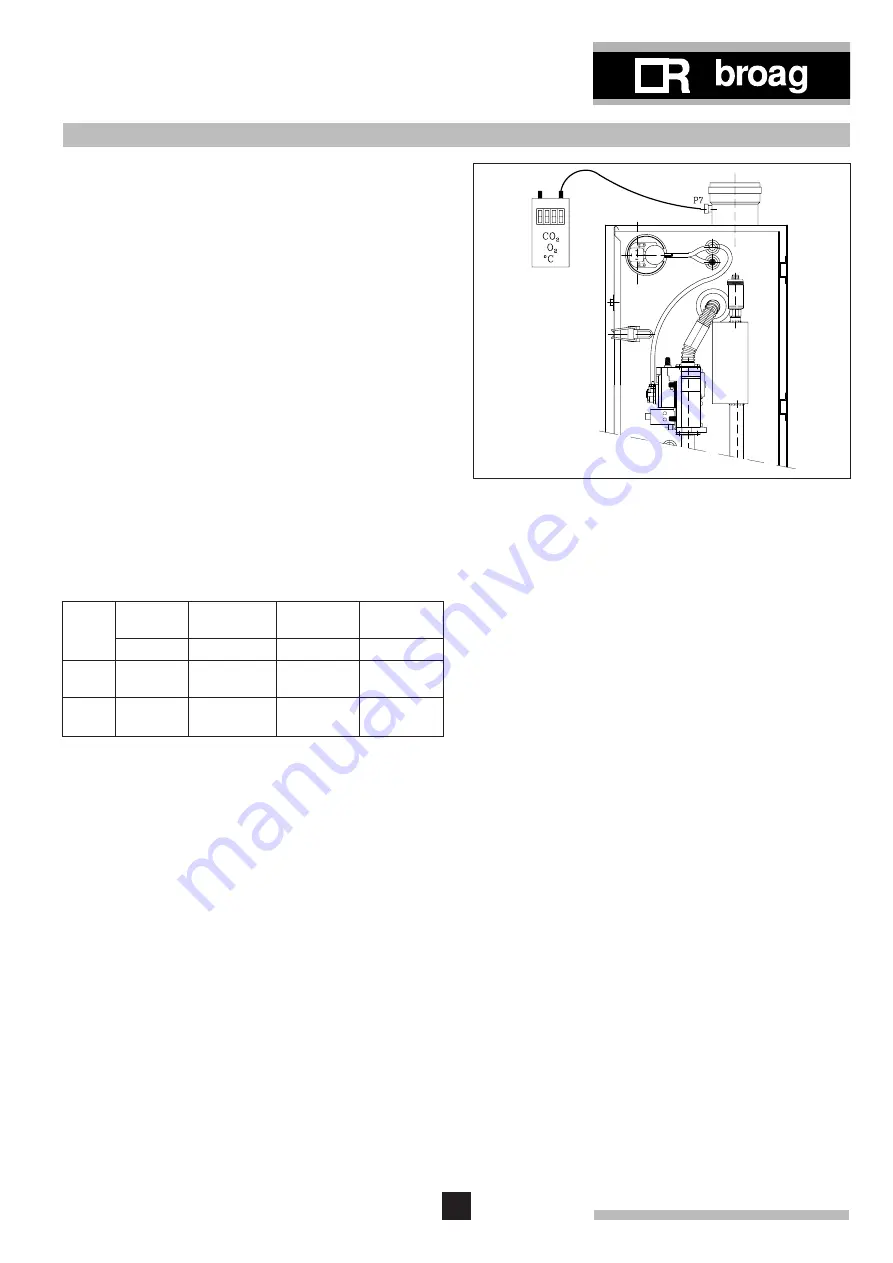
37
12. INSPECTION AND SERVICING INSTRUCTIONS
12.1 General
The remeha W40/60-m ECO is practically maintenance-
free. Once a year, the appliance should be checked and
if necessary cleaned.
12.2 Inspection
The annual inspection of the remeha W40/60-m ECO
can be limited to:
- inspection of the boilers combustion characteristics
- cleaning the siphon
- setting the ignition electrode
- check for leaks (water side, flue gas side and gas side)
- water pressure check.
Checking the boiler combustion characteristics
This can be done by measuring the O
2
level in the flue
gas
(P7, fig 24). The boiler should be in equilibrium with
an average boiler water temperature of approximately
70°C.
The flue gas temperature can also be taken at P7.
This flue gas temperature must not exceed the return
water temperature by more than 30°C.
If this check shows the operation of the unit to have
deteriorated clean the boiler as detailed in para. 12.3.
Fig. 24 Measuring points
W40-m
W60-m
boiler
model
kW
input
(NCV)
18.6
62.1
12.7
42.3
4.8
4.8
%
O
2
4.8
4.8
9.0
9.0
%
CO
2
9.0
9.0
fan
speed
approx. 3000
approx. 4900
approx. 3000
approx. 4900
rpm
The above values apply to a closed air box.
See also para. 10.1 for initial settings.
Cleaning the siphon
Remove the siphon and clean it. Fill the siphon with
clean water and fit it.
Setting the ignition electrode
Check the setting of the ignition electrode (3-4 mm).
Water pressure check
The water pressure should be at least 0.8 bar. You are
recommended to fill the appliance to approx. 1.5 bar.