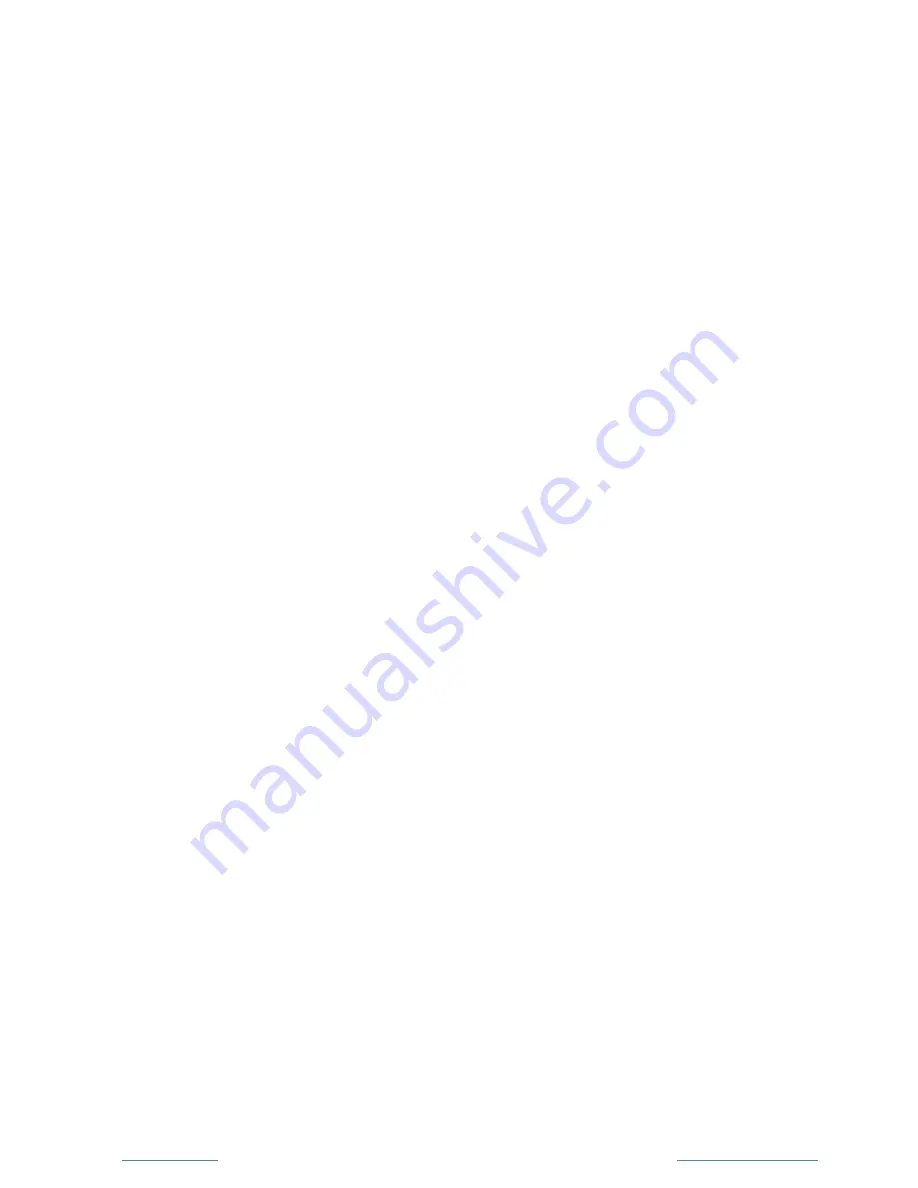
CJWinter Page 14
Work Piece (Blank) Preparation
Prior to knurling, the work piece needs to be prepared. Typically, the blank
needs to be turned to a diameter approximately halfway between the major
OD and Minor OD of the finished knurled part. To start, you may want to bias
this diameter about .003"/inch smaller, so that the dies do not overfill. This
can later be adjusted upwards to get the proper amount of fill, and achieve the
desired Major diameter. The lead-in chamfer should typically be a flat 30°
(measured from the part axis), and should extend down below the minor
diameter of the part. Failure to properly chamfer your blank will lead to
premature roll breakage. Surface finish should be 125 RMS or better, and the
tolerance held on the pre-knurl blank diameter should be roughly 1/3 of the
tolerance on the finished knurl major diameter. Adjustments made to the
blank diameter should be small, since there is a roughly 3 to 1 relationship
between blank diameter and the finished major diameter. The knurl can
extend into an undercut, or terminate right on the blank diameter prior to a
shoulder. It should be noted that each knurl roll has a lead-on chamfer. Unless
a sufficient undercut is present in the blank, the knurl roll will leave a partially
incomplete section of knurl at the inboard end of the part knurl surface. The
size of this incomplete section is variable by the Knurl Roller design, but shorter
knurl chamfers tend to diminish the life of the roll. Consult with our application
specialists for your particular application.
Work Piece Materials
Knurl Rolling can be performed on almost any ductile metal material under
Rc40. Some materials roll better than others. For questions on the rollability
of your particular part, please consult with our application specialists.