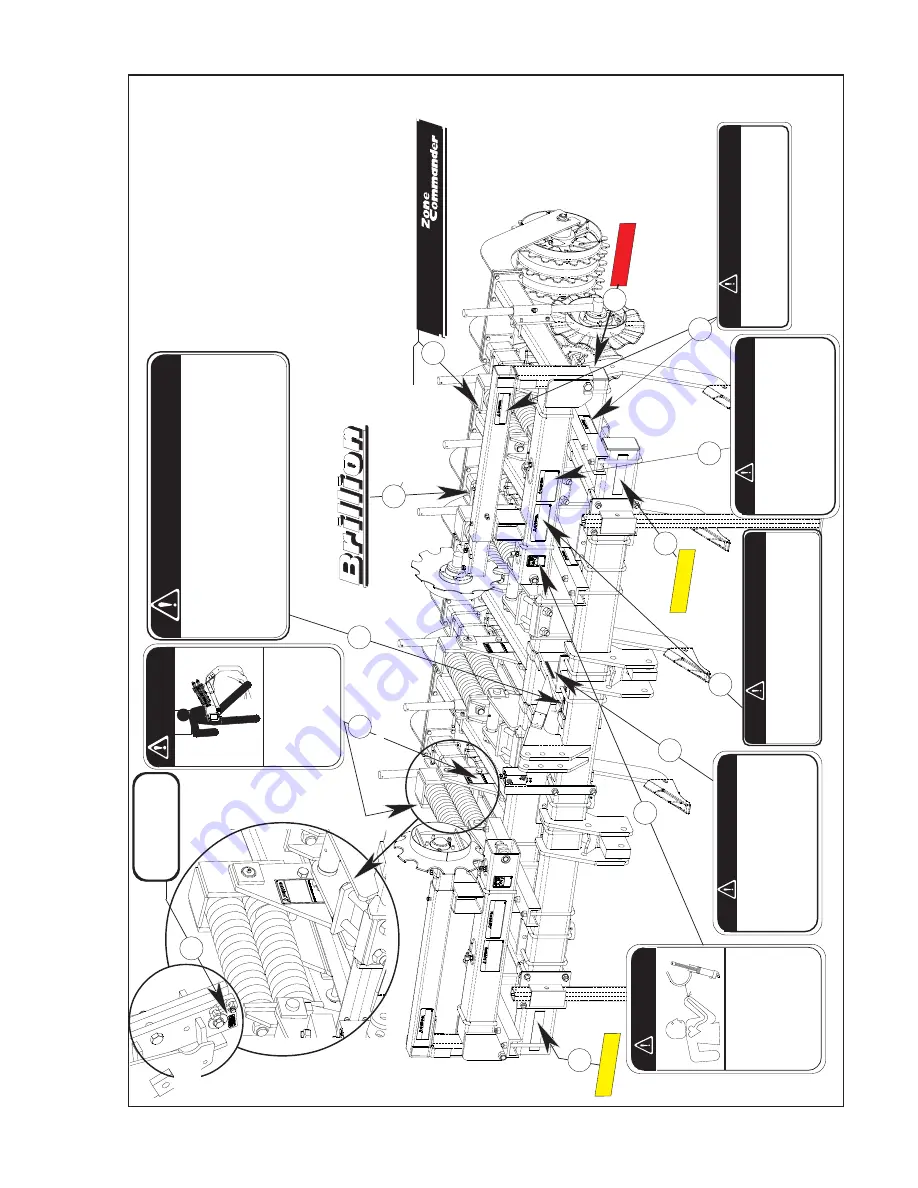
6K689
Page 9
1
.
8J310 - Caution List
2
.
6K883 - Shank Under Load
3
.
2J431 -
Amber Reflective
4
.
2J430 - Red Reflective
5
.
6K800 - Zone Commander
6
.
4K103 - Brillion
7
.
3K706 - Hydraulic Leak Hazard
8
.
3J678 - Bleed
Air from Cylinders
9
.
9J629 - W
atch for Electrical W
ires
10.
3J675 - Falling Wings
13.
9K829 - Deep
T
ill Caution
14.
9K129 - Shear Bolt decal
On Drawbar (Pull-type only -See pg. 5)
11
.
7K956 - Loss of Control W
arning
12.
7K957 - Drawbar Light Caution
SHANK IS ALWAYS UNDER LOAD
DO NOT USE HANDS OR FEET
TO DISLODGE ANY
OBSTRUCTION HOLDING THE
SHANK IN THE
TRIPPED POSITION
SHANK IS SPRING LOADED
6K883
AND SERIOUS INJURY
COULD
RESULT AS SHANK RESETS
W
ARNING
Both
Sides
2
Rear-
Both Sides
On RearFrame
Between Shanks
6
1
3
DANGER
WATCH FOR ELECTRICAL WIRES AND
OTHER OVERHEAD OBSTRUCTIONS
WHEN FOLDING WINGS.
FAILURE TO HEED THESE WARNINGS
MAY RESULT IN PERSONAL INJURY OR
DEATH.
9J629
4
DANGER
FALLING WINGS CAN CAUSE INJURY
OR DEATH. STAND CLEAR WHEN WINGS
ARE BEING RAISED OR LOWERED.
3J675
9
8
10
1200
rev2-10-04
Both Row Markers and
all channel mount
s
Page 7
1. DO NOT LUBRICATE, ADJUST OR REPAIR WHEN MACHINE IS IN MOTION.
2. DO NOT TOW OR TRANSPORT FASTER THAN 15 MILES PER HOUR.
3. DO NOT RIDE OR ALLOW OTHERS TO RIDE ON THE MACHINE.
4.
BLOCK UP ALL HYDRAULICALLY OR MECHANICALLY RAISED COMPONENTS
T
O
PREVENT UNINTENDED LOWERING OR LOWER THE MACHINE TO THE GROUND TO
MAKE ADJUSTMENT OR REPAIRS WHEN NOT IN USE.
5. KEEP ALL PERSONS AWAY FROM MACHINE DURING HITCHING AND OPERATING.
6. SLOW DOWN BEFORE MAKING SHARP TURNS OR USING THE BRAKES.
DRIVE SLOWLY OVER ROUGH GROUND, SIDE HILLS, AND AROUND CURVES TO AVOID TIPPING.
7. COMPLY WITH ALL LAWS WHEN TRANSPORTING THE MACHINE ON PUBLIC ROADWAYS.
8. INSTRUCT ALL OPERATORS IN THE SAFE OPERATION OF THE MACHINE.
REVIEW THE OPERATOR’S MANUAL FOR CORRECT PROCEDURES.
9. BLOCK IMPLEMENT TO PREVENT MOVEMENT WHEN UNHITCHED FROM TRACTOR.
10.
KEEP ALL GUARDS AND SHIELDS IN PLACE WHILE MACHINE OR PARTS ARE IN MOTION.
CAUTION
DO NOT GO NEAR LEAKS
HIGH PRESSURE OIL EASILY PUNCTURES
SKIN CAUSING SERIOUS INJURY,
GANGRENE OR DEATH.
IF INJURED, SEEK EMERGENCY MEDICAL
HELP. IMMEDIATE SURGERY IS
REQUIRED TO REMOVE OIL.
DO NOT USE FINGERS OR SKIN TO
CHECK FOR LEAKS.
LOWER LOAD OR RELIEVE HYDRAULIC
PRESSURE BEFORE LOOSENING FITTINGS.
10813A
W
ARNING
3
CAUTION
DEEP TILL OPERATION CAN DAMAGE
UNDERGROUND UTILITIES CAUSING
DANGEROUS CONDITIONS AND
DISRUPTING SERVICES. DETERMINE
THE DEPTH AND LOCATION OF BURIED
CABLES, PIPE LINES, AND DRAIN
TILES BEFORE OPERATION.
8K829
DANGER
BLEED THE AIR FROM WING LIFT CYLINDERS
BEFORE OPERATING. FAILURE TO DO SO WILL
ALLOW WINGS TO FREE-FALL AND MAY CAUSE
SERIOUS PERSONAL INJURY. SEE OPERATOR’S
MANUAL FOR CORRECT PROCEDURE.
3J678
Side of
Shank
Mt.
IMPORT
ANT
USE GRADE 2 BOL
T
A
T
THIS LOCA
TION
9K129
14
5
Figure 2B
13
7