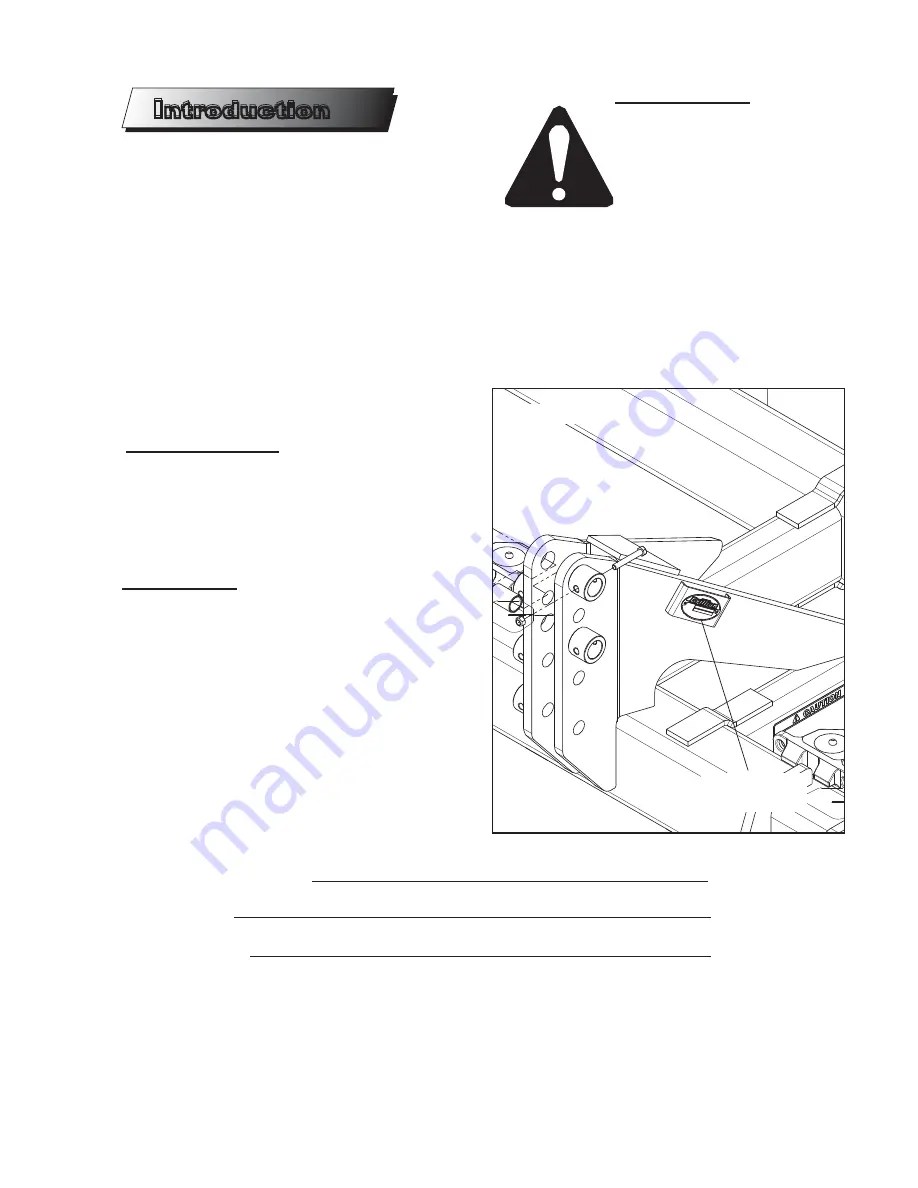
Pa
g
e
5
The
Brillion Zone Commander
was designed
as a primary tillage tool imparting minimum soil
disturbance and soil eroison while providing ex-
cellent break-up of compacted soil, lifting it up
enough to promote air and water absorption.
To obtain maximum benefits, please study this
manual carefully before operating or starting as-
sembly of machine or optional equipment.
If items covered in this manual are not under-
stood, contact your local Brillion dealer.
This safety alert symbol
is used to call your
attention to instructions
concerning
personal
safety. This symbol is found throughout this
manual and will be found on safety signs on
your machine. It points out important safety
precautions. It means
“ATTENTION! BE
ALERT! YOUR SAFETY IS INVOLVED!”
Read the message that follows and be alert to
the possibility of personal injury or death.
SAFETY ALERT
Location Reference
Right hand, left hand and forward designations
are those related to the operator when sitting in
the operating position.
Be sure to read the warranty form which is
shipped with the machine. Return the proper
portion of the form for recording at the factory.
Parts Ordering
When ordering parts for this machine, include
the complete model number and serial number.
Refer to the name plate on the inside of the
frame’s right hand end plate. Please record
these numbers upon taking delivery of the unit.
Zone Commander Model
Serial Number
Date Purchased
Figure 1
Nameplate
located here.
I
ntroduction
I
ntroduction
9K162
504
Page 3
Summary of Contents for Zone Commander ZM3302
Page 2: ...Page 2 ...
Page 4: ...Page 4 ...
Page 25: ...Page 25 ZS8302 DUAL COULTER PLACEMENT BY MODEL 9K320 9K377 9K320 9K376 9K162 504rev7 13 05 ...
Page 41: ...Page 41 9K162 504 Page 29 This Page Left Blank Intentionally ...
Page 49: ...Page 49 7K925 Ductile Wheel Kit or or 7K924 Optimizer Wheel Kit 9K162 504 Page 37 ...
Page 52: ...Page 52 ...
Page 53: ......