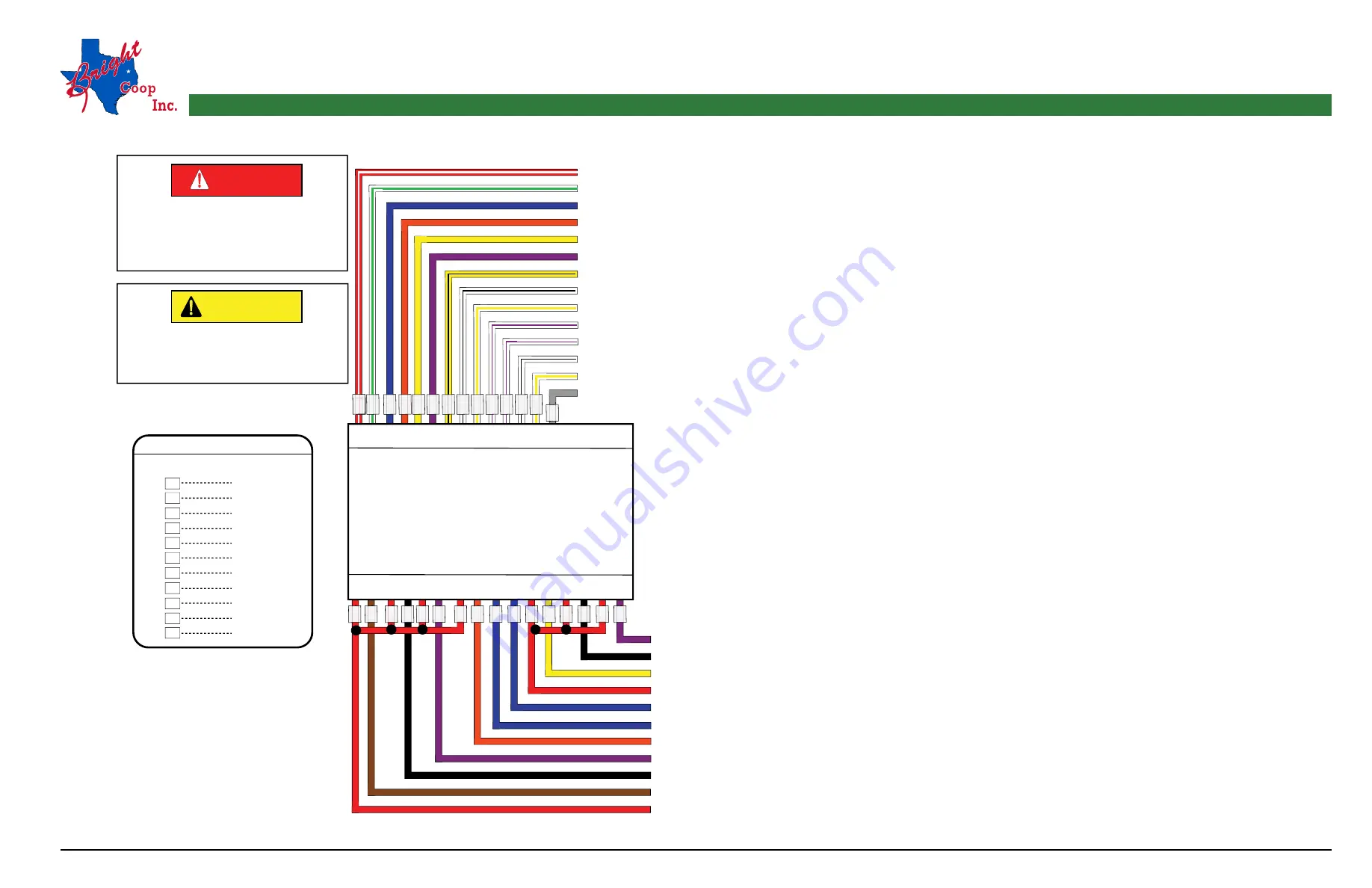
Schematics
Cage Unloading System
73
ELECTRICAL SCHEMATIC SMART RELAY (091-21961W)
I/O DESCRIPTION FOR PROGRAMMABLE RELAY DATED - JUNE-2012
Wire with Two Letters
is Striped
WIRE COLOR CODE CHART
COLOR CODE - DESCRIPTION
A
B
C
D
E
F
G
H
M
N
R
ORANGE
WHITE
PINK
GREY
GREEN
BLUE
YELLOW
PURPLE
BROWN
BLACK
RED
24V DC+ (FROM BLOW FUSE 1A)
24 V DC- (FROM POWER SUPPLY)
FENCING GATE SENSOR 1 (MUST BE ON WHEN THE GATE IS CLOSED)
FENCING GATE SENSOR 2 (MUST BE ON WHEN THE GATE IS CLOSED)
FENCING GATE SENSOR 3 (MUST BE ON WHEN THE GATE IS CLOSED)
FENCING GATE SENSOR 4 (MUST BE ON WHEN THE GATE IS CLOSED)
OPERATOR GATE SENSOR (MUST BE ON WHEN THE GATE IS CLOSED)
NOT USED
NOT USED
NOT USED
WASHER CRADLE (MUST BE ON WHEN THE CRADLE IS IN THE POSITION)
WASHER CARRIAGE HOME POSITION (MUST BE ON WHEN THE CARRIAGE IS HOME)
WASHER CARRIAGE END OF TRAVEL POSITION (MUST BE ON WHEN THE CARRIAGE IS IN THE END OF TRAVEL POSITION)
RESET SWITCH (TURN ON WHEN DEPRESSING THE RESET BUTTON)
WATER VALVE SOLENOID (ENERGIZED WHEN THE CARRIAGE IS IN MOTION)
WASHER CARRIAGE REVERSE SOLENOID (MOVES CARRIAGE FORM END OF TRAVEL TO HOME POSITION)
WASHER CARRIAGE FORWARD SOLENOID (MOVES CARRIAGE FROM HOME TO END OF TRAVEL POSITION)
120V AC (L) (FROM WATER PUMP SWITCH IN CONTROL PANEL))
NOT USED
NOT USED
CRADLE SELECTOR SWITCH POWER
NOT USED
NOT USED
NOT USED
120V AC (L) (FROM MAIN 10A BREAKER)
SMART RELAY FOR UNLOADING SYSTEM
WITH WASHER
(091-21961W)
+ _ |1 |2 |3 |4 |5 |6 |B |C |D |E |F |G _ _
1 2 1 2 1 2 1 2 1 2 1 2 1 2 1 2
Q2
Q1
Q3 Q4
Q5
Q6 Q7
Q8
RB BE
A G
GN BN BG BH
F
R
R N R H
A F F
BG D
M
R G R N
H
BH BN
H
R
R
NEVER ATTEMPT TO SERVICE OR
MAINTAIN THE UNLOADING SYSTEM IF
THE MAIN POWER SOURCE IS
ENERGIZED. USE PROPER LOCKOUT/
TAGOUT PROCEDURES.
DANGER
This Smart Relay Schematics
contains 120 Volt AC+ and 24 Volt
DC- Wiring.
CAUTION