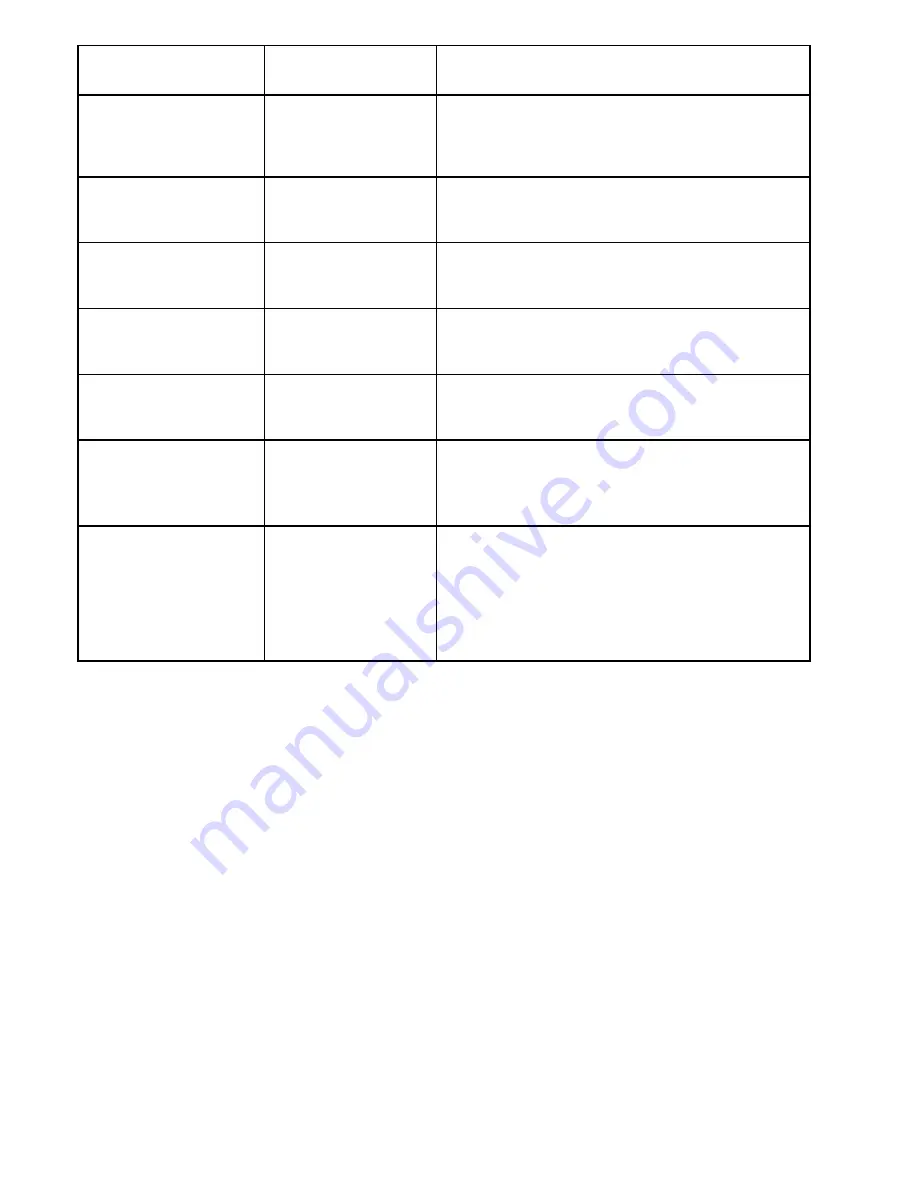
Adjuster cables are
breaking or fraying.
Cables windings too
loose.
See Service Bulletin #4.
Wall keeps rolling "under"
the climber's foot.
Harness line adjusted
improperly
Make sure harness line is pulled tight through the
line-locks before climbing.
Wall sways side-to-side.
Internal x-bracing too
loose.
Tighten Internal x-bracing. Do not over-tighten.
Tighten until just firm and adjust for panel end
clearance (See Service Bulletin # 22).
Hold rotates.
Hold bolts not
sufficiently tightened.
Re-check hold bolts; re-tighten if necessary.
Wall too far to one side
(not centered in frames).
Main (external)
X-bracing needs
re-adjustment.
See Service Bulletin # 2.
Hydraulic Assembly leaks
oil.
Valve gland-nut loose.
See Service Bulletin # 6.
Cord has too much friction.
Cord is frayed or broken
inside top pulley bar.
Cord is off pulley
See Service Bulletin # 8
Counter will not count
Battery in counter needs
replacement (no display)
Microswitch needs
adjustment or is broken
Replace 9 volt battery - cover unscrews on back
See Service Bulletins #3 and 1.
The following Service Bulletins are included in this manual:
Service Bulletins # 1, 2, 3, 4, 6, 7, 8, 10, 13, 18,19, 20, 22, 23, 26, 27, 28, 30
These Bulletins are those that pertain to standard service issues. As needed, we develop further Service Bulletins
for specific tasks.
May, 1996
Summary of Contents for Treadwall AM
Page 32: ......