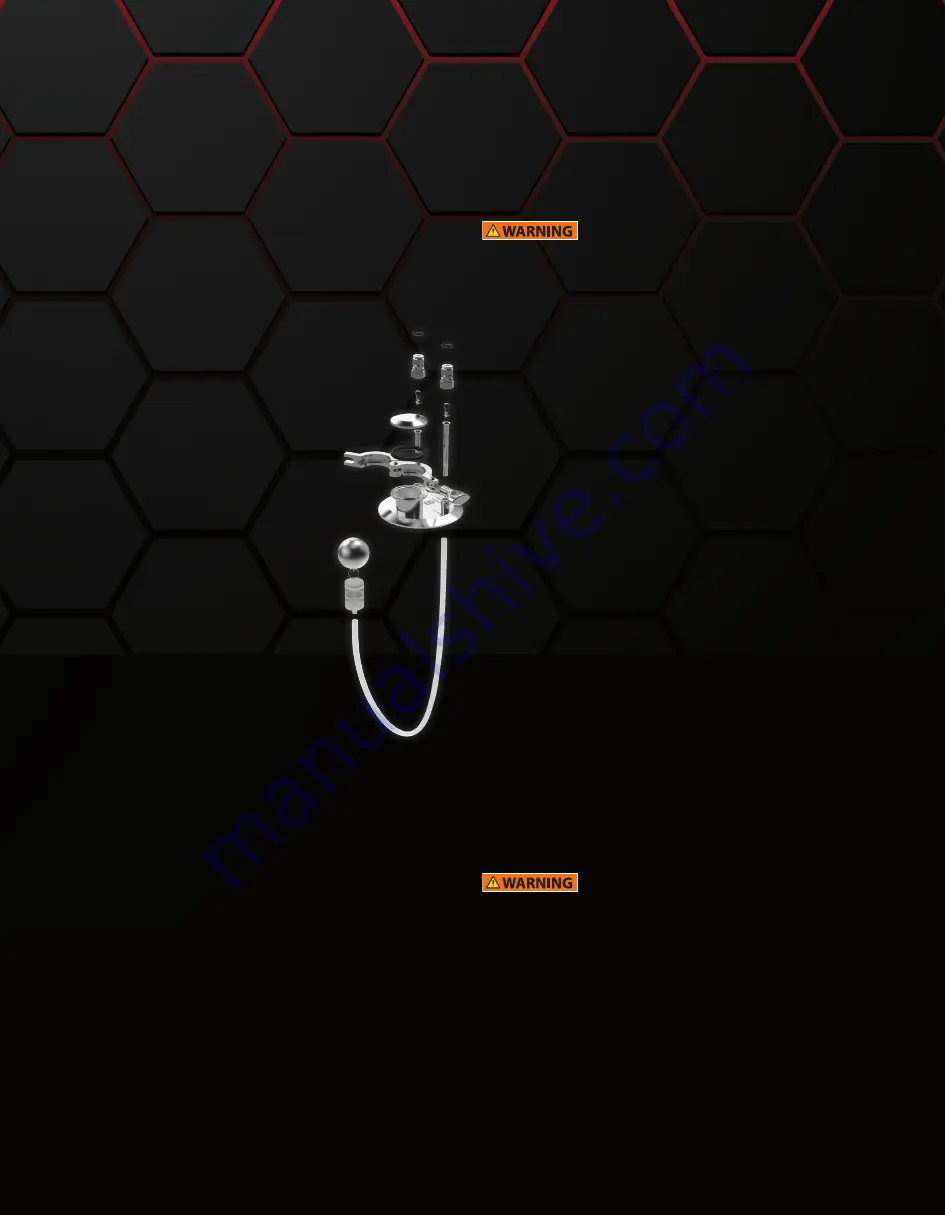
directly into the fermenter. Loose material can clog the blow off
and airlock. Use a mesh bag to contain these types of materials.
•
Do not alter or change the Pressure Relief Valve (PRV) built into
the lid.
•
Pressurize with compressed gas only with the BrewBuilt Kit
for Fermenting Under Pressure. Always use an approved CO
2
regulator, with a functional low-pressure gauge. Never exceed
15 PSI.
•
During fermentation, never close off/cap your X1 except when
using the BrewBuilt Kit for Fermenting Under Pressure.
•
When the optional BrewBuilt Flex Chamber is installed always
keep the bottom butterfly valve open, allowing CO
2
to be
released. Failure to keep the valve open could cause the Flex
Chamber to become over pressurized and explode.
The Pressure Pack, specifically designed to work
with BrewBuilt X1 Conical Unitanks, unlocks many
possibilities. Apply low pressure before cooling to
eliminate sucking oxygen back in. Use it to grab a sample
or transfer finished beer to a keg in a true oxygen-
free environment. The Clear Float allows sampling or
transferring of the clearest possible beer from
the top down! In this guide. Please read and
follow the additional instructions that come
with your Pressure Pack Kit.
INSTALLATION
Assemble the Pressure Pack lid per the
diagram. DO NOT USE TEFLON TAPE to
assemble threaded body connects as
they seal with the included o-rings. When
attaching the Pressure Pack lid to your X1
conical, be sure your TC gasket is properly
seated and then tighten down the TC clamp.
Follow instructions that come with your
Pressure Pack lid.
TIP:
A welded a hook on the bottom of the
Pressure Pack Lid can be used to hang drawstring
bags for flavoring additions.
APPLYING PRESSURE
FIRST TEST —
First take a moment and read the warnings above. For
safety we always recommend the first pressure test be made while
the conical is filled with water. After the conical is completely filled
with water, replace the u-shaped blowoff with an included TC end
cap. Before connecting CO
2
pressure be sure you have a working,
accurate regulator with a low pressure gauge. We recommend
setting your regulator to 1–2 psi to start with, and always less than
15 psi. Connect your gas-in ball lock QD on your CO
2
draft system
to the gas-in body connect located on the Pressure Pack. The gas-
in body connect has a notch on the side, while the beverage-out
body connect does not. With 1-2 psi applied to the conical, practice
releasing pressure by unthreading the PRV cap. Read the section
on releasing pressure slowly as instructed in the section ‘Releasing
Pressure’ below.
TRANSFERRING AND SAMPLING
The bev-out fitting is equipped with a unique floating dip tube that
will pull beer from the top rather than the middle or bottom of the
conical. We recommend using a ball lock jumper, a section of beer
line with a beverage-out QD at both sides, to transfer beer from
your X1 to the bottom of your keg. When applying pressure for
sampling or transferring start with a low pressure and increase only
as needed. Keep in mind that your X1 Uni and Pressure Pack lid are
rated at 15 psi and the PRV will start releasing pressure around this
point. Never apply more than 15 PSI to your X1.
TIP:
Filling your keg from the bottom up will keep splashing to a
minimum as beer will flow down the beverage dip tube and gently
fill the keg from the bottom up. Lastly, pull up the PRV ring on the
keg and set it in the open position to allow air (or CO
2
if you pre
purged the keg) to escape as your fresh beer flows in.
RELEASING PRESSURE
Before removing the lid clamp, TC fitting, or
any accessory, you must first release any pressure from your
BrewBuilt Fermenter.
Releasing pressure from your X1 can be achieved by loosening the
cap on the Pressure Relief Valve (PRV) that is built into the lid. Slowly
loosen the cap counterclockwise until you hear the release of any
CO
2
exiting the PRV. When the release has stopped, continue to
slowly unthread the cap. At any point while loosening the cap if
you hear additional CO
2
being released, stop and wait. When no
additional CO
2
is being released slowly remove the cap completely to
ensure that all pressure has been removed from the fermenter. Only
then is it safe to begin removing fittings or the lid clamp.
TRANSFER CLEAR BEER TO KEG UNDER PRESSURE
Push your finished beer into a keg using CO
2
so it never becomes
exposed to oxygen—it’s simple and fast using the Pressure Pack.
Thanks to the Clear Float stainless steel floating pick up, you’ll be
transferring the clearest beer from the top down.
Once your beer is ready to be packaged into a keg, follow these
instructions.
NOTE:
you will need a Corny Keg Ball Lock Jumper Line
(beverage tubing with bev-out ball lock connectors at both ends).
1. Fill your keg with sanitizer solution. Push the sanitizer out using
CO
2
. Open the keg pressure relief valve to let CO
2
exit the keg
during filling.
2. Attach your CO
2
tank to the gas-in post on your Pressure Pack lid
and set it to around 10–12 psi.
3. Attach the Corny Keg Ball Lock Jumper Line to the bev-out post
on your Pressure Pack lid.
4. Once you hook up the bev-out to the keg, beer will start flowing
from the pressurized X1 Unitank into the unpressurized keg.
5. Once your beer has transferred, unhook the bev-out and gas-in
connectors. Pressurize your keg.
6. Be sure to release any pressure from inside your X1 before open-
ing it for cleaning.
FERMENTING UNDER PRESSURE
Follow all special warnings and instructions
that come with the optional BrewBuilt Kit for Fermenting Under
Pressure. Do not pressure ferment without using the optional Kit for
Fermenting Under Pressure.
If you wish to ferment under pressure, or capture CO
2
at the end
of fermentation, you must use the optional BrewBuilt Pressure
Fermentation Hardware Kit. The optional hardware kit comes with
a commercial-grade pressure relief that connects to the 1.5” TC port
on the lid. It also comes with an adjustable spunding valve. The
spunding valve allows you to set a safe pressure to ferment. With
the BrewBuilt Kit for Fermenting Under Pressure installed, there are
three safety relief valves: the standard pressure relief valve welded
into the lid, the commercial 1.5” TC relief valve, and the PRV on the
Spunding Valve. The Fermentation kit includes a no-foam krausen
reducer, CellarScience
®
Foam-Axe to reduce the chance that krausen
could enter any of the PRVs.
BREWBUILT.COM
PAGE 7