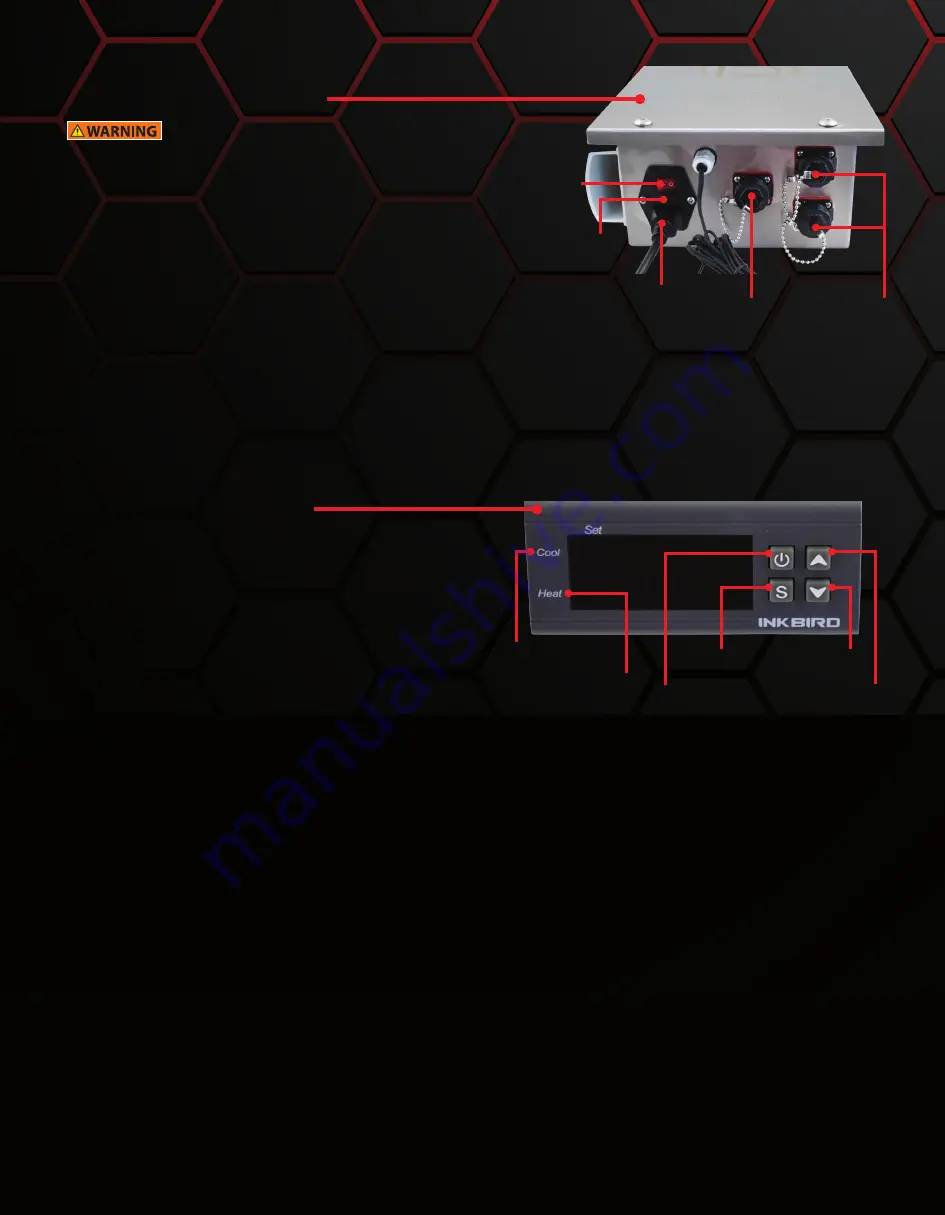
Connecting the Control Panel
To reduce the risk of fire or electrical shock, follow these warnings.
•
Always use a GFCI outlet rated at 15amps/110v/60z.
•
The GFCI will not supply power without a proper ground.
•
Do not use if there is any damage to the wiring.
•
Do not spray or immerse the control panel. To clean wipe with a damp
cloth when unplugged.
The BrewBuilt Control Panel has an included InkBird heating and
cooling controller and a 500 watt 12V DC power supply. It has a
tab welded to the top four screws and can be hung on a wall or one of our optional stainless controller stands (CONP735 &
CONP736). On the bottom of the box there are 4 sockets. One socket is for the power cord and it contains the power switch
and a fuse. There is a 3-pin connector for the heating element and two 2-pin connectors for the cooling. Depending on what
system you have you may only need one cooling connector.
The power connectors are sealed with a water-tight cap. It is best to leave the caps in place when not in use. The connectors
are polarity sensitive and will only go in one way. Once aligned correctly they push in and rotate clockwise 1/4 turn to lock.
COOLING
ON
POWER
UP
SET
DOWN
HEATING
ON
FACTORY SETTINGS:
•
tS
= Set Point = 68
•
CF
= Celsius/Fahrenheit = F
•
CA
= Calibration Offset = 0
•
Pt
= Compressor Delay = 0
•
dS
= Differential = 1
To change the settings hold the S button down till tS is showing (about 5 seconds). Using the up and down arrows find the
setting you wish to check or change and press S. Set the new value with the up and down buttons and press S when finished.
When all settings are correct press the power button to return to normal operation.
NOTE:
Changing from Celsius to Fahrenheit resets the other settings.
To set the Calibration offset, place the temperature sensor in a glass of ice water and stir till the reading is stable. Subtract 32
from the reading and change the sign. If it reads 34, subtract 32 to get 2, change the sign, and set the offset to -2. This allows
for changes in the resistance of the probe and connections.
Setting Your Temperatures
The controller in your control panel comes programmed
with a default setting of 68F, the most common
fermentation temperature for ales. To change the
temperature setting, follow these directions:
POWER
SWITCH
FUSE
POWER
CORD
HEATER
COOLING
PAGE 8
BREWBUILT.COM