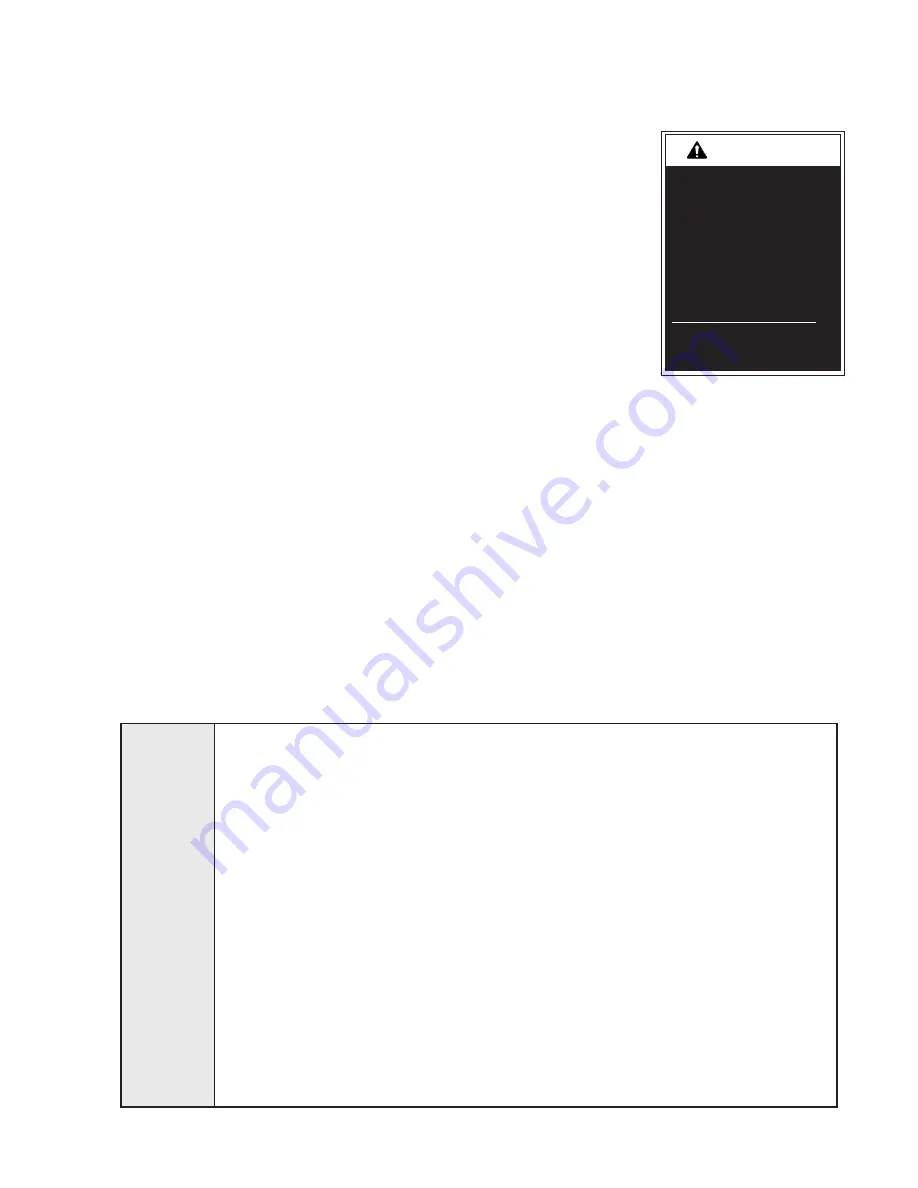
Page 9
Maintenance and Lubrication Schedule
Maintenance and
lubrication procedures
must be performed as
specified by an
authorized service
technician. Failure to
do so may result in
serious bodily injury
and/or property
damage.
WA
RNING
Proper maintenance is necessary to ensure safe,
trouble free operation. Inspecting the lift for any
wear, damage or other abnormal conditions should
be a part of the transit agency daily service program.
Simple inspections can detect potential problems.
The maintenance and lubrication procedures speci-
fied in the following schedule must be performed by
a BraunAbility authorized service representative at
the scheduled intervals according to the number of
cycles.
All service procedures must be performed
when the lift is fully on the ground.
NL503 Series
lifts are equipped with a cycle counter (digital display
built into the electronic control board).
NL503 Series lifts are equipped with hardened pins
and self-lubricating bushings to decrease wear,
provide smooth operation and extend the service life
of the lift.
When servicing the lift at the recommended intervals,
inspection and lubrication procedures specified in the
previous sections should be repeated. Clean com-
ponents and the surrounding area before applying
lubricants. Clean only with water, and when cleaned,
lubricate as directed in the lubrication diagram. Do
not use solvents to clean.
LPS2 General Purpose Penetrating Oil is recom-
mended where Light Oil is called out. Use of improp-
er lubricants can attract dirt or other contaminants
which could result in wear or damage to the compo-
nents. Platform components exposed to contami-
nants when lowered to
the ground may require
extra attention.
Lift components requiring
grease are lubricated dur-
ing assembly procedures.
When replacing these
components, be sure
to apply grease during
installation procedures.
Specified lubricants are
available from BraunAbili-
ty (part numbers provided
on previous page).
All listed inspection, lubrication and maintenance proce-
dures should be repeated at 750 cycle intervals follow-
ing the scheduled 4500 cycle maintenance procedures.
These intervals are a general guideline for scheduling
maintenance procedures and will vary according to lift
use and conditions. Lifts exposed to severe conditions
(weather, environment, contamination, heavy usage,
etc.) may require inspection and maintenance proce-
dures to be performed more often than specified.
Discontinue lift use immediately if maintenance and
lubrication procedures are not properly performed, or if
there is any sign of wear, damage or improper operation.
Contact your sales representative or call BraunAbility at
1-800-946-7513. One of our Aftersales representatives
will direct you to an authorized service technician who
will inspect your lift.
Apply Light Oil - See Lubrication Diagram
Apply Light Oil - See Lubrication Diagram
Apply Light Oil to both sides of slot.
See Lubrication diagram
Apply Synthetic Grease to both sides of slot.
See Lubrication diagram
Correct or replace damaged parts.
Correct or replace damaged parts and/or relubri-
cate. See Lubrication Diagram
See Certification Checklist Diagnostic Procedures
Correct as needed.
Correct as needed.
Extend outer platform and use compressed air to
remove any debris in the platform slide plate tracks.
750
Cycles
Outer barrier pivot bearings (2)
Outer barrier latch pivot (2)
Outer barrier latch split foot pivot
Outer barrier bracket slot (both sides) - (2)
Inspect outer barrier for proper operation
Inspect outer barrier latch for proper operation,
positive securement, and detached or missing
spring
Verify FMVSS 403 / 404 Certification Checklist
Inspect lift for wear, damage or any abnormal
condition
Inspect lift for rattles
Platform slide tracks (6)