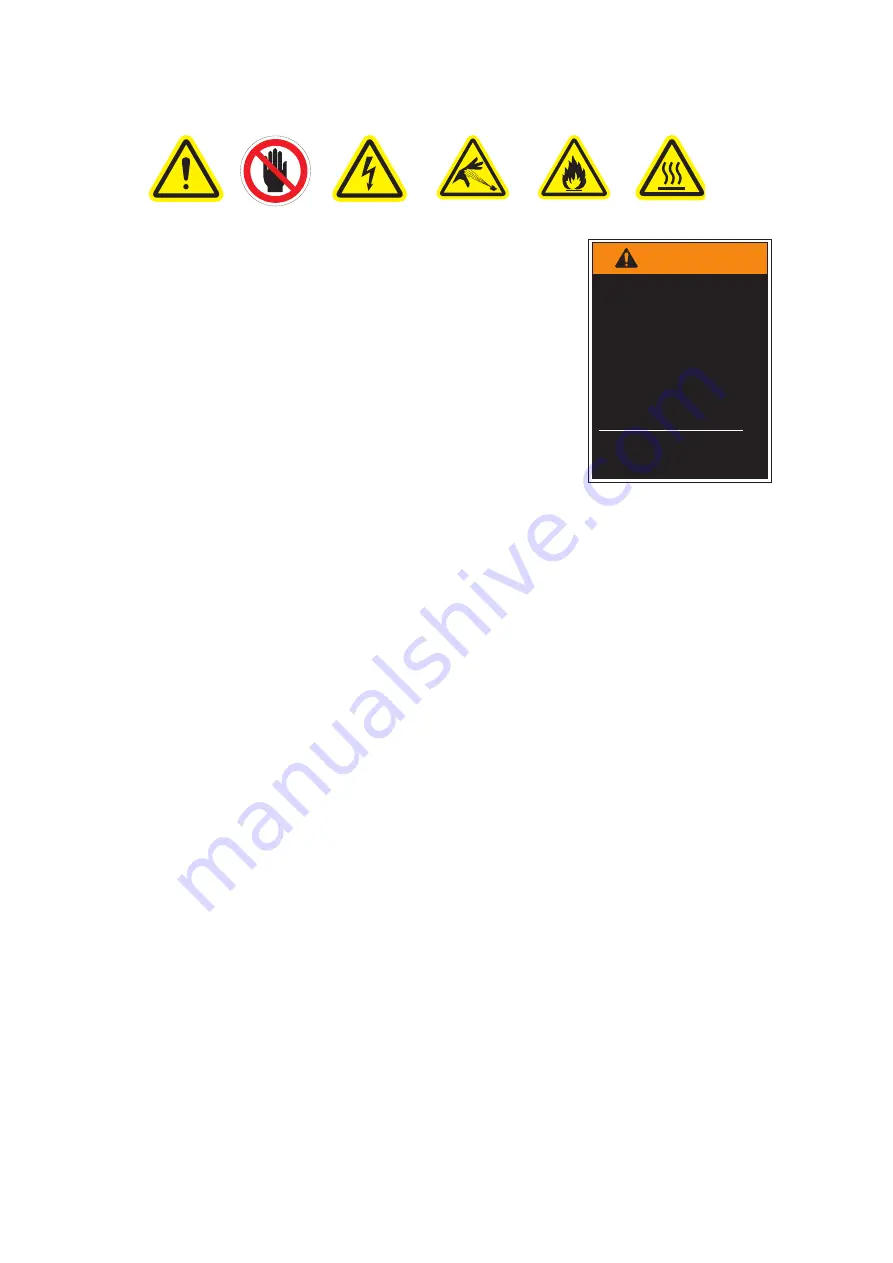
Page 32
Maintenance and Lubrication
WA
RNING
Maintenance and
lubrication procedures
must be performed as
specified by an
authorized service
technician. Failure to
do so may result in
serious bodily injury
and/or property
damage.
Proper maintenance is necessary to ensure safe,
trouble-free lift operation. Inspecting the lift for
any wear, damage or other abnormal conditions
should be a part of a regular service program.
Simple inspections can detect potential problems.
Park vehicle on a level surface clear of traffic and
bystanders. Place vehicle transmission in “Park”
and engage parking brake. Deploy lift to ground
level. Provide adequate work space around fully-
deployed lift. Perform specified maintenance and
lubrication procedures (position lift as required).
Pump Module: When cleaning the exterior of
the pump module, first disconnect the unit from
its power source. Do not use liquid cleaners,
aerosols, abrasive pads, scouring powders or
solvents, such as benzine or alcohol. Use a
soft cloth lightly moistened with a mild detergent
solution. Ensure the surface cleaned is fully dry
before reconnecting power.
Other Components: Clean components and
the surrounding area before applying lubricants.
Clean only with mild detergent and water. Do not
clean with solvents. Allow the lift to dry thoroughly
and apply lubricants as specified after every
cleaning.
LPS2 General Purpose Penetrating Oil is recom-
mended where Light Oil is called out. Use of
improper lubricants can attract dirt or other con-
taminants which could result in wear or damage
to components. Platform components exposed
to contaminants
when lowered to the
ground may require
extra attention.
Perform mainte-
nance and lubrica-
tion procedures
at the scheduled
intervals according
to the number of
cycles. When ser-
vicing the lift at the
recommended inter-
vals, inspection and
lubrication procedures specified in the previous
sections should be repeated.
These intervals are a general guideline for sched-
uling maintenance procedures and will vary ac-
cording to lift use and conditions. Lifts exposed to
severe conditions (weather, environment, contami-
nation, heavy usage, etc.) may require inspection
and maintenance procedures to be performed
more often than specified.
Records of maintenance and service procedures
should be maintained.
Discontinue lift use if maintenance and lubrication
procedures are not properly performed, or if there
is any sign of wear, damage or improper opera-
tion. Contact your sales representative.
36514
36512
36513
Summary of Contents for L952SE2740IB-2
Page 44: ...Page 42...