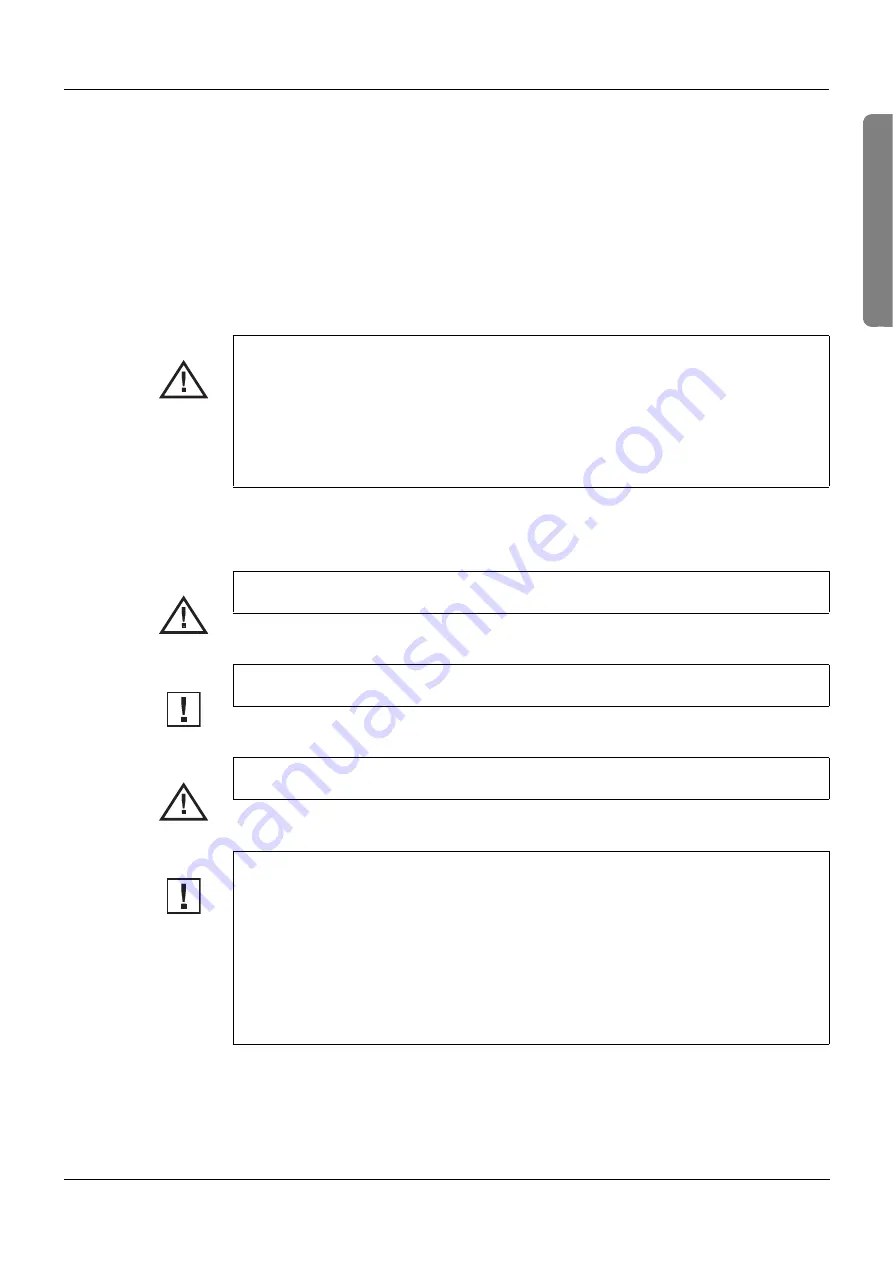
Disinfection / Cleaning
Part 1 • Page 12-1
Part 1 – Operating Instructions
Rev. 6.4 dated 2022-02
Software Released Version: 1
(Eco)RO Dia II
Part 1 • Ch
apter 12
12. Disinfection / Cleaning
Disinfection of the (Eco)RO Dia II is carried out
•
After initial commissioning and flushing out the preservative
•
As a preventative measure
•
When the microbiological action, warning or alarm limits are attained or exceeded
•
After opening the system for maintenance or repair work or other constructional intervention
12.1 General points
The system must be disconnected completely from the mains supply line before disinfecting or cleaning
the softener. It is absolutely essential to disconnect the RO during disinfection or cleaning.
CAUTION
The system may only be disinfected or cleaned during the dialysis-free period.
Acute risk of poisoning!
•
The permeate must be disconnected from the dialysis machines before the disinfection
process is started.
•
It must not be possible to carry out dialysis!
If a softener is used: softeners may only be used with a pipe disconnector of the type EA1 or
with a free intake.
CAUTION
The RO must be disinfected if the germ count is found to be higher than normal (action limit:
30 CFU/ml).
IMPORTANT After the RO has been at a standstill for > 72 hours, carrying out disinfection is
recommended.
CAUTION
A B. Braun reverse osmosis system may only be disinfected or cleaned by B. Braun-
authorized and trained personnel.
IMPORTANT Before disinfection or cleaning:
•
The Hydrowatch on the membrane surge tank (DG) must be checked before each
disinfection or cleaning process. If the red indicator is visible, the ring piping must
not be disinfected.
•
To increase the effectiveness of the disinfection process, it must be ensured that the
membrane modules are free of organic and chemical contamination. The membrane
modules must be cleaned beforehand with a commercial membrane cleaner to
remove hardness salts or iron deposits on the membrane.
•
Chemical disinfectants must comply with EN 1040:2005 (Chemical disinfectants and
antiseptics: test procedure for bactericide basic action).