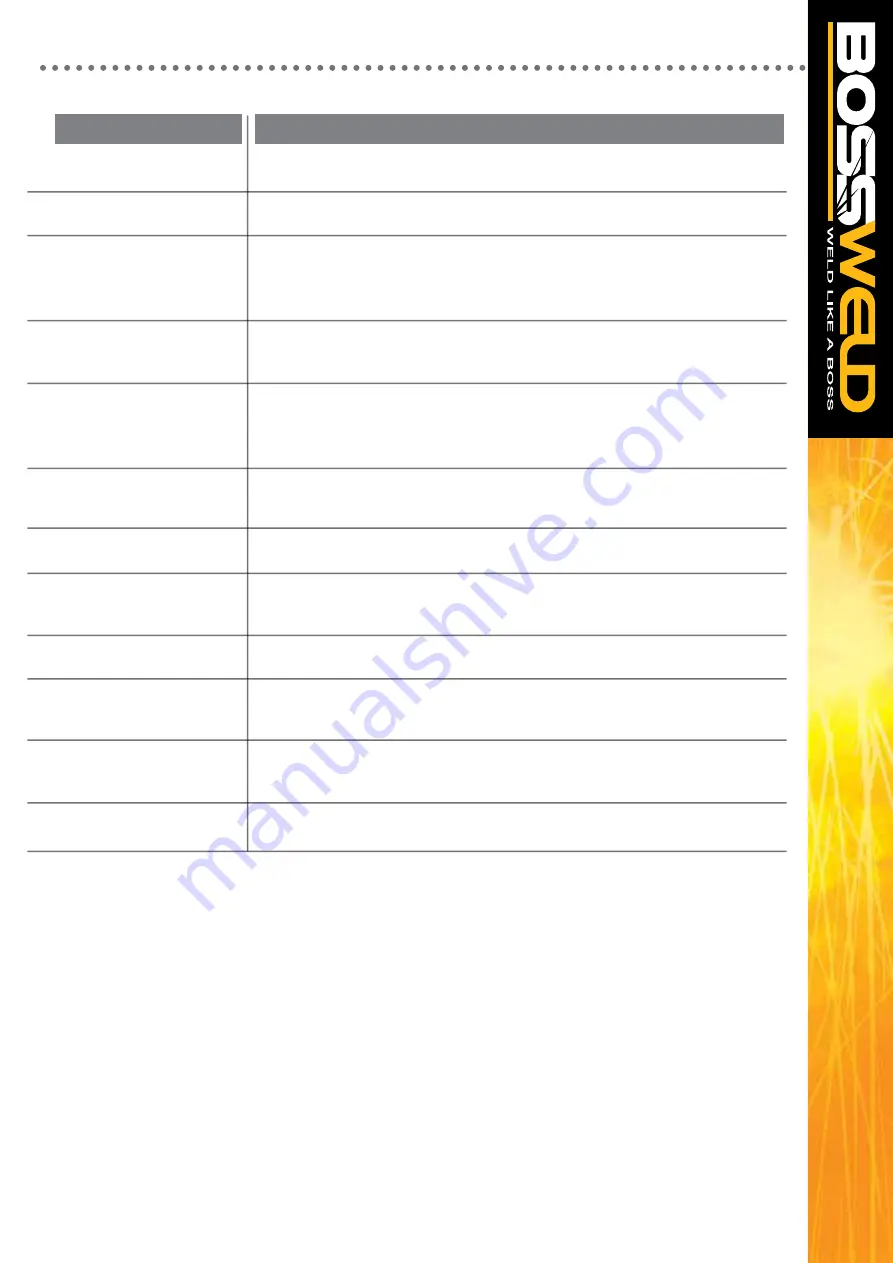
Issue
Adjusting wrong dial
Incorrect wire speed setting
Voltage setting incorrect
MIG torch lead kinked or
too sharp angle being held
Contact tip worn, wrong
size, wrong type
Liner worn or clogged (the
most common causes of
bad feeding)
Wire misaligned in drive
roller groove
Incorrect drive roller size
Wrong type of drive roller
selected
Worn drive rollers
Too much tension on wire
spool hub
Wire crossed over on the
spool or tangled
Contaminated MIG wire
Possible Reason
• Be sure to adjust the wire feed and voltage dials for MIG welding.
• Adjust the wire feed speed
• Adjust the voltage setting
• Remove the kink, reduce the angle or bend
• Replace the tip with correct size and type
• Try to clear the liner by blowing out with compressed air.
• Locate the wire into the groove of the drive roller
• Fit the correct size drive roller E.g. 0.8mm wire requires 0.8mm drive roller
• Fit the correct type roller (e.g. knurled rollers needed for flux cored wires)
• Replace the drive rollers
• Reduce the spool hub brake tension
• Remove the spool untangle the wire or replace the wire
• Use clean dry rust free wire. Do not lubricate the wire with oil, grease etc
MIG WIRE FEED TROUBLE SHOOTING
The following chart addresses some of the common WIRE FEED problems during MIG welding.
23
OPERATIONAL ENVIRONMENT
• Height above sea level ≤1000m
• Operation temperature range -10~+40°C
• Air relative humidity is below 90%( 20°C)
• Preferably site the machine above floor level, ensure the maximum angle does not exceed 15 degrees.
• Protect the machine against heavy rain and against direct sunshine.
• The content of dust, acid, corrosive gas in the surrounding air or substance must not exceed normal
standards.
• Take care that there is sufficient ventilation during welding. There must be at least 30cm free distance
between the machine and wall.
For other tips and troubleshooting refer to our website www.dynaweld.com.au/troubleshooting