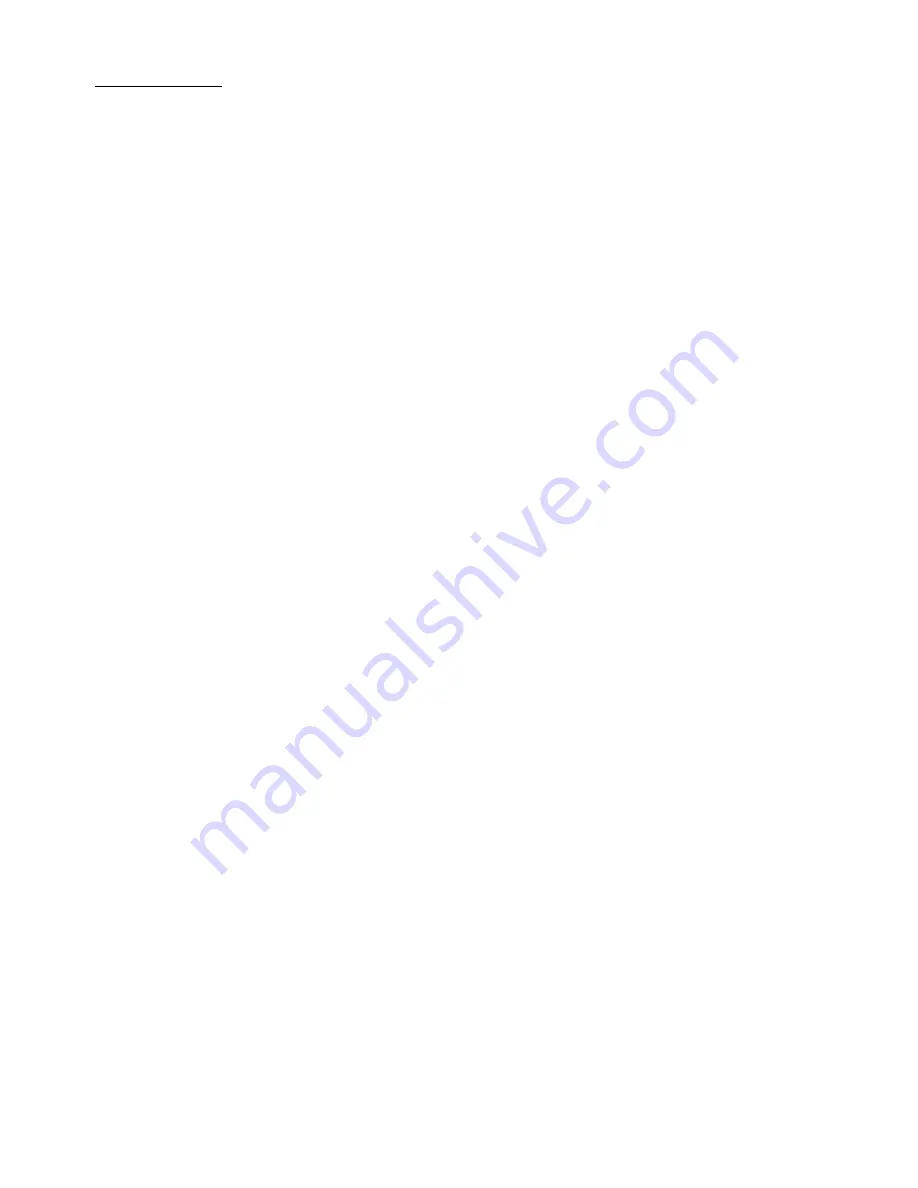
Troubleshooting
•
Problem:
The motor is running but the drive structure does not move.
o
Possible Causes:
The connection between the motor and the drive structure is loose.
o
Approach:
Check the connection between the motor and the drive structure after the
system is powered down.
•
Problem:
The cutting head runs in the opposite direction to normal logic.
o
Possible Causes:
The direction of the control signal DIR signal is reversed or a signal
is not connected firmly. Between the motor and the drive AB.
o
Approach:
After the system is powered down, adjust the connection between the
motor and the drive.
•
Problem:
The system can not control the cutting head to follow the specified height after
entering the normal working condition.
o
Possible Causes:
The system does not detect a follow-up signal.
o
Approach:
Check whether the laser switch signal output of the laser system is normal.
Is this signal properly connected to the FTC port?
•
Problem:
After the system has entered the normal working condition, close the follower
signal (TR), cut the head up, or shake up and down.
o
Possible Causes:
(1) The capacitor signal line connection loose. (2) The motor driver
line is loose. (3) The signal strength has abnormal changes. (4) The workpiece is in
poor contact with the amplifier housing.
o
Approach:
Check if the connection between the capacitor signal cable and the cutting
head is loose. Check whether the connection between the capacitor signal cable and
the preamplifier is loose. Check whether the motor driver cable is loose and the
resistance of the workpiece and the amplifier shell should be less than 2 ohms. If the
signal strength changes abnormally, please re-calibrate.
•
Problem:
The system follows the height deviation from the set value too far.
o
Possible Causes:
The screw pitch / per revolution is not the same as the actual value.
o
Approach:
Set the screw pitch / per revolution to the actual value setting.
•
Problem:
Cutting head in the follow-up height up and down the shock.
o
Possible Causes:
(1) FTC and metal processing parts bad grounding. (2) Nozzle and
metal parts short circuit. (3) The nozzle and the FTC coaxial cable connection
loosening. (4) Follow the tolerance set too small.
o
Approach:
(1) Check whether the FTC grounding point with the metal processing
parts connected well. (2) Check the capacitance sensor (nozzle) is short with metal
parts (3) Check the capacitance sensor (nozzle) and the FTC coaxial cable is connected
between the fastening. (4) Will be set to follow the tolerance.
•
Problem:
The cutting head has overshot before being followed.
o
Possible Causes:
(1) The motor rigidity is insufficient. (2) The motor speed is too fast.
o
Approach:
(1) Adjust the motor drive rigidity or current. (2) Reduce the speed stalls
FTC61 SERIES MANUAL
Document Number: 855-910
Revision: 001 Revision Date: 6/1/2019
BOSSLASER - PAGE 11 of 12