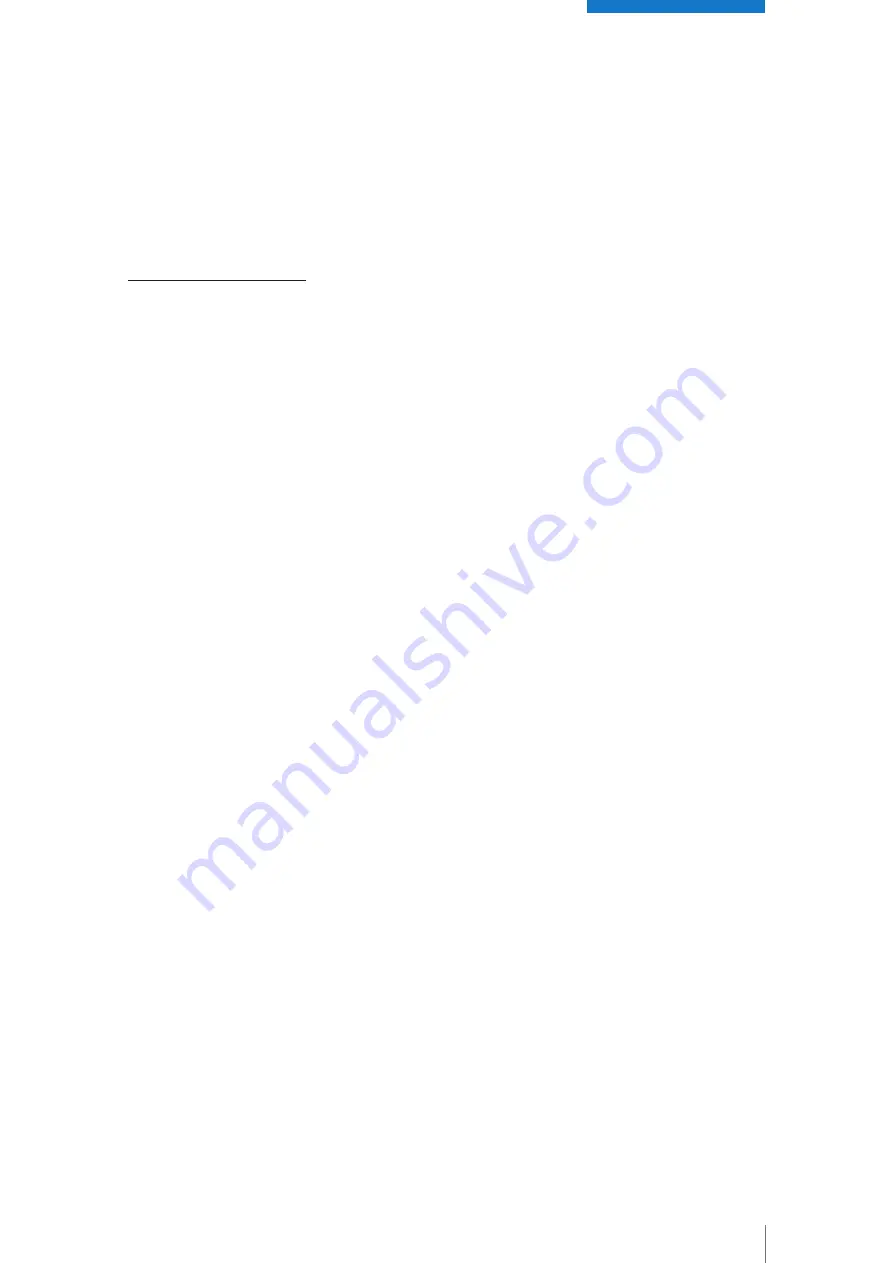
3
ELECTRIC SCREWDRIVERS FOR SELF-CUTTING THREADED INSERTS
1. BOSSARD DISCLAIMER
For the attention of the end-user
Bossard INSTALLATION EQUIPMENT
Please nominate a contact who can be kept updated of any changes to the equipment and return this
sheet to Bossard. Where applicable, it is also supplied with quotations.
COMPANY
_______________________________________________________________________________
(print please)
NOMINATED CONTACT
____________________________________
DEPARTMENT
_______________________________
TELEPHONE NUMBER & EXTENSION
___________________________________________________________________
DISCLAIMER
This equipment supplied for
_______________________________________________________
(customer & country)
On Shipment Number
___________________________________________________________________________________
Dated
____________________________________
…should not be put into production use until the attached manual is understood. In some instances,
operating instructions, are included, and these are detailed on the packing list attached, the contents of
which should be confirmed as present by the customer. No warranty claims will be considered if the fault
is due to misuse or lack of precautions previously brought to your attention. Repairs will then be charged
at cost, including carriage.
The standard equipment is designed for reasonable use at an economic price. Where this is of an exces-
sive nature, either through continual use or the arduous nature of the operation, the warranty period
reduces accordingly. Bossard and their suppliers, if applicable, will adopt a reasonable attitude to this
reduction after consultation with the customer on the basis of commercial common sense. Modifications
to the equipment, where applicable, will be charged at cost.
It is the customer’s responsibility to order sufficient recommended spares to service the equipment as
detailed in the literature, and consideration should be given to duplicating complete units if the operation
is critical through either time of completion or production volume.
Ideally, one individual should be made responsible for maintaining the equipment. In the case of malfun-
ction of a specific piece of equipment, confirmed after discussion with Bossard, within a twelve-month
period from receipt of goods or proportionally less if the working day is greater than eight hours, Bossard
reserves the right to request the equipment be sent direct to the manufacturer of the original equipment.
Serial numbers and part numbers where applicable should always be stated on the paperwork.
Summary of Contents for 035/E32V
Page 1: ...OPERATORS MANUAL FOR ELECTRIC SCREWDRIVERS for self cutting Threaded Inserts ...
Page 23: ...23 4 6 10 INPUT OUTPUT CONNECTOR ...
Page 24: ...24 4 6 11 DIP SWITCH SETTINGS ...
Page 25: ...25 ...
Page 27: ...www bossard com 27 ...