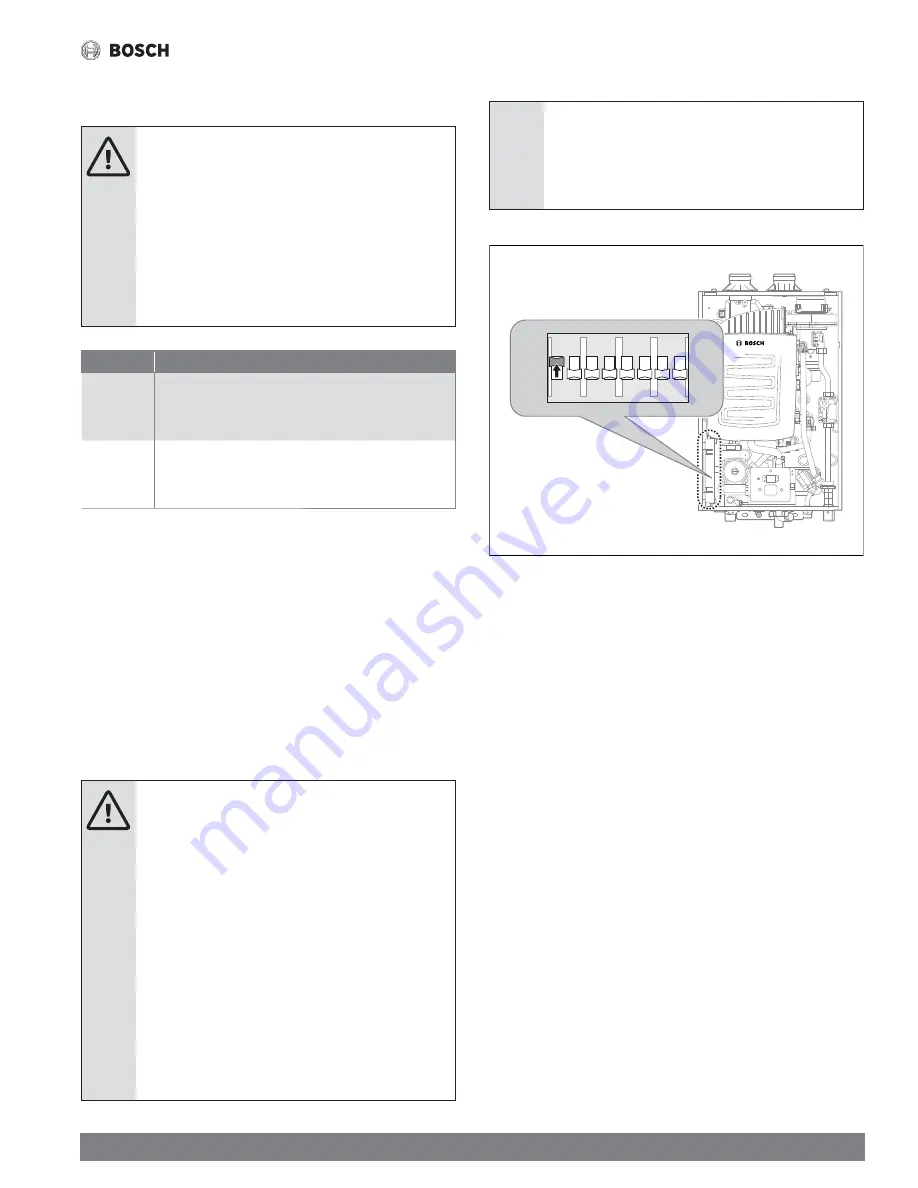
|
33
Installation Instructions
Singular Combi Boiler - BTC 439003301 B (2021/07)
6.2 Vent Pipe Materials
WARNING:
Venting requirements differ in the US and Canada. Consult
the following chart or the most recent edition of ANSI
Z223.1/ NFPA 54 or CAN/CGA B149.1, as well as all
applicable local codes and regulations when selecting vent
pipe materials. Do not use cellular core PVC (ASTM F891),
cellular core CPVC, Radel® (polyphenolsulfone) for the
exhaust vent.
Covering non-metallic vent pipe and fittings with thermal
insulation shall be prohibited.
Location
Recommended Vent Materials
USA
PVC Schedule 40 (solid core)
CPVC Schedule 40 or 80 (solid core)
Approved Polypropylene
Canada*
Type BH Special Gas Vent Class IIA (PVC)
Type BH Special Gas Vent Class IIB (CPVC)
Type BH Special Gas Vent Class IIC (Polypropylene)
Table 12
* For installation in Canada,
fi
eld-supplied plastic vent piping must comply with
CAN/CGA B149.1 (latest edition) and be certi
fi
ed to the Standard For Type BH
Gas Venting Systems, ULC-S636. Components of this listed system must not be
interchanged with other vent systems or unlisted pipes or
fi
ttings. All plastic
components and speci
fi
ed primers and glues of the certi
fi
ed vent system must
be from a single system manufacturer and must not be intermixed with another
system manufacturer’s parts. The supplied vent connector and vent termination are
certi
fi
ed as part of the boiler.
Generally, the boiler limits the flue gas to remain below 150°F (65°C) to
use the flue pipe.
When the return water temperature to the boiler is higher than 140°F
(60°C), DIP switch #1 must be set to ON to release the flue gas limit. CPVC
or PP must be used in such case.
WARNING:
This boiler has a built-in control to limit the exhaust
temperature to 149°F (65°C). As a result, the boiler can be
vented with Schedule 40 PVC.
In high temperature applications, the exhaust temperature
can exceed 149°F (65°C). In that case, to prevent nuisance
tripping of the control you must install Schedule 40
or 80 CPVC or Approved Polypropylene in the USA or
Type BH Special Gas Vent Class IIB (CPVC) or Class IC
(Polypropylene) that conforms to ULC-S636 in Canada.
Then the dip switch setting can be changed to "ON".
In systems with 2 in. vents, if the exhaust temperature
exceeds 149°F (65°C), CPVC pipe (field supplied) must
be used for the first 3 feet of equivalent pipe length. For
systems with 3 in. vents, if the exhaust temperature exceeds
149°F (65°C), CPVC pipe (field supplied) must be used for
the first 5 in. of equivalent pipe length.
NOTICE:
PCB DIP switch #1 is set to OFF as factory default
When you set PCB DIP switch #1 to ON, ensure that CPVC
piping shall be used for exhaust venting.
Figure 32
1 2 3 4 5 6 7 8
ON