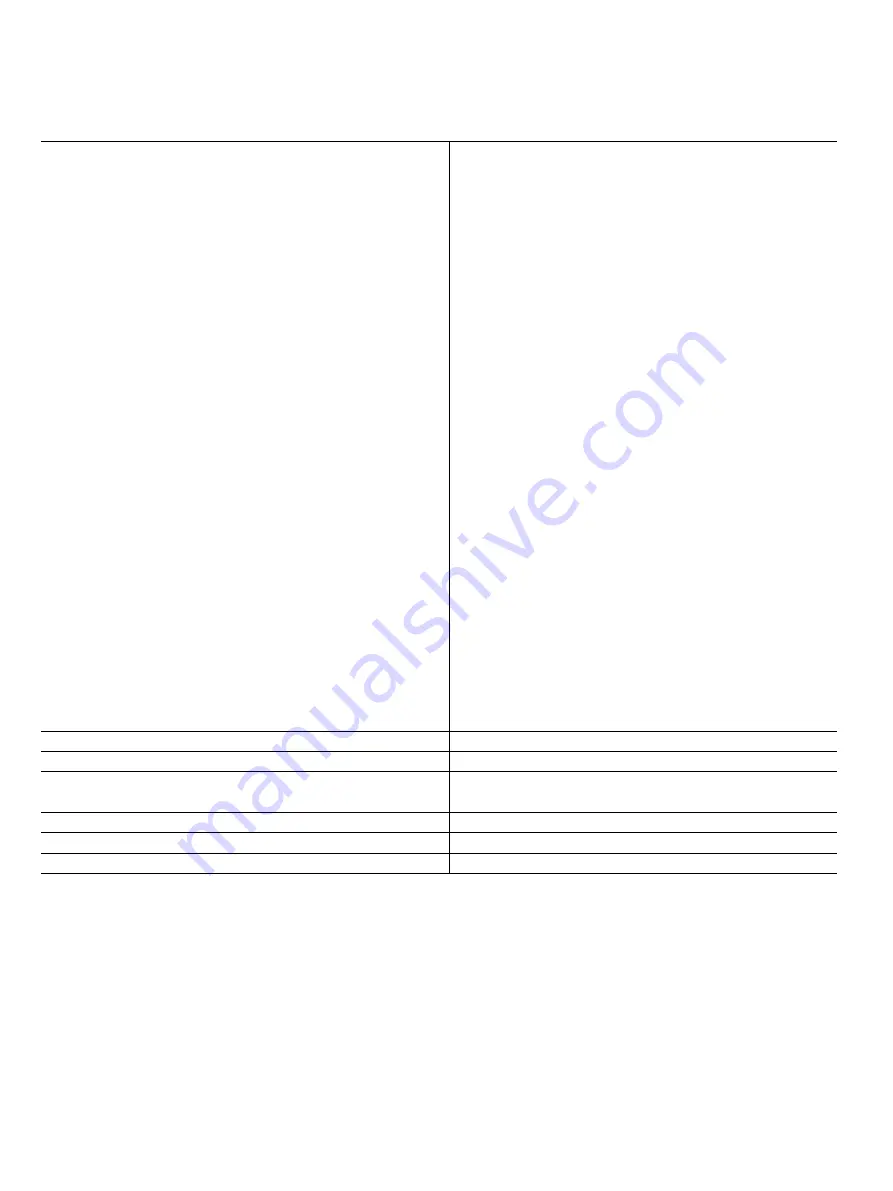
10/14
VT-HNC100.../S
| Digital drive controller
Bosch Rexroth AG
, RE 30159, edition: 2012-03
Digital position transducers (encoder)
per axis electronics:
– Position transducer, incremental
(transducer with TTL output)
• Input voltage
log 0 0 to 1 V
log 1 2.8 to 5.5 V
• Input current
log 0 –0.8 mA (with 0 V)
log 1 0.8 mA (with 5 V)
• Max. frequency referring to Ua1
f
max
250 kHz
• Voltage supply via the VT-HNC100...3X/S
U, I
5.25 V ±1 %,
max. 400 mA
at X8M1, pin 12 (+5 Venc)
– SSI transducer
(Due to the higher control quality, an SSI transducer
with clock synchronization should be used.)
• Coding
Gray-Code / binary code
• Data width
Adjustable 12 to 28 bits
• Line receiver / line driver
RS485
• Voltage supply via the
VT-HNC100...3X/S
U, I U
B
,
max. 500 mA
at X8M1, pin 14 (+24 Venc)
– Position transducer, EnDat 2.2
• Interface (clock and data) according to RS 485
• Voltage supply via the VT-HNC100...3X/S
U, I
5.25 V ±1 %,
max. 400 mA
at X8M1, pin 12 (+5 Venc)
3.6 to 5.25 V must be applied to the transducer.
• Resolution
Minimum 10 nm or higher
Analog position transducer (encoder):
•
Input
voltage
U
E
Max. +12 V to –12 V (+10 V to –10 V measurable)
•
Input
resistance
R
E
> 10 MΩ
•
Resolution
5
mV
• Non-linearity
< 0.2 %
•
Calibration
tolerance
1)
Max. 40 mV (with factory settings)
• Voltage supply via the VT-HNC100...3X/S
U, I
+10 V ± 25 mV, max. 20 mA at X8M1, pin 13 (+10 Vref)
Reference potential for all signals
EGND
Dimensions
See page 13
Assembly
Top hat rail TH 35-7.5 or TH 35-15 according to EN 60715
Admissible operating temperature range
0 to 50 °C
Storage temperature range
–20 to +70 °C
Protection class according to EN 60529:1991
IP 20
Weight
m
585 g
CE conformity
See page 2
Further technical details upon request.
Technical data VT-HNC100-...-3X
(1-axis version), continued
Notice:
For information on the environment simulation testing
for the areas EMC (electro-magnetic compatibility), climate and
mechanical load, see data sheet 30139-U.
1)
If the factory settings are insufficient, the measurement
technology can be calibrated on site via software in a system-
specific way.