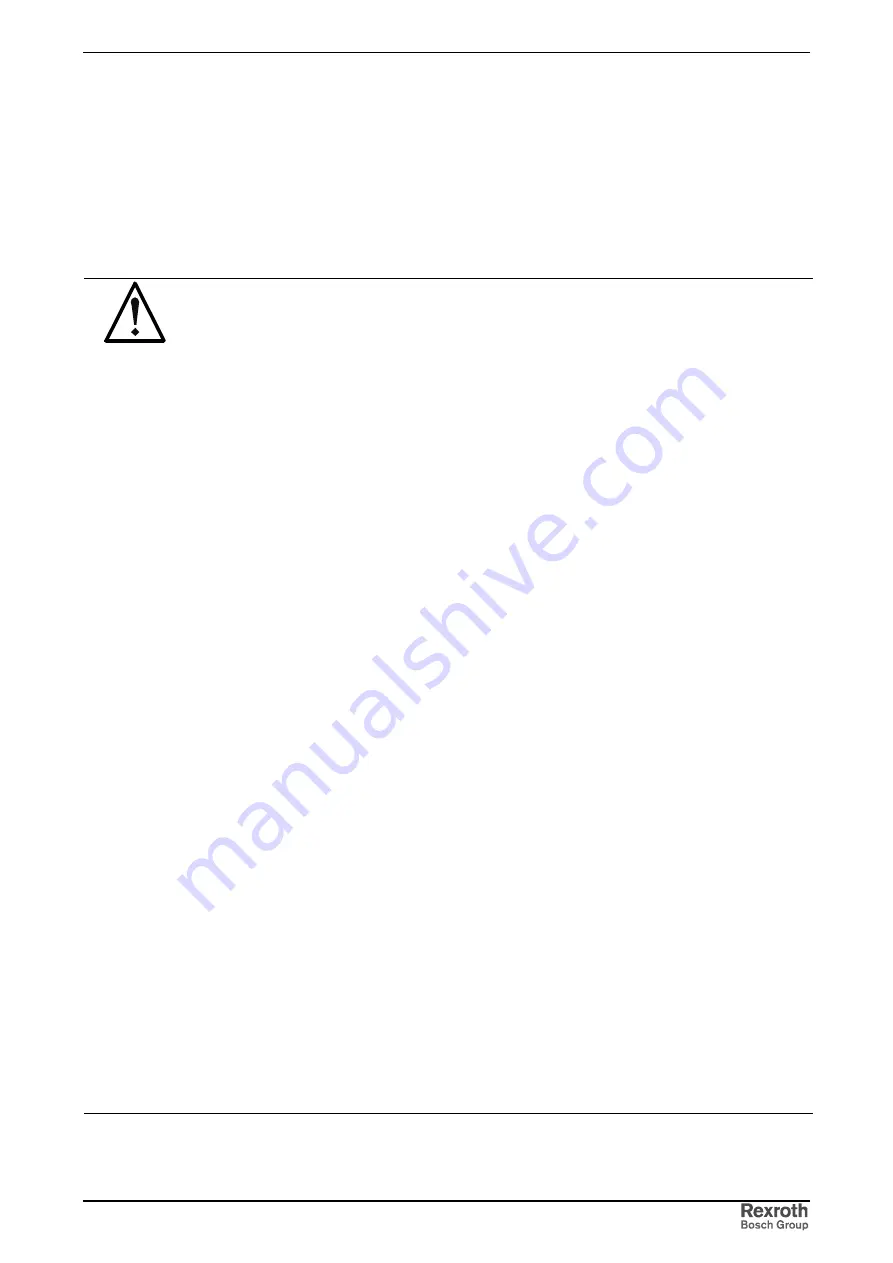
Rexroth Diax 04 HDD and HDS
Important Notes
1-3
DOK-DIAX04-HDD+HDS*UL*-IB01-EN-P
Dangerous movements can occur immediately after equipment is
switched on or even after an unspecified time of trouble-free operation.
The monitoring in the drive components will normally be sufficient to avoid
faulty operation in the connected drives. Regarding personal safety,
especially the danger of bodily harm and material damage, this alone
cannot be relied upon to ensure complete safety. Until the integrated
monitoring functions become effective, it must be assumed in any case
that faulty drive movements will occur. The extent of faulty drive
movements depends upon the type of control and the state of operation.
DANGER
Dangerous movements! Danger to life, risk of injury, severe bodily harm or material
damage!
•
For the above reasons, ensure personal safety by means of qualified and tested higher-
level monitoring devices or measures integrated in the installation.
They have to be provided for by the user according to the specific conditions within the
installation and a hazard and fault analysis. The safety regulations applicable for the
installation have to be taken into consideration. Unintended machine motion or other
malfunction is possible if safety devices are disabled, bypassed or not activated.
To avoid accidents, bodily harm and/or material damage:
•
Keep free and clear of the machine’s range of motion and moving parts. Possible
measures to prevent people from accidentally entering the machine’s range of motion:
–
use safety fences
–
use safety guards
–
use protective coverings
–
install light curtains or light barriers
•
Fences and coverings must be strong enough to resist maximum possible momentum.
•
Mount the emergency stop switch in the immediate reach of the operator. Verify that the
emergency stop works before startup. Don’t operate the device if the emergency stop is
not working.
•
Isolate the drive power connection by means of an emergency stop circuit or use a safety
related starting lockout to prevent unintentional start.
•
Make sure that the drives are brought to a safe standstill before accessing or entering the
danger zone.
•
Additionally secure vertical axes against falling or dropping after switching off the motor
power by, for example:
–
mechanically securing the vertical axes,
–
adding an external braking/ arrester/ clamping mechanism or
–
ensuring sufficient equilibration of the vertical axes.
•
The standard equipment motor brake or an external brake controlled directly by the drive
controller are
not sufficient to guarantee personal safety!
•
Disconnect electrical power to the equipment using a master switch and secure the switch
against reconnection for:
–
maintenance and repair work
–
cleaning of equipment
–
long periods of discontinued equipment use
•
Prevent the operation of high-frequency, remote control and radio equipment near
electronics circuits and supply leads. If the use of such devices cannot be avoided, verify
the system and the installation for possible malfunctions in all possible positions of normal
use before initial startup. If necessary, perform a special electromagnetic compatibility
(EMC) test on the installation.