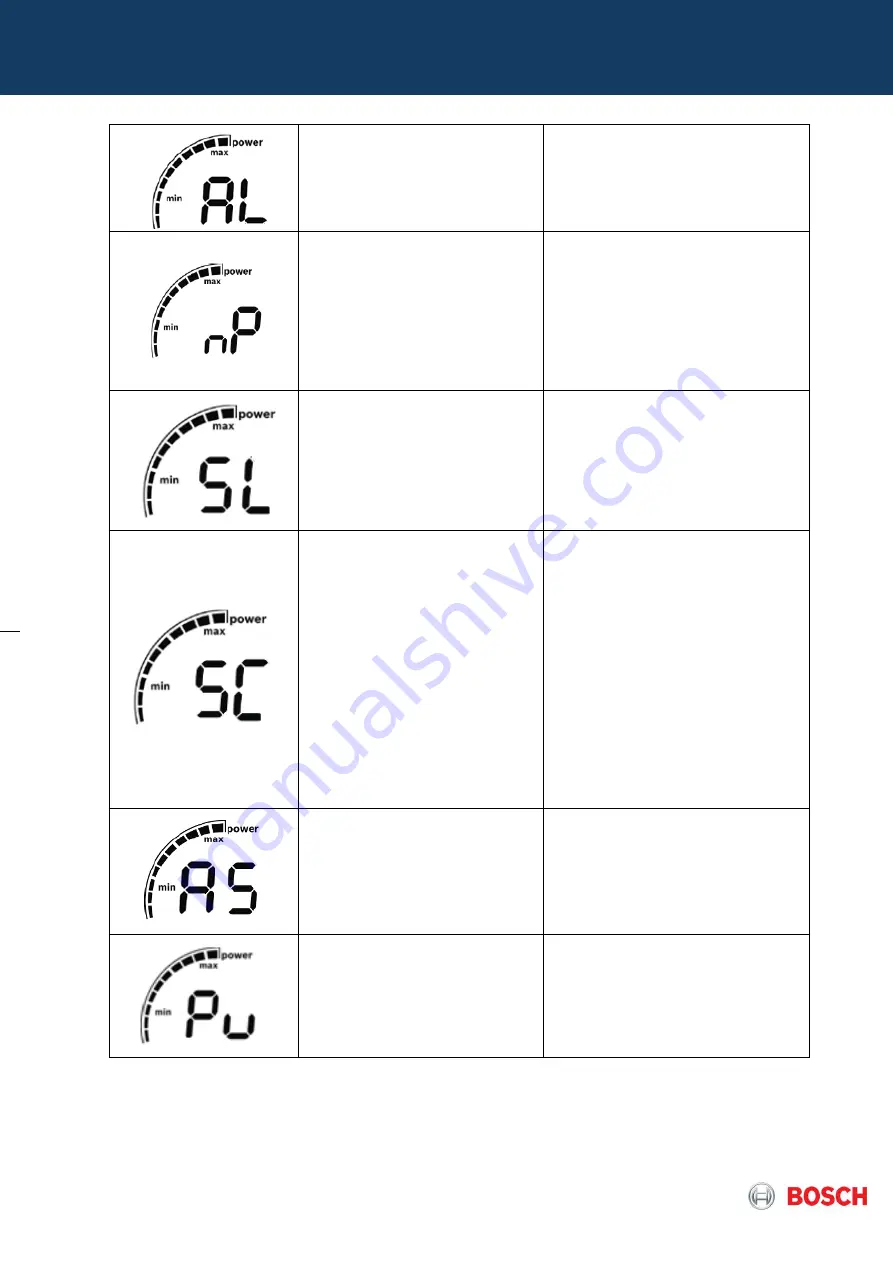
Page 46 from 76 6 720 814 719
SM FP_Australia 2017/04 EN
Test Display
Visualization of all segments of text
display (LCD)
Reset to Factory default values
Allows the individual reset of P1 and
P2 for the default values memorized
from factory during appliance
adjustment.
Enter this mode and select P1 or P2
according need and press P for reset
(+/- 3 sec)
Set Point Limit
Allows the Installer to select the
maximum temperature setting
possible in the appliance to be
selected by user:
55ºC
60ºC
70ºC
SC = Set Point Calibration
Internal Compensation of set point
defined by user in order to
compensate temperature loss until
last consumption point.
Value can be adjusted (ºC by ºC):
4000S
set point - 5ºC
to
set point + 5ºC
Optiflow
set point – 2.5ºC
to
set point + 2.5ºC
AS = Altitude Adjustment
(combustion optimization)
(default value depends of TTNR
and destination Country –
Australia is set to 1)
1= sea level to 500 m
2= 500 m to 1000 m
3= 1000 m to 1500 m
4= 1500 m to 2000 m
5= 2000 m to 2500 m
6> 2500 m
Purge time definition
Allows the change of time for pos-
purge time between:
-
3 min (at min fan speed)
or
-
30 sec (at normal fan
speed)