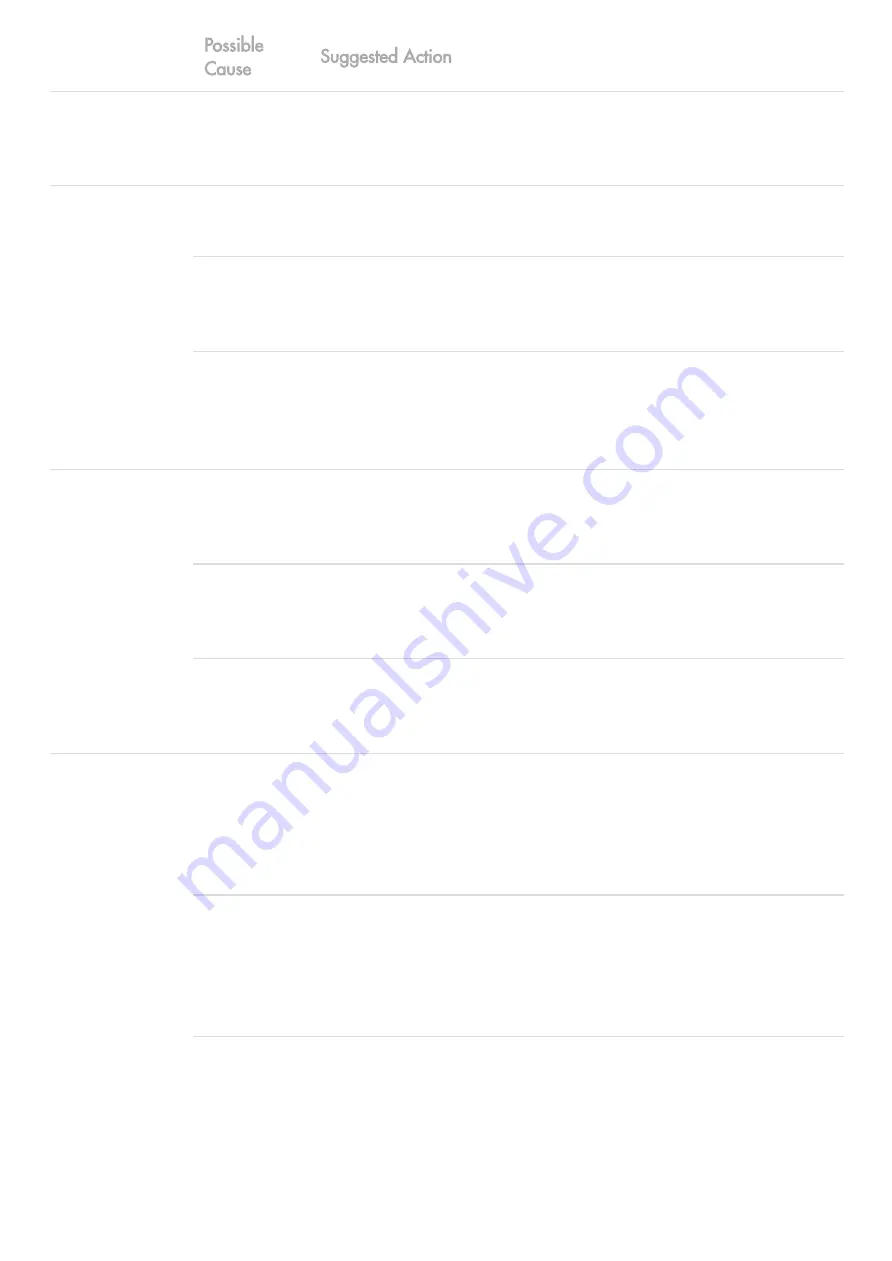
Problem/Report
Possible
Cause
Suggested Action
No Water
Dispensing
Water
Pressure
Regulator
Check water flow through the regulator.
Replace if necessary.
No Sparkling
Water
No CO2
pressure
Check CO2 bottle, regulator and non-return valve. Supply pressure
should be 58 psi (4bar), replace as necessary.
Carbonator
Tank Not
Filling
Check carbonator probe for possible short circuit to ground.
Check for pump timeout, cycle power off & on then purge
carbonator.
Water
isolated
from
machine
Check water inlet supply.
Poor Quality
Carbonation
Incorrect
CO2
Pressure
Check CO2 bottle, regulator and non-return valve. Supply pressure
should be 58 psi (4bar), replace as necessary.
Air in
Carbonator
Tank
Visit to view steps for purging tank.
Residue in
Carbonator
Tank
After prolonged use, a surface film can develop within the
carbonator tank. Refer to cleaning and sanitising instructions.
Warm Drinks
Insufficient
cooling air
flow through
the
fridge.
Check that the condenser is not blocked.
Check supply to cooling fans (230V AC).
If supply present replace fans.
If supply not present move on to the compressor. The supply to the
fans and the compressor are linked.
Compressor
not running
Check supply to compressor (230V AC).
Check NTC probe is not faulty
Check for system over heat. Allow the unit to cool and check for
airflow obstructions. Once the unit has cooled the fridge system will
restart. If the problem persists contact technical support.
Fridge
failure (See
fault codes)
If compressor & fan are running and there is no cooling contact
technical support.
Summary of Contents for T1
Page 4: ...Specification ...
Page 6: ...CLIMATIC CLASS N ...
Page 9: ......
Page 10: ......
Page 14: ......
Page 15: ......
Page 16: ...Installation Requirements Installation ...
Page 29: ...Fault Diagnostics Advanced Troubleshooting ...
Page 32: ...T1 Chilled Ambient Sparkling Circuit Schematic ...
Page 33: ...Water Pathway Chilled Ambient ...
Page 34: ...Water Pathway Chilled Sparkling ...
Page 35: ...Water Pathway Chilled Ambient Sparkling ...
Page 36: ......
Page 37: ...ProCore Exploded Parts Diagram T1 Exploded Parts Diagram Spares ...
Page 38: ......
Page 41: ......
Page 42: ......