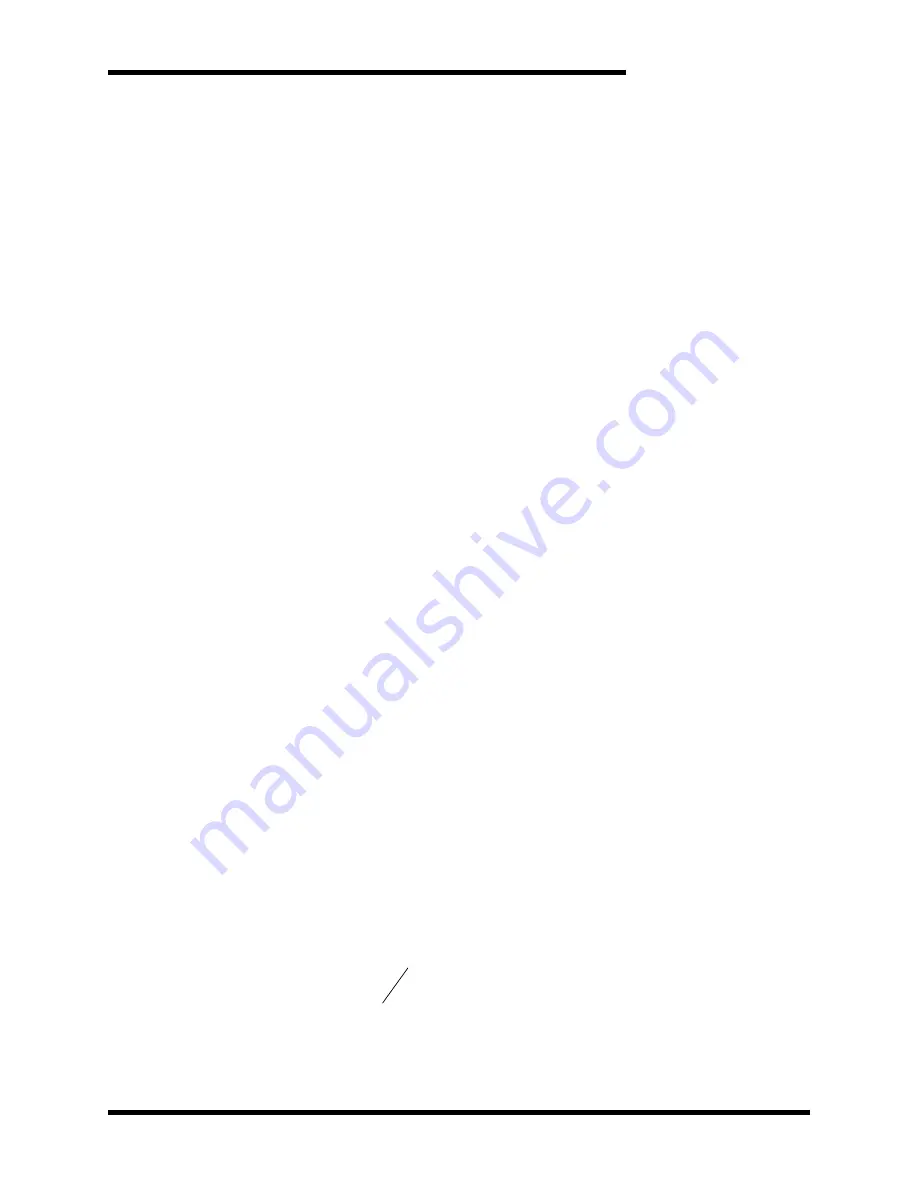
User’s Manual
35
7.
A
PPENDIX
7.1.
A
PPLICATION
N
OTES
7.1.1.
S
IZING
Y
OUR
B
RAKING
R
EQUIREMENTS
Braking transistor modules are sized by peak current requirements and
system voltage. Please use the following guidelines:
Verify the amount of peak power needed for braking. This must be
determined from the mechanical system layout, and should be calculated
in either peak watts or horsepower.
VFD’s are rated for braking power as well as peak braking capacity. This
information is available in the drive manual. This will be the maximum
amount of power that the output inverter stage of the VFD can absorb
from the load before having an overcurrent condition. Refer to your VFD
documents for information on drive sizing. Keep in mind that the current
rating of the drive is for three phase current, not DC bus current. The
braking current in the DC bus will be higher than the AC current absorbed
from the load.
Because Bonitron braking transistor modules are rated for peak current,
determine the
peak
braking power required.
7.1.1.1.
H
ORSEPOWER TO
W
ATTS
Once the braking requirements for the mechanical load are determined,
multiply the horsepower by the scaling factor of 746 W/hp to determine
the wattage required. For instance, with a 400hp system, the peak
braking power may be 600hp. In this case the peak power required would
be:
746
*
.
Braking
brake
hp
P
watts
hp
P
brake
447600
746
*
600
7.1.1.2.
P
EAK
A
MPERAGE
The peak amperage of the braking cycle can be determined by dividing
the peak braking wattage by the system bus trip point of the braking
transistor module used. If the above example were on a 480VAC system,
the trip point is 750VDC, as determined from Table 2-1. In this case the
peak current required would be:
VDC
P
I
Braking
brake
750
/
.
596.8ADC
750
/
447600
VDC
watts
I
brake
In this case, a 600 amp module should be used.
7.1.1.3.
O
HMIC
V
ALUE
The ohmic value of the resistive load can usually be determined from the
module ratings (see Table 6-1). This ohmic value indicates the capacity
of the braking transistor module, and may not be directly related to the
horsepower of the drive. In order to calculate the required ohmic value
for the braking load, use the following formula:
brake
brake
P
V
R
2
DCbus
)
(
The DC bus voltage for the equation is determined by the level that the
drive begins braking. For 460/480VAC systems, this is typically 750VDC,
Summary of Contents for M3575T
Page 6: ...M3575T 6 This page is intentionally left blank ...
Page 17: ...User s Manual 17 3 6 TYPICAL CONFIGURATIONS Figure 3 2 Typical Power Interconnection Diagram ...
Page 31: ...User s Manual 31 Figure 6 3 B5 Chassis Dimensional Outline Drawing ...
Page 34: ...M3575T 34 6 8 BLOCK DIAGRAM Figure 6 7 Block Diagram ...
Page 38: ...M3575T 38 Figure 7 1 Typical Status Contact Wiring with Input Contactor ...
Page 39: ...User s Manual 39 Figure 7 2 Typical Status Contact Wiring with Drive Interlock Control ...
Page 41: ...User s Manual 41 NOTES ...
Page 42: ...M3575T 42 This page is intentionally left blank ...
Page 43: ......