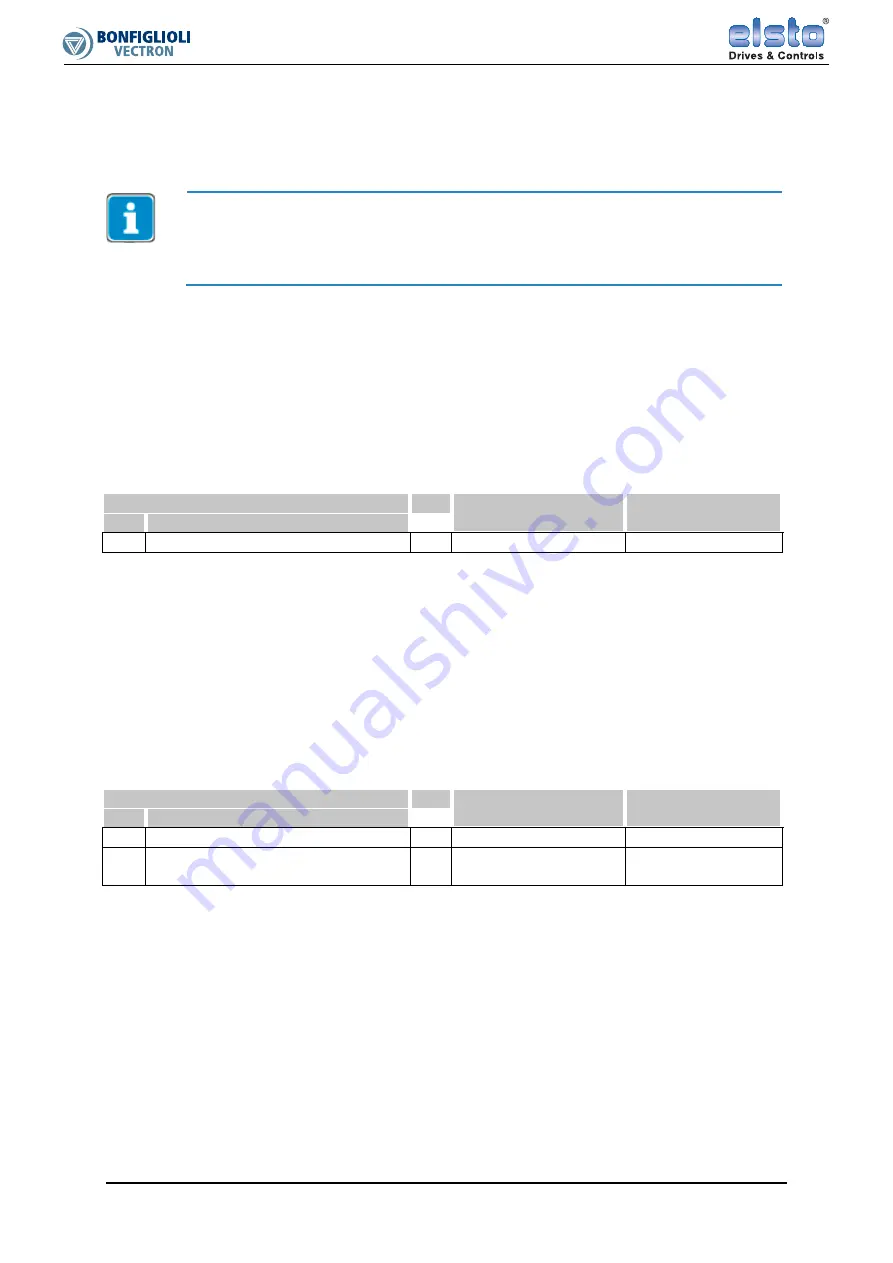
Voorhout • Groningen • Weert • Hoogerheide
T
+31(0)88 7865800
I
elsto.eu
Gear factor
Parameters
Gear Factor Numerator at Dmin
832
and
Gear Factor Denominator at Dmin
833
define
the numerator and denominator of the gear factor at minimum diameter
.
Parameter
Unit
Setting range
Default settings
No.
Identifier
832
Gear Factor Numerator at Dmin
-
1 .. 2147483647
1
833
Gear Factor Denominator at Dmin
-
1 .. 2147483647
1
Percentage source
After multiplication by a fixed gear factor, the input value is multiplied by a diameter-dependent per-
centage from Parameter
Source Gear Factor Percentage Value
834
.
Parameter
Unit
Setting range
Default settings
No.
Identifier
834
Source Gear Factor Percentage Value
-
Source percentage table 8942 – Speed Factor
at Dact filtered
Offset frequency
In Parameter
Offset Frequency
835
, you can define a fixed frequency value. This value will be added
to the reference frequency after consideration of the gear factors if the logic source from Parameter
Activate Frequency Offset
836
is TRUE.
Parameter
Unit
Setting range
Default settings
No.
Identifier
835
Offset Frequency
Hz
-50.00 .. 50.00
0.00
836
Activate Frequency Offset
-
Sources logic table
7 - Off
Parameter setup
Parameters
Gear Factor Numerator at Dmin
832
and
Gear Factor Denominator at Dmin
833
are
normally set such that the winding drive will follow the process exactly at the right speed when the
coil is empty.
In the case of indirect tension control (see Chapter 4.1 “Example: Indirect traction control”) is set
such that the winding drive tries to wind 5-10% too fast at all times.
If the Diameter Calculator is configured correctly, the value from actual value parameter
Gear Factor
Linefreq. to Winderfreq. at Dmin
844
can be used as a reference for the gear factor to be set. Pref-
erably, the gear factor should be calculated manually and Parameters
832
and
833
should be set
such that maximum accuracy is reached.
Via the percentage from Parameter
Source Gear Factor Percentage Value
834
, diameter-dependent
adjustment of the reference frequency is reached Normally, the right setting is source
Q.8942
gener-
ated by the Diameter Calculator. It will supply, at D
min
, the value 100% and decreasing values with
increasing diameters.
5.3.2
Output values
The output value can be obtained from the following source:
Frequency [s
-1
]
Q.8902
–
Output frequency of gear stage
11/13
ACU
Winding Drive
33
5.4
Limitation of web tension (Tension Setpoint)
With this function block, the web tension can be kept at a constant level in winding operations. It
limits the torque required for building up the web tension to a diameter-dependent value.
−
The function block should only be used for winders.
−
It is recommended that the winder drive be operated with sensor when the function
block is used (Configuration 217 or 517). In the case of sensor-less drives, at least
the working range must be above the current impression range, i.e. the motor speed
must be higher than the frequency set in Parameter
Frequency Limit
624
.
In order to keep the web tension at a constant level, the speed is set via the electronic gear such that
the winding drive would wind a little too fast (5-10%) at all times. The “web tension limitation” func-
tion block limits the torque to the value required for the required value. Acceleration and system loss-
es are considered.
In this way, the winding drive will not race even in the case of a web break and can be accelerated
and decelerated smoothly.
The logic signal for activation of web limitation is selected via Parameter
Activate Torque Limitation
860
.
Parameter
Unit
Setting range
Default settings
No.
Identifier
860
Activate Torque Limitation
-
Sources logic table
7 - Off
The value for torque limitation is made up of a constant value which is valid for the maximum diame-
ter and a diameter-dependent factor:
Parameter
Torque at Dmax
861
indicates the percentage of the rated torque of the machine is need-
ed at maximum diameter to build up the required web tension (static, without consideration of losses
due to friction).
The diameter-dependent factor considers the acceleration and system losses. For this factor, a suita-
ble percentage source is selected via Parameter
Source Diameter dependent Factor
862
. Normally,
this is the source provided by the Diameter Calculator
Q.8944
, see Chapter 5.2 “Diameter calculator”.
This source has value 100% at maximum diameter and is reduced with decreasing diameter such that
the web tension remains constant.
Parameter
Unit
Setting range
Default settings
No.
Identifier
861
Torque at Dmax
%
0.00 .. 300.00
100.00
862
Source Diameter dependent Factor
-
Percentage Source table 8944 – Torque Factor
at Dact filtered
5.4.1
Calculation of static torque for Parameter 861
If the required web tension is known, the percentage to be entered in Parameter
861
for the torque
at D
max
is calculated as follows:
Web
sion · D
max
/2
P.861
=
——————————
· 100%
M
rated
with
Web tension in [N]
D
max
in [m]
M
rated
in [Nm]
34
ACU
Winding Drive
11/13