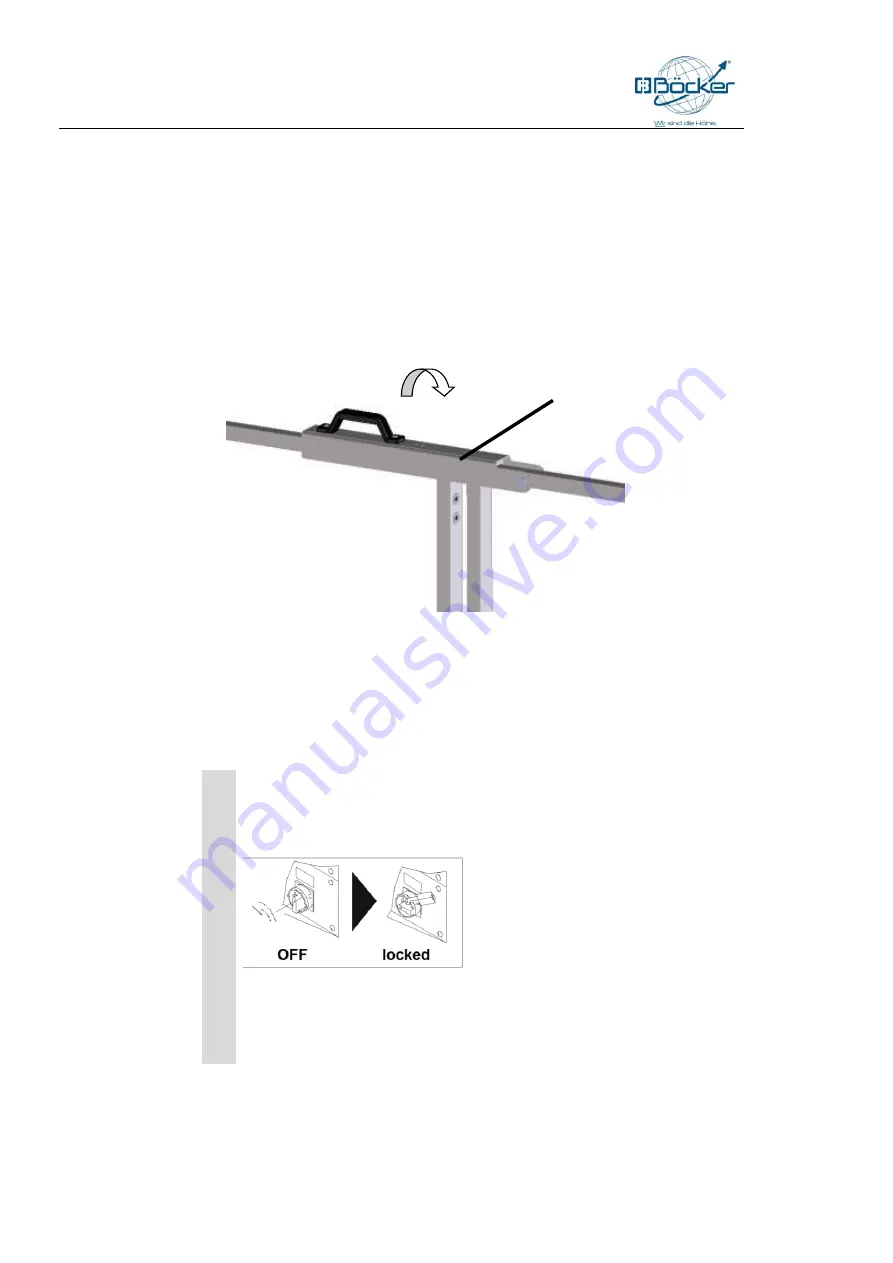
Steel frame Table form lift TL 1512
84
213300043
8.4.2 Door locking mechanism of the pivoting gate
In order to open the pivoting gate, the following conditions
must be met:
The pivoting gate can only be opened if the loading ramp
is open.
Fig. 52: Door locking mechanism of the pivoting gate
9 Shutting down the Table lift
1
Lower the platform to the ground station.
2
Completely close the platform gate and the loading position gate
3
Switch off the EMERGENCY OFF
main switch and secure the switch to
prevent from unauthorised restart.
Fig. 53: Switching off and locking the Emergency Off main switch.
4
Finally, disconnect the power supply and ensure accidental reconnection
is prevented.
Locking
mechanism