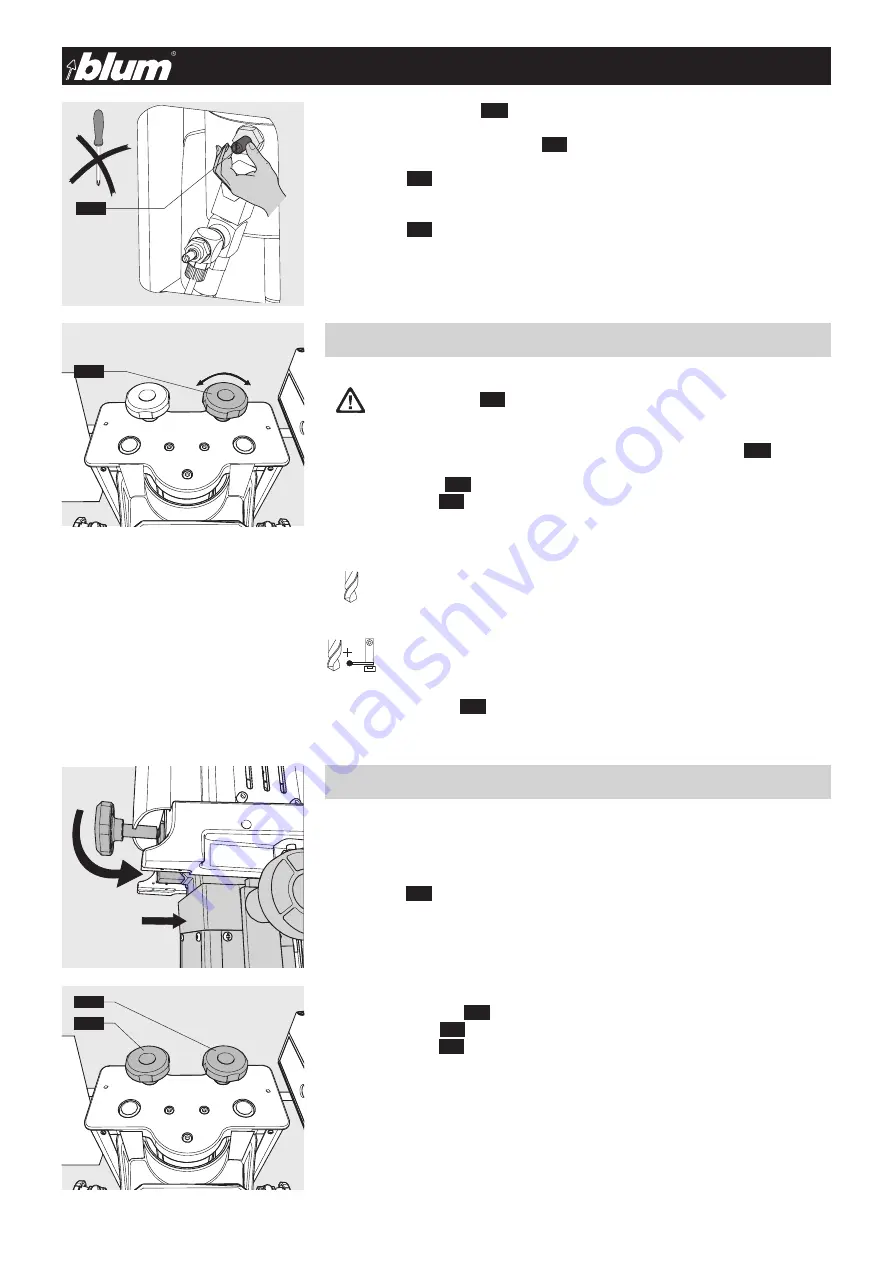
17
BA-102/2EN M54.XXXX
3 - How to operate the machine
3.5.3) Setting cam brake
(3.7)
The brake is set by turning the screw
(3.7)
on the cylinder.
• Turn screw
(3.7)
to the right:
slows down the drill bit
• Turn screw
(3.7)
to the left:
speeds up the drill bit
3.6.1) “Drilling” and/or “Drilling and inserting fittings” mode switch
(3.6)
• Press feed switch
(2.2)
• Set mode switch
(3.6)
to the desired setting
3.7.1) Assembly of furniture hinges, furniture connectors, METABOX and
TANDEMBOX front fixing brackets
• Insert the gear box (see point 3.1.1)
• Insert ruler
(8.2)
• Set work top
• Set hold down clamp
(3.3)
(see point 3.3.1)
• Set drilling depth
(3.4)
(see point 3.4.1)
• Set mode switch
(3.6)
to “Drilling and insertion”
(see point 3.6.1)
3.6 - Setting operating mode
Pos. A - Drilling
The return stroke of the assembly machine is limited.
Pos. B - Drilling and/or inserting fittings
The vertical drilling unit uses a full stroke.
3.7 - Drilling and inserting fittings
Important:
Particular care must be taken when working on sections that jut out
over the work top. Use extensions.
ATTENTION:
Set main switch
(2.1)
to Pos. 0
• Release feed switch
(2.2)
3.6
!
3.7
3.6
3.4