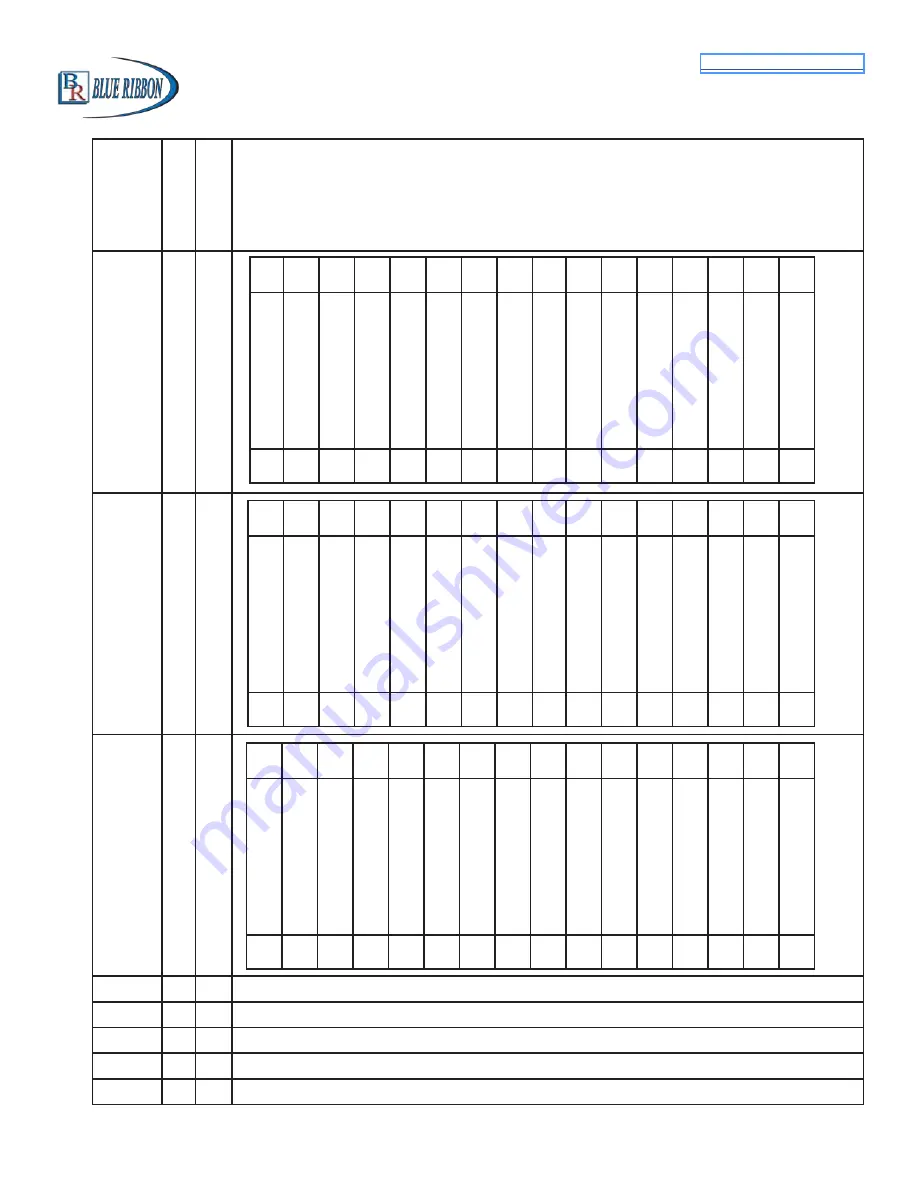
39
Model BB4000 Controller Instruction Manual
Description of Register Contents
(Where a Coil is represented by a Bit in a Register)
40008
√
Coil
Bit
40009
√
√
Coil
Bit
40010
√
√
Coil
Bit
40011
√
Wet Well Level (As shown on display with no decimal point)
40012
√
√
Setup Parameter - 1st Pump On Level
40013
√
√
Setup Parameter - 1st Pump Off Level
40014
√
√
Setup Parameter - 2nd Pump On Level
40015
√
√
Setup Parameter - 2nd Pump Off Level
Telemetry E
Discrete Input Function 19
Telemetry F
Discrete Input Function 20
Telemetry G
Discrete Input Function 21
Telemetry H
Discrete Input Function 22
All Pump Disable
Discrete Input Function 8
On Generator
Discrete Input Function 7
Off Level Float
Discrete Input function 33
High Level Float
Discrete Input Functions 18, 38
Low Level
(Level Probe Backup)
High Level
(Level Probe Backup)
4th Pump On Level Float
Discrete Input Function 36
3rd Pump On Level Float
Discrete Input Function 36
2nd Pump On Level Float
Discrete Input Function 35
1st Pump On Level Float
Discrete Input Function 34
Low Level Float Level
Discrete Input Functions 17, 32
113
0
114
1
115
2
116
3
117
4
118
5
119
6
120
7
121
8
122
9
123
10
124
11
125
12
126
13
127
128
14
15
High Level (When Level is
At or Above Alarm Setting)
Low Level (When Level is At
or Below Alarm Setting)
Force Alternation
Start Flush Cycle
Stop Flush Cycle
Flush Cycle Active
129
0
130
1
131
2
132
3
133
4
134
5
135
6
136
7
137
8
138
9
139
10
140
11
141
12
142
13
143
144
14
15
Register
Address
Write
Write
Pump 1 Called to Run
Pump 2 Called to Run
Pump 3 Called to Run
Pump 4 Called to Run
Pump 1 Remote Control
Disable Pump Operation
Pump 2 Remote Control
Disable Pump Operation
Pump 3 Remote Control
Disable Pump Operation
Pump 4 Remote Control
Disable Pump Operation
145
0
146
1
147
2
148
3
149
4
150
5
151
6
152
7
153
8
154
9
155
10
156
11
157
12
158
13
159
160
14
15