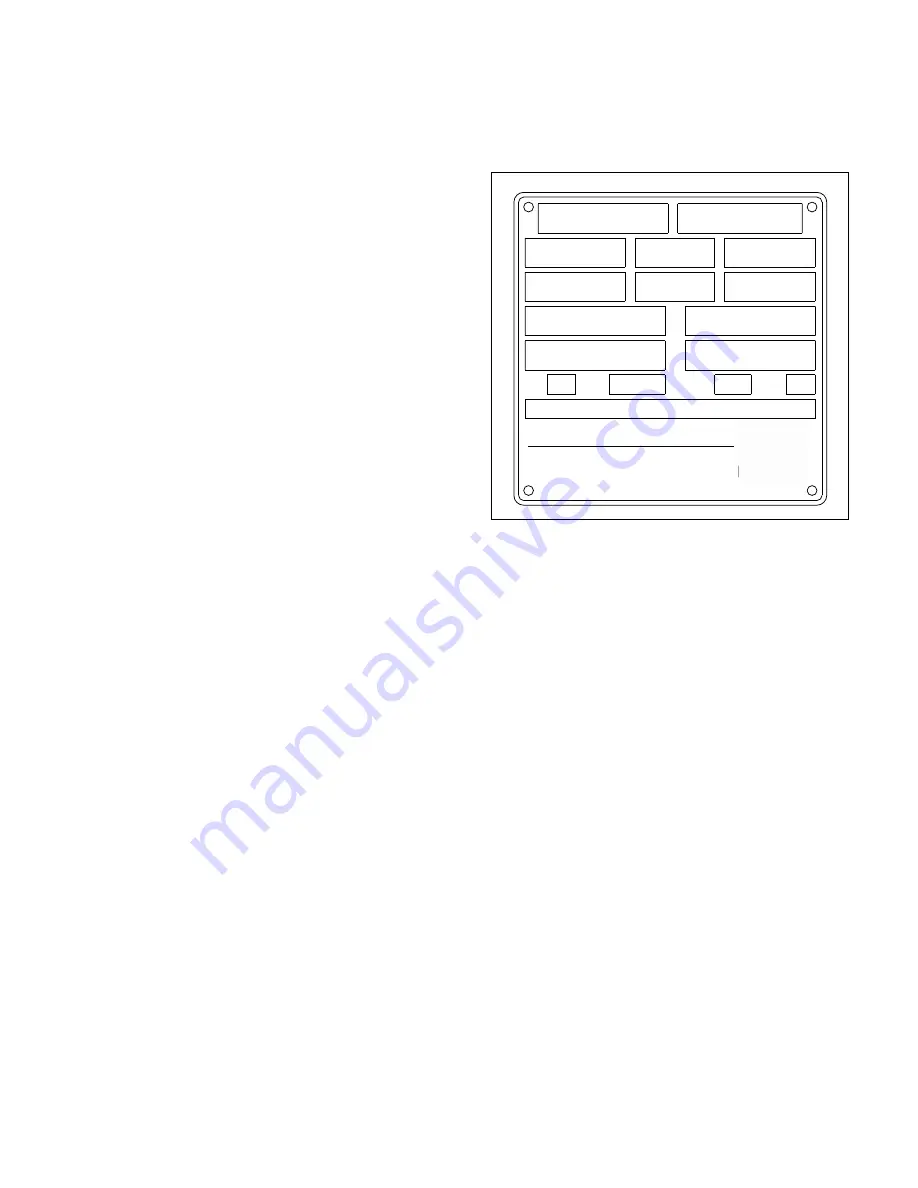
SECTION 1
DESCRIPTION
1-1.
INTRODUCTION.
This publication describes the 24 volt transistor
PDS lift truck distributed by
Blue Giant
. Included are
operating instructions, planned maintenance instruc-
tions, lubrication procedures, corrective maintenance
procedures and a complete parts list with part location
illustrations.
Users shall comply with all requirements indicated in
applicable OSHA standards and current edition of
A.N.S.I. B56.1 Part II. By following these requirements
and the recommendations contained in this manual,
you will receive many years of dependable service
from your PDS lift truck.
1-2.
GENERAL DESCRIPTION.
The self-propelled
BGN40
truck,
, lifts and
transports payloads up to 3000 pounds on either rigid
or adjustable forks. The self-propelled PDS 40 truck,
, lifts and transports payloads up to 4000
pounds on either rigid or adjustable forks.
The Telescopic truck has either a 104, 126 or 141 inch
lift. The TRIMAST truck has either a 158, 177, or 189
inch lift. The TRIMAST lift carriage will freelift the first 4
feet without changing the overall lift height. Then the
mast will start to rise. However, if the truck has an
optional load backrest, the backrest will raise above
the mast before the end of the full freelift.
The forward and reverse motion is controlled by either
of two controller levers mounted on the control head.
Stopping and turning is controlled by the steering arm.
Lift and Lower is controlled by pushbuttons on the con-
trol head. The battery powered lift truck is quiet and
without exhaust fumes.
The reversible AC motor propels the lift truck in for-
ward or reverse direction throughout the available
speed range. The PDS lift truck can be driven with
forks raised or lowered; however, the speed is
restricted when the platform is raised above a preset
limit.
The model number will be found on the name plate
) along with the serial number, lifting capac-
ity, and load center.
shows the locations of
the truck’s main components and controls.
Figure 1-1 Name Plate
1-3. SAFETY FEATURES.
The PDS is designed engineered to provide maximum
safety for operator and payload. Some of the safety
features incorporated into the design are:
• Dead-man brake to apply the brake and cut off drive
power when the steering arm is released.
• Belly-button switch to reverse truck should the oper-
ator accidentally pin himself against a wall or
obstruction when backing up in slow speed.
• High speed limit switch to restrict speed when lift
carriage is raised above the preset limit.
• All control functions automatically return to “OFF”
when released.
• Externally accessible quick-disconnect battery plug
within operator's reach.
• Separately fused control circuits and power circuits.
• Readily accessible horn button.
• Lift carriage backrest to help stabilize the load.
• Handle to provide a firm hand hold for operator.
• Flow control valve regulates maximum lowering
speed within prescribed limits.
• Relief valve maintains hydraulic pressure within pre-
scribed limits.
• High visibility color scheme of truck provides visual
alert of truck’s presence.
• Battery Indicator
• Casters.
COMPLIES WITH THE APPLICABLE REQUIRE-
COMPLIES WITH THE APPLICABLE REQUIRE-
MENTS OF ANSI B56.1 AND OSHA STANDARDS
MENTS OF ANSI B56.1 AND OSHA STANDARDS
TRUCK
TYPE
MODEL NO.
SERIAL NO.
VOLTAGE
BATTERY
TYPE
CERTIFIED
MAX CAP LB/
MAX CAP LB/
LOAD CTR IN/
LOAD CTR IN/
LIFT HGT IN/
LOAD CTR IN/
LOAD CTR IN/
LIFT HGT IN/
ALT CAP LB/
BATTERY MIN WT LB/
BATTERY MIN WT LB/
TRUCK WT LESS BATTERY LB/
TRUCK WT LESS BATTERY LB/
BATTERY MAX WT LB/
BATTERY MAX WT LB/
TRUCK WT WITH BATTERY LB/
TRUCK WT WITH BATTERY LB/
KG
MM
MM
MM
MM
KG
KG
KG
KG
KG
R6209
5
Summary of Contents for BGN-40
Page 6: ...Figure 1 2 PDS Lift Truck R6765 6...
Page 12: ...NOTES 12...
Page 18: ...NOTES 18...
Page 34: ...NOTES 34...
Page 39: ...Figure 5 4 Cap Assembly R6809 39...
Page 44: ...Figure 7 1 Transmission Motor Brake Assembly R6811 44...
Page 45: ...Figure 7 2 Adjustable Straddle R6814 45...
Page 46: ...NOTES 46...
Page 48: ...Figure 8 2 Elevation System Telescopic R6816 48...
Page 50: ...Figure 8 3 Mast TRIMAST R6817 50...
Page 52: ...NOTES 52...
Page 56: ...Figure 9 2 Mast Telescopic R6816 56...
Page 57: ...Figure 9 3 Lift Cylinder Telescopic R6825 57...
Page 59: ...Figure 9 4 Mast TRIMAST R6817 59...
Page 60: ...Figure 9 5Free Lift Cylinder TRIMAST R6826 60...
Page 62: ...Figure 9 6 Secondary Lift Cylinder TRIMAST R6827 62...
Page 64: ...Figure 10 1 Electrical System R6478 R6828A 64...
Page 67: ...Figure 10 3 Transmission Motor Brake Assembly R6811 67...
Page 68: ...NOTES 68...
Page 70: ...NOTES 70...
Page 72: ...Figure 12 1 Steering System R6807 72...
Page 74: ...Figure 12 2 Control Head R6808 74...
Page 76: ...Figure 12 3 Cap Assembly R6809 76...
Page 79: ...NOTES 79...
Page 80: ...Figure 12 5 Transmission Motor Brake Assembly R6811 80...
Page 82: ...Figure 12 6 Compartment R6813 82...
Page 84: ...Figure 12 7 Adjustable Straddle R6814 84...
Page 86: ...Figure 12 8 Fixed Straddle PDS 40 ONLY R6844 86...
Page 88: ...Figure 12 9 Caster Adjustable Straddle R6834 88...
Page 90: ...Figure 12 10 Caster Fixed Straddle R6845 90...
Page 92: ...Figure 12 11 Elevation System Telescopic R6816 92...
Page 94: ...Figure 12 12 Elevation System TRIMAST R6817 94...
Page 96: ...Figure 12 13 Lift Carriage R6815 96...
Page 100: ...Figure 12 16 Pump Motor Assy R6820 100...
Page 102: ...Figure 12 17 Hydraulic System Telescopic R6821A 102...
Page 104: ...Figure 12 18 Hydraulic System Telescopic R6822A 104...
Page 106: ...Figure 12 19 Hydraulic System TRIMAST R6823A 106...
Page 108: ...Figure 12 20 Hydraulic System TRIMAST R6824 108...
Page 110: ...Figure 12 21 Lift Cylinder Telescopic R6825 110...
Page 112: ...Figure 12 22 Free Lift Cylinder TRIMAST R6826 112...
Page 114: ...Figure 12 23 Secondary Lift Cylinder TRIMAST R6827 114...
Page 116: ...Figure 12 24 Electrical System R6828A 116...
Page 119: ...NOTES 119...
Page 120: ...Figure 12 26 Drive Motor R6830 120...
Page 125: ...125...