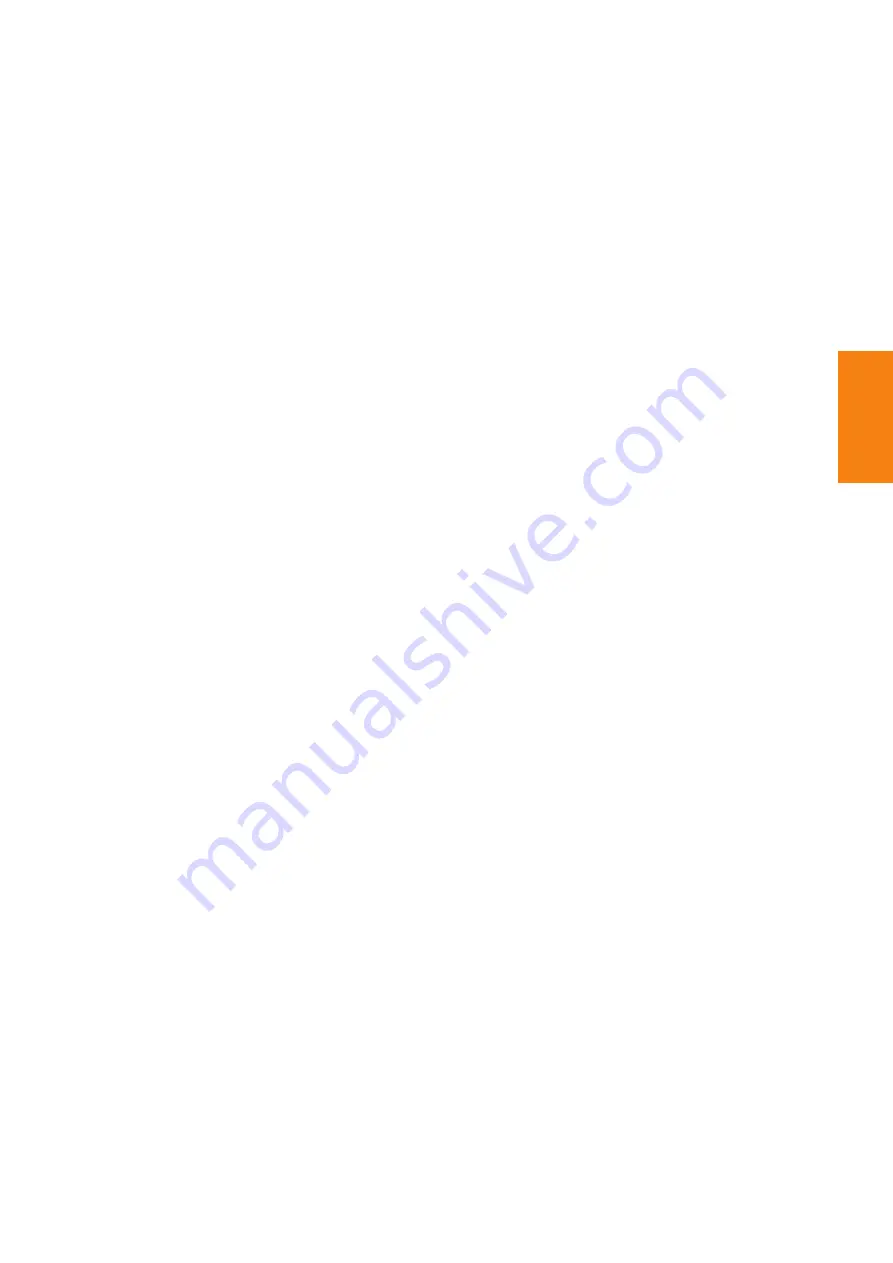
11
C
OM
M
IS
S
ION
ING
FloorHand Commissioning Procedure
This test procedure is to be performed by authorized B+V personnel only!
Note: When performing the following steps, appropriate PPE will be used and standard safety practices must be followed at all
times.
Note: When commissioning, H.P.U Commissioning must be completed prior to FloorHand commissioning. If installing
FloorHand to customer supplied hydraulics, hoses must be flushed completely before connecting to FloorHand.
1.
___ Connect FloorHand (using flow meter) to Hydraulic power source of 2,500-2,800
psi and 25-28 gpm. If pressure is above 2,800 psi, a Pressure Release Valve (PRV)
should be used. _____If flow rate is above 28 gpm, a pressure compensated flow
control should be used.______
2.
___ H.P.U should be powered up a minimum of 20 minutes before moving to next
step, to bring all oil to required operating oil temperature, record oil temp._________
Note: Throughout entire test, observe FloorHand for leaks, and or malfunctions, repair as necessary.
3. ___ Run spinner motors in make direction for 20 seconds, check that rotation of all
four rollers are correct, check for leaks. Monitor flow meter, record max flow. ________
See step 1.
4. ___ Run spinner motors in break direction for 20 seconds, check for leaks.
Note: After making fresh hydraulic connections, or a rig move, it is best to always run the spinner before anything else. The
spinner is the only system that is close to a direct system. For example, there are no PRV’s, check valves, shuttle valves,
diverter valves, pilot operated check valves, etc. in the spinner motor system, only a flow divider. This means, by running the
spinner first, any small trash or contaminants that may be in the lines, will be flushed through with minimal to no damage. If
there were trash in the lines, and the torque, or clamp system were operated first, there is a chance of contaminants getting
lodged in a small orifice, in one or more of the many valves in the other systems.
5. ___ Without pipe, clamp and unclamp lower wrench 10 times, check that die blocks
extend and retract evenly, check for leaks.
Note: This helps to remove air from the lower clamp system so that the flow divider may work correctly.
6.
___ Without pipe, clamp lower wrench.
7.
___ Clamp and unclamp upper wrench 10 times, check that die blocks extend and
retract evenly, check for leaks.
8.
___ Unclamp lower wrench.
9. ___ Without pipe, clamp and unclamp spinner 10 times, check for leaks.
Note: spinner may, or may not close evenly, this is normal.
10.
___ Back torque adjustment knob out completely, then turn in (clockwise) 4 turns,
Blohm + Voss Oil Tools, LLC.
11. ___ Actuate torque cylinder 10 complete strokes in each direction and check for
leaks.
12.
___ Adjust make up speed flow control for a 5 second stroke. Verify during
commissioning.
13.
___ Install test gauge on lower clamp cylinder outboard test port.
14.
___ Clamp lower wrench.
15. ___ Observe the test gauge on lower wrench clamp cylinder, and Pressure Release
Valve (PRV) if applicable.
16.
___ Set Pressure Release Valve (PRV) output to obtain 600 psi at lower clamp
Summary of Contents for 9PU-7200
Page 5: ...5 DESCRIPTION DESCRIPTION ...
Page 9: ...9 COMMISSIONING COMMISSIONING ...
Page 14: ...14 INSTALLATION INSTALLATION ...
Page 17: ...OPERATIONS 17 OPERATIONS ...
Page 22: ...MAINTENANCE INSPECTION 22 MAINTENANCE INSPECTION ...
Page 24: ...24 SPARE PARTS SPARE PARTS ...
Page 26: ...26 DRAWINGS DRAWINGS ...
Page 27: ...27 DRAWINGS Figure 9 ...
Page 28: ...28 DRAWINGS Figure 10 ...
Page 29: ...29 DRAWINGS Figure 11 ...
Page 30: ...30 DRAWINGS Figure 12 ...
Page 31: ...31 DRAWINGS Figure 13 ...
Page 32: ...32 DRAWINGS Figure 14 Figure 15 ...
Page 33: ...33 DRAWINGS Figure 16 ...