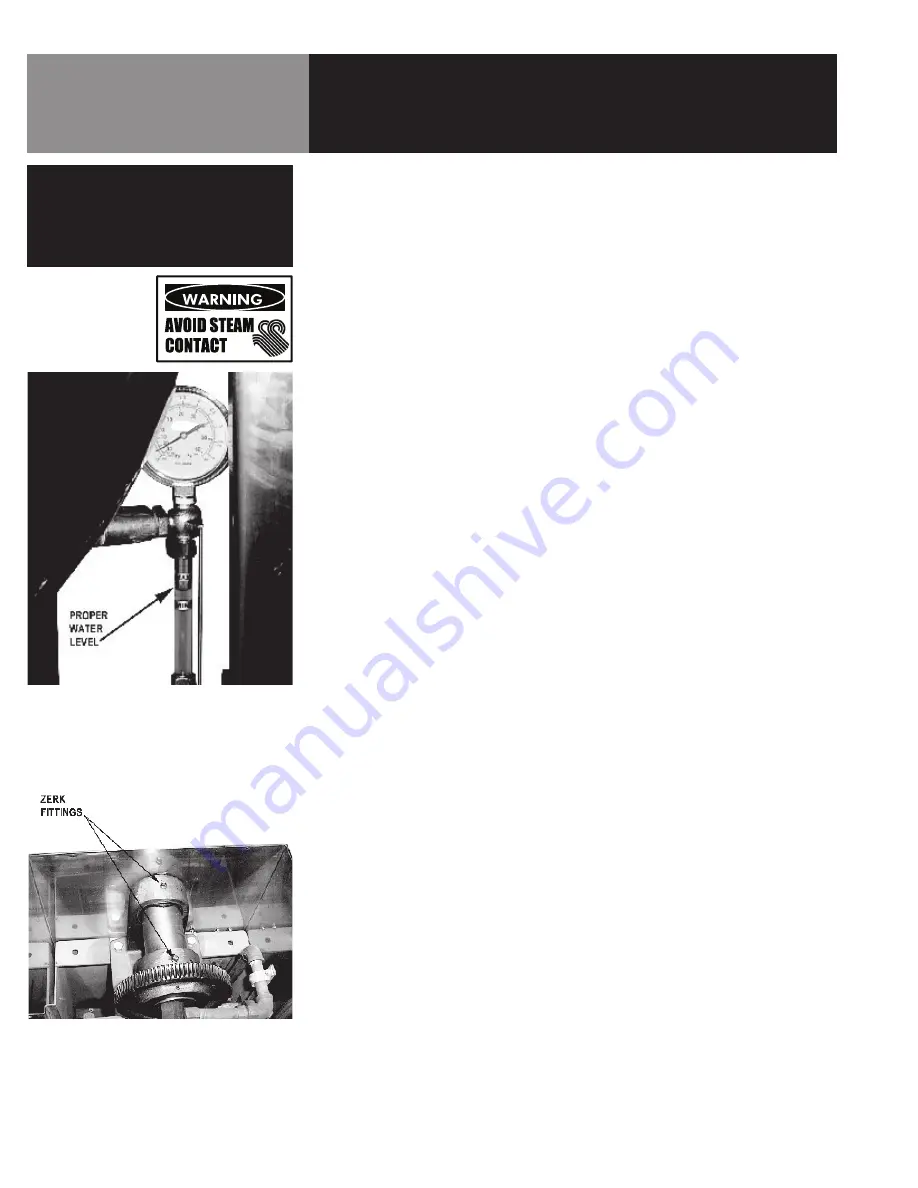
14
OM-KLT-G
Maintenance
NOTICE: Contact an authorized representative when repairs are required.
A.
Periodic Maintenance
A Maintenance & Service Log is provided at the back of this manual with the
warranty information. Each time maintenance is performed on your kettle, enter
the date on which the work was done, what was done, and who did it. Keep this
manual on file and available for operators to use.
Periodic inspection will minimize equipment down time and increase the ef-
ficiency of operation. The following points should be checked:
1.
Check the pressure/vacuum gauge every day. The gauge should show
a vacuum of 20 to 30 inches mercury (Hg), when the kettle is cold. If it
does not, see “Jacket Vacuum” on page 16.
2.
Also check the jacket water level every day. It should be between the
markers on the gauge glass or inside the sight glass port. If the level is
low, see “Jacket Filling and Water Treatment” on page 16.
3.
Test the safety valve at least twice each month. With the kettle operating
at five psi (105 kPa), pull the test lever and let it snap back to its closed
position. If there is little discharge (mostly air), and the pressure gauge
drops back to zero PSI, allow the pressure to build back to five PSI and
repeat the procedure. (Tip: Using a screwdriver or other implement to
pull the ring will help you avoid contact with the steam.)
4.
If the valve does not activate, or there is no evidence of discharge, or the
valve leaks, stop using the kettle and contact a qualified service repre-
sentative.
5.
Keep the primary burner gas jet air inlets free of dust and lint.
6.
The pilot flame should be blue. It should envelop about ½ inch (12 mm)
of the flame sensor tip.
7.
The gear housing has fittings for lubrication of moving parts. The gears
do not run in oil, so periodic lubrication with grease is necessary.
8.
Frequency of lubrication depends on operating conditions, but it should
be done at least once every six months.
9.
Use a #2 grade LGI lithium grease to add grease through Zerk fittings on
gear housing until it flows out of the bearings around the trunnion shaft.
10. Place liberal amounts of grease on the gear to cover the arc that is in
contact with the worm gear.
11. Keep electrical wiring and connections in good condition.
12. Keep the inside of the control console clean and dry.
13. Keep burner slots clean.
WARNING
WHEN TESTING, AVOID ANY EXPOSURE
TO THE STEAM BLOWING OUT OF THE
SAFETY VALVE. DIRECT CONTACT
COULD RESULT IN SEVERE BURNS.
WEAR EYE
PROTECTION
The pressure gauge should show a
vacuum of 20 to 30 inches of mercury (Hg)
and the water level should be between the
markers when the kettle is cold.
Add grease through Zerk Fittings.