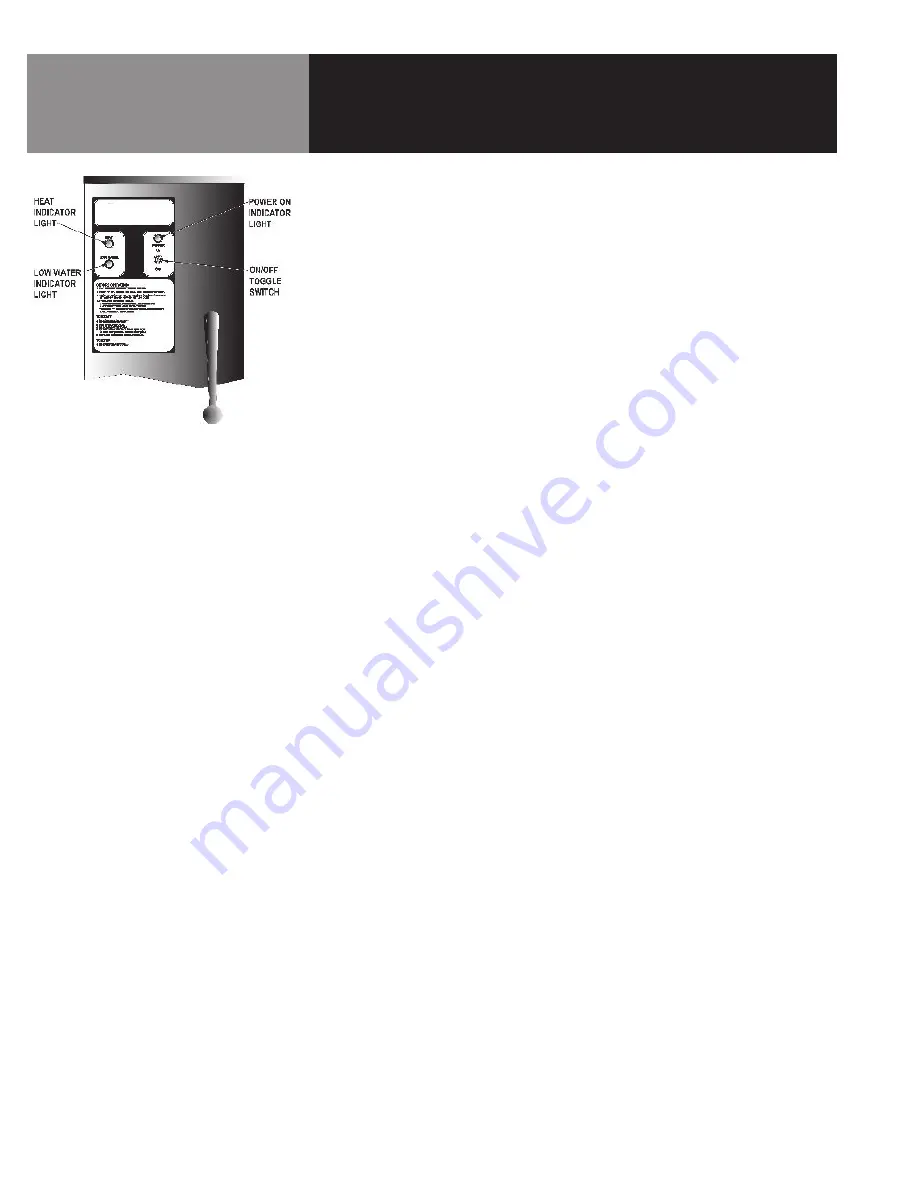
8
OM-KLT-G
Operation
A.
Controls
Operator controls for the kettle are:
1.
Manual gas valve (on gas line behind the unit), which controls the supply
of gas from the main to the unit.
2.
On-Off (Toggle) Switch. This controls the supply of electric power to the
control circuits.
3.
Thermostat dial, which turns the thermostat on or off, and sets the kettle
temperature.
4.
Tilting crank, used to tilt the kettle body.
5.
Indicator Lights to alert operator of unit conditions:
a.
Power On Indicator - shows that the unit is turned on
b.
Heat Indicator - indicates that main gas is on to produce steam in
the kettle jacket.
c.
Low Water indicator - shows that jacket water is low
6.
Unit gas pressure regulator adjustment - located behind the access door
in the kettle skirt.
B.
Operating Procedure
1.
To Start Kettle:
a.
EVERY DAY make sure that the jacket water level is between the
markers on the gauge glass or inside the sight glass port. If the level
is too low, see “Jacket Filling and Water Treatment” on page 16.
b.
Check the pressure gauge. If the gauge does not show 20 to 30
inches of mercury (Hg) vacuum (that is a reading of 20 to 30
below 0 atmospheric pressure), see “Jacket Vacuum” on page 16.
c.
Do not attempt to light any burner with a flame. Turn the manual
gas valve ON (align handle with gas line).
1)
Turn toggle (on-off) switch ON. The electronic ignition will
attempt to light the pilot for 90 seconds, or until it is lit.
Once lit, proceed to step two.
2)
Turn thermostat to desired setting. The main gas burner will
ignite, and will cycle to maintain the set temperature. The
3)
If the unit does not light, turn it off and wait five minutes.
Then follow the instructions again.
2.
To Empty Kettle:
a.
To tilt the body of the kettle forward, turn the hand crank on the
front of the cabinet counter-clockwise. The body will stay in the
position it holds when you stop cranking. To return the kettle body
to its upright position, turn the crank clockwise.
b.
Product may also be transferred by means of the optional draw-off
valve, if the kettle is so equipped.