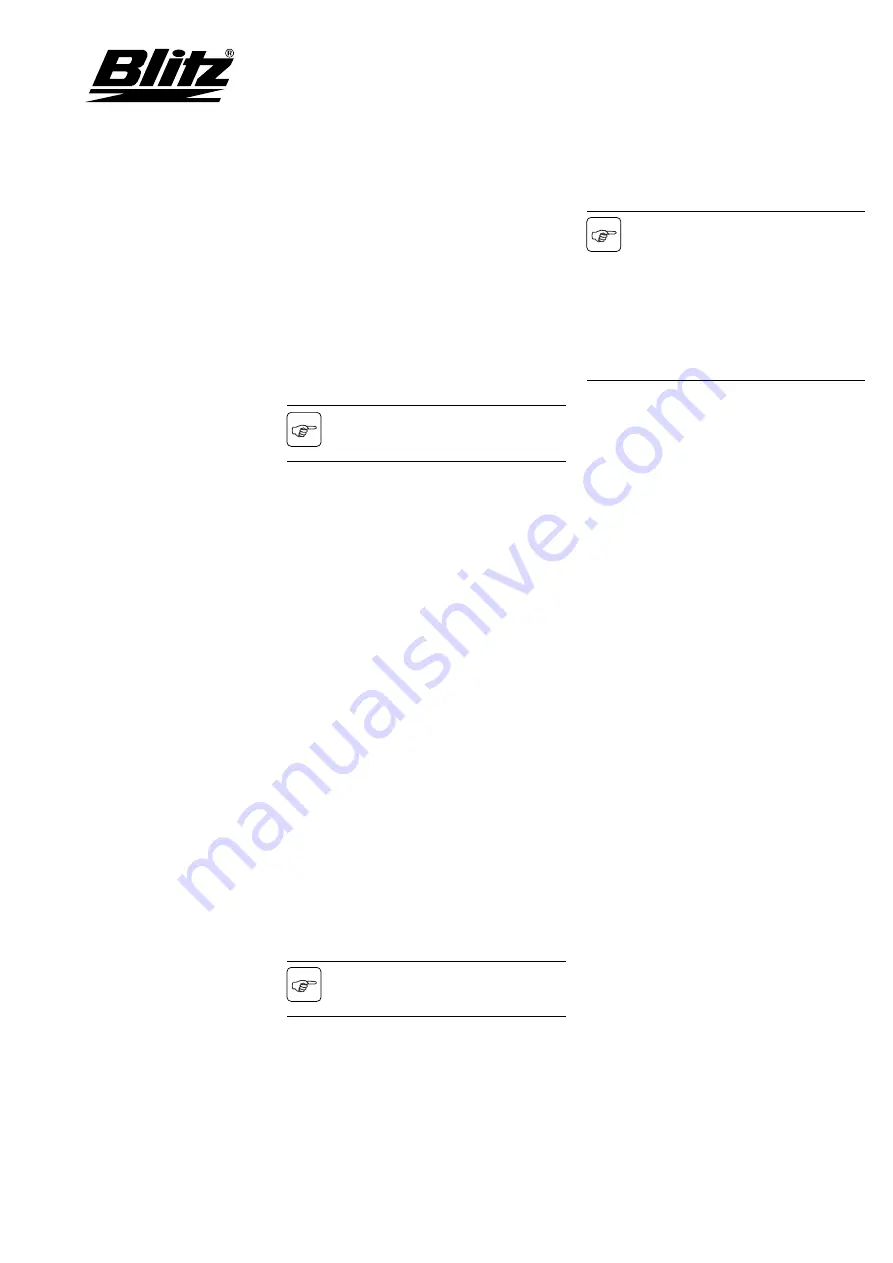
Operating instructions
Inspection and servicing
11
104485 • 03/03
!
Place a suitable collecting vessel under
the oil filter 24.
!
Turn the oil filter left using chain pliers to
screw it off.
!
Clean the oil filter holder.
!
Screw down the new oil filter until the
gasket is firmly in place.
!
Replace oil that has escaped by new oil
(refer to chapter 6.2 “
Checking and topping
up the oil level
“).
5.5
Draining the condensation wa-
ter
The condensation water contains oil
and has to be disposed of according to
the local environmental regulations.
Drain the condensation water every week.
!
Place a suitable collecting vessel under
the oil and condensation water drain valve
15.
!
Remove plug 15
while it is at operating
temperature.
!
Screw down enclosed
oil and condensation
water
drain valve.
!
Drain the condensation water into the
vessel until pure oil escapes.
!
Screw off
oil and condensation water drain
valve.
!
Screw down plug 15 again.
5.6
Cleaning the oil cooler and the
compressed-air aftercooler
!
Blow compressed air through the cooling
fins of the oil cooler 27 and of the com-
pressed-air aftercooler 26 (see fig. 1: Com-
ponent overview) from the inside of the
machine until dust and deposits have dis-
appeared.
5.7
Checking safety valve
The safety valve 11 (see fig. 1: Compo-
nent overview) is secured with a seal
which must not be removed.
!
Slightly lift the valve cap to check the
function.
5.8
Changing oil high-precision
separator cartridge
Use only a new oil high-precision sepa-
rator cartridge; you cannot clean a
used high precision separator car-
tridge.
A small amount of oil can escape as
you change the oil high-precision
separator cartridge.
Dispose of the oil high-precision sepa-
rator cartridge according to the appli-
cable local environmental regulations.
!
Turn the oil high-precision separator car-
tridge 3 (see fig. 1: Component overview)
left using chain pliers to screw it off.
!
Clean the oil high-precision separator
cartridge holder.
!
Oil slightly the O-ring and the gasket of
the new oil high-precision separator car-
tridge.
!
Screw down the new oil high-precision
separator cartridge until the gasket is
firmly in place.
5.9
Checking and changing the
suction filter cartridge
!
Remove cap of the suction filter 23
(see fig. 1: Component overview).
!
In case of severe soiling, immediately
replace the suction filter (cf. list of BLITZ
spare parts in the chapter titled “Technical
annex”).
!
Refit the cover of the suction filter.
!
Press visual wear indication 33 on the
cover to reset to zero.