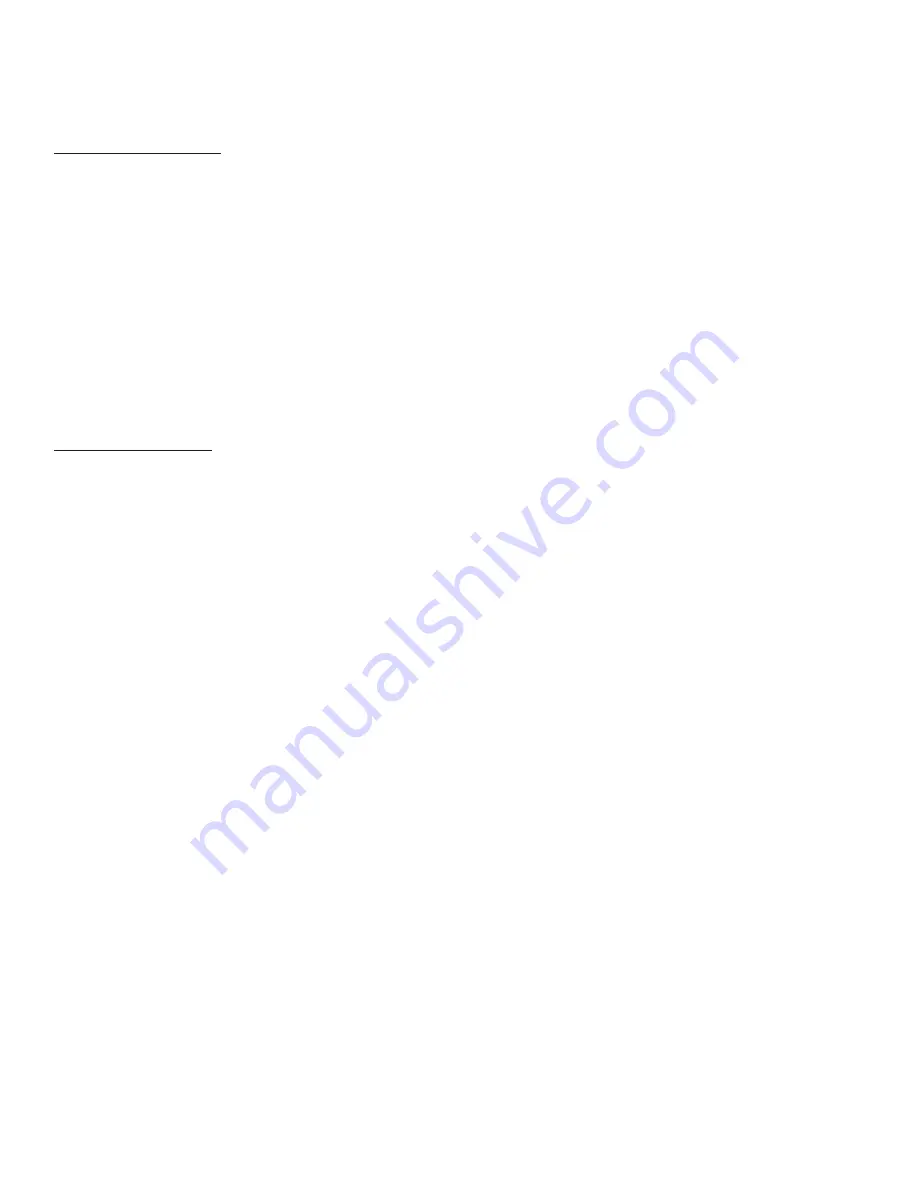
2 BBL Hybrid™ 2 Vessel Brewhouse V2
© Blichmann Engineering, LLC 2019
For replacement parts, visit: blichmannengineering.com/genuine-replacement-parts
9
Caution:
NEVER restrict the inlet to the pump. Always place flow throttling valves on the OUTLET of the pump ONLY. Failure to do this will
cause cavitation in the pump possibly leading to failure of the impeller. If you hear any grumbling or grinding in the pump STOP IMMEDI-
ATELY as this is cavitation. Cavitation failures are NOT covered under warranty.
Tip:
A spray of StarSan on the interior surfaces after cleaning will help prevent mildew between uses.
Tip:
Place your chiller in-line with the pump to clean it at the same time.
Mash Tun:
Spent grains can easily be removed through the manway in the mash tun. Drain all remaining wort out of the bottom drain and then open the door.
Utilizing a non-marring hoe (available in our maintenance kit) rake out the spent grains into a tub, also available through Blichmann Engineering. Remove the
false bottom sections and spray them off with hot water and allow to dry. Spray excess grain from the sidewalls and bottom of the kettles with a hose.
BK/MT:
Due to the easy access through the top of the relatively small tanks, and small size of the chiller and pumps, it is usually fastest to scour the kettles with
a scrub brush mounted on a pole and spray them out with a hose. Optional cleaning tools are available through Blichmann Engineering to make this a fast and
thorough job. Alternately, you can utilize one of the heated vessels to heat and hold your CIP (clean in place) chemicals and use one pumps to recirculate through
the CIP ball and the second pump to return back into the chemical kettle. It is recommended that you turn off all heaters while running the CIP system to avoid dry
firing them. Tip your kettles forward so that all water drains out the bottom valve, leave the lid open, and allow the kettles to dry thoroughly.
Cleaning Your System:
Typical heating rates are 0.8-1.5 F/min.
Expect about a 5% boil-off rate
Temperature loss in MT – less than 1F/hr
Temperature stability of control system approxi/- 1 F
Helpful System Data