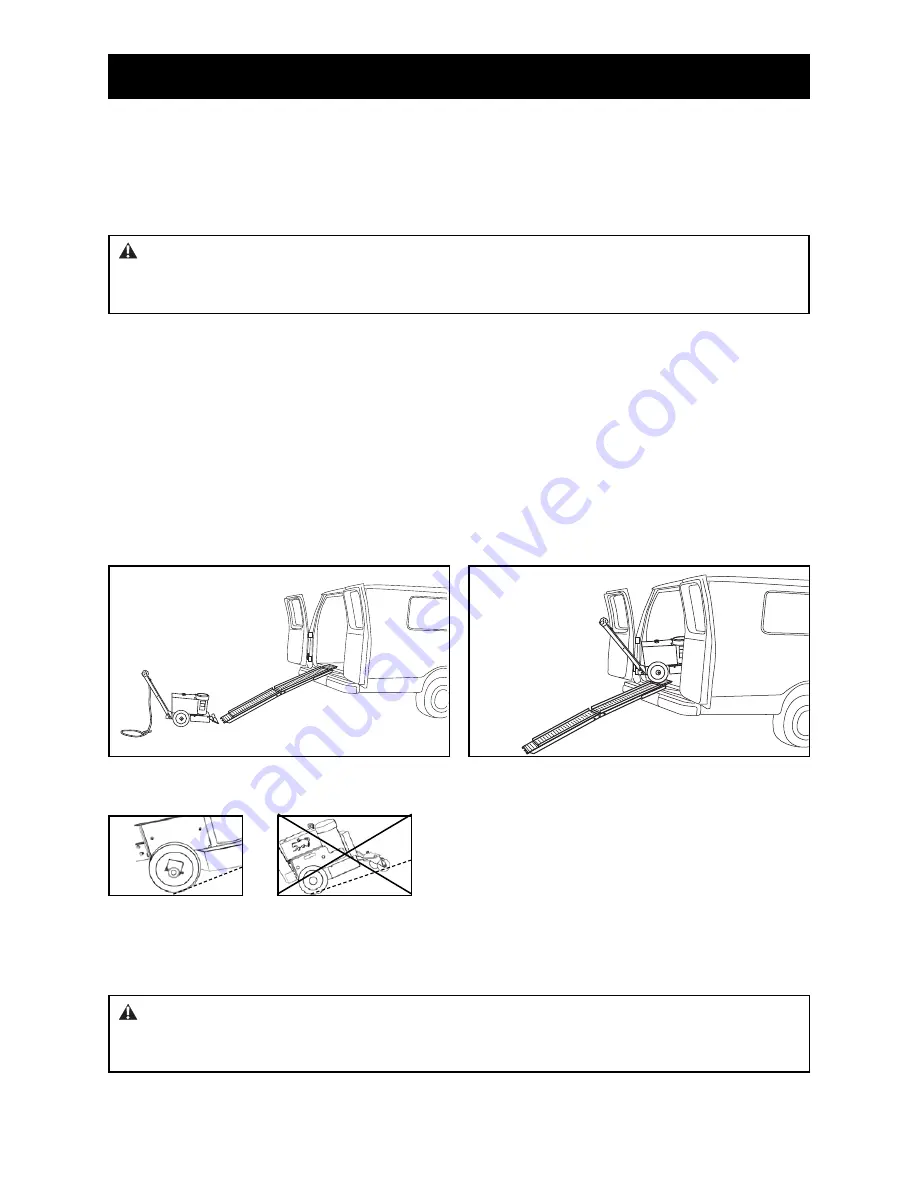
Page 12
BS180 TRANSPORTATION
UNLOADING
• Position machine at the back of the truck in line with the ramp (See Figure B).
• Carefully move machine onto ramp leaving cutting head down (in contact with ramp surface).
• Even without counterweights machine weighs 318 pounds
• Make sure you have machine under control. Failure to do so could cause machine runaway, damage to
machine, damage to property or cause serious injury.
• Slowly back machine down ramp. This is done the easiest with the machine under power and driving
the on or off.
• Ramp is designed to work from a van height. Easy for most loads up to 26
''
or 19° angle. Somewhat
difficult for large loads up to 32
''
or a 23° angle. Not recommended for anything higher. A pickup is too
high.
WARNING:
Ramp must have good contact with the back of the vehicle. Failure to do so could
cause ramp to lose contact with back of vehicle resulting in damage to the machine or injury to
the operator.
Figure A
WARNING:
Never load or unload machine on a ramp or incline when wheels are in the disengage
mode. Failure to do so could cause machine runaway, damage to machine, damage to property or
cause serious injury.
CORRECT
INCORRECT
Figure B
Summary of Contents for BS 180
Page 50: ...Page 48 110 VOLT WIRING DIAGRAM 110 VOLT 60 HZ...
Page 52: ...Page 50 BS180 MATERIAL SAFETY DATA...
Page 53: ...Page 51 BS180 MATERIAL SAFETY DATA...
Page 54: ...Page 52 BS180 MATERIAL SAFETY DATA...
Page 55: ...Page 53 BS180 MATERIAL SAFETY DATA...
Page 56: ...Page 54 BS180 MATERIAL SAFETY DATA...