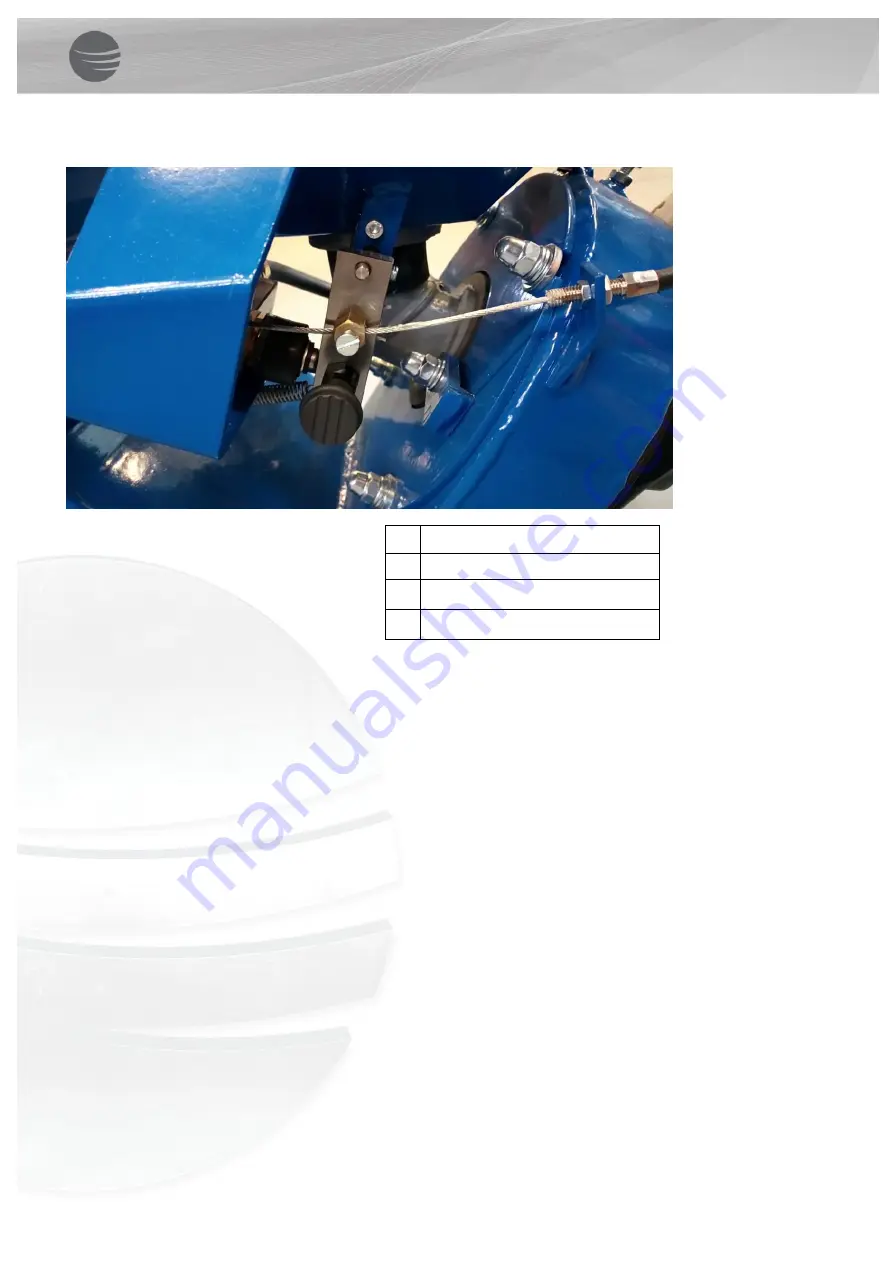
16
5.7
The blast pattern
Abrasive leaving the blast wheel blades is not thrown in all directions. Scatter is restricted to an angle of about
50°. This is achieved through the use of a control cage which surrounds the impeller.
The position of the control cage has been set by
Blastrac
and is fixed by pins and recesses. Do not remove any
fixings. Incorrect adjustment of the control cage results in very high wear and premature blasting-through of the
liners in the blast wheel housing, as well as reduced blasting performance and a possible loss of the rebound
energy of the abrasive.
Every time the control cage is replaced, the thread of the blast wheel fastening nut should be checked. Make sure
that this nut will be tightened correctly. In addition, absolute care must be taken to clean the thread from dust and
abrasive.
The best speed depends on the material of the surface to be cleaned and the desired profiling.
The right speed can be found out by observing the blasted surface and varying the speed during the blast cleaning
process
Slight profiling on concrete requires a higher speed then coarse profiling.
Blasting on steel requires a very low advancing speed.
The following 3 factors affect the blast pattern:
With increased wear of the tune-up kit (impeller, control cage) the blast pattern will change.
The size of the abrasive affects the blast pattern.
Different types and hardness of surfaces.
1
Feed spout
2
Control cage
3
Cage clamp
4
Cage retaining plate
1
2
3
4