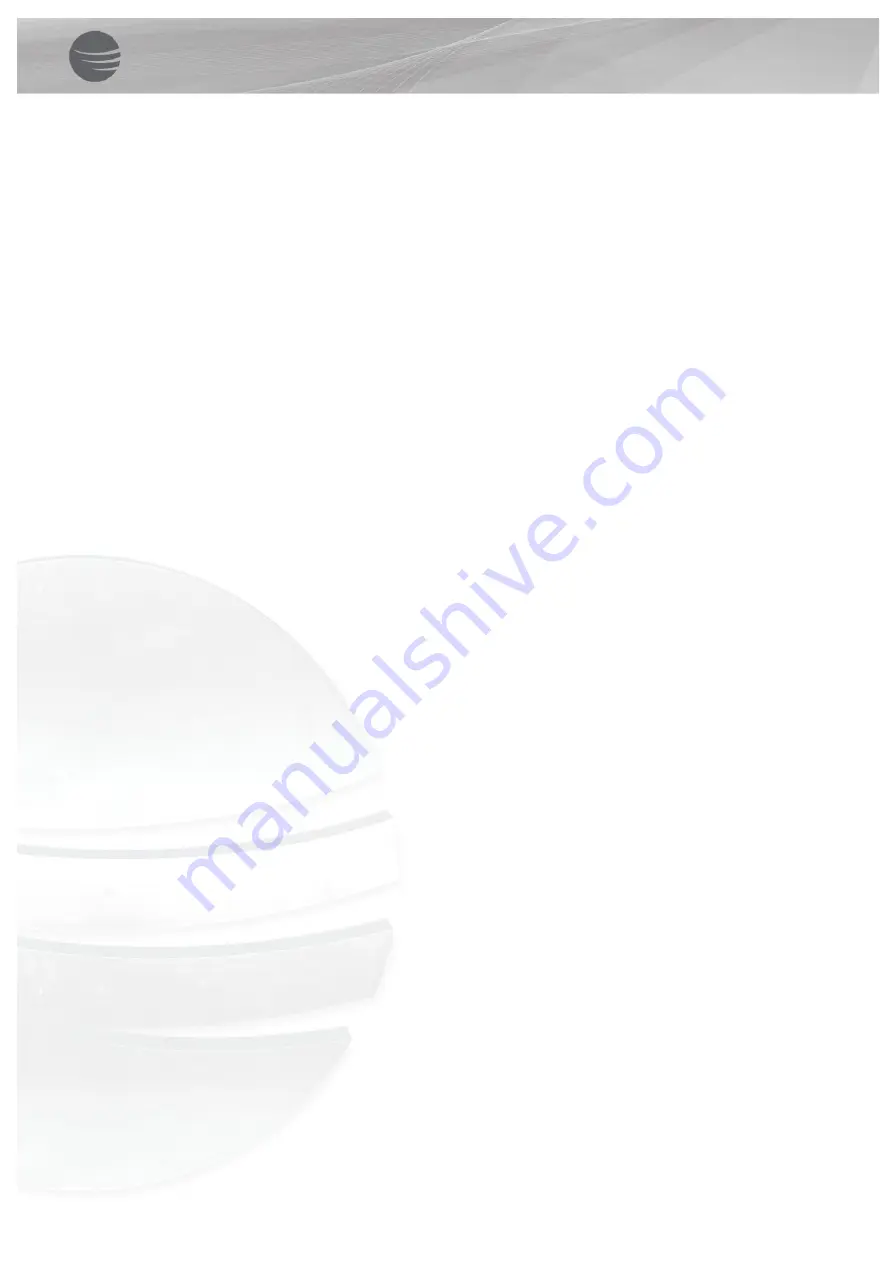
8
3.5
Maintenance safety
a)
Pull out the main plug and place it in sight, before starting inspections and repairing on the machine.
b)
Wait for standstill of the machine before any inspections, adjustments and/or maintenance work is
started.
c)
Block machine in stable position before doing any maintenance work.
d)
Failures due to inadequate or incorrect maintenance may generate very
high repair costs
and long
standstill periods of the machine.
Regular
maintenance therefore is imperative.
e)
Operational safety and service life of the machine depends, among other things, on proper maintenance.
f)
Prevent premature wear by keeping the machine as dust free as possible. Clean the machine for this
reason regularly with a dust collector and non-aggressive materials. Never use a high pressure water
cleaner to clean the machine.
g)
Do not use any
aggressive
cleaning materials!
h)
Use lint-free
cleaning cloths
!
i)
It is advisable to stock all spare parts or wear parts that cannot be supplied quickly. As a rule, production
standstill periods are more expensive than the cost for the corresponding spare part.
3.6
Dust collector safety
a)
Always use a Blastrac dust collector
to ensure a dust-free operation of the machine and clean air at
the workspace. Also the airflow helps to cool the machine and prevents overheating.
b)
Read the operating instructions of the dust collector before using it.
c)
The dust container/bag of the dust collector must be emptied regularly
. Comply with the local
waste treatment regulations considering the removed material.
d)
The dust hose must be connected properly with a hose clamp and industrial tape.
e)
The dust hose must be undamaged and free of obstructions.
f)
Always switch on the dust collector first!
3.7
Shot blasting safety
a)
Never lift the blast head during blasting!
This could cause serious injury to yourself and others
around you!
b)
Abrasive can escape from the sides of the blast head at high speed!
Wear safety glasses with
lateral protection and close-fitting protective clothing.
c)
Check the following parts daily for damage and wear to avoid unnecessary long and costly standstill on
the workplace; blastwheel, feedspout, liners, magnet- and brush sealing;
Replace the parts when you can see obvious signs of wear and tear.
Wear grooves are acceptable until 75% of blade thickness has been worn away.
d)
Check the parts of the separator on wear and defects. Remove foreign bodies and dust deposits to
prevent clogging of the separator.
e)
The cover of the separator and separator tray must be closed to keep the vacuum in the machine.
f)
The machine will heat up during blasting, don’t risk getting burned, always wear gloves and only touch
the handle .
g)
Check the level of abrasive in the storage hopper before work starts. Refill if necessary.
h)
Remove the abrasive from the abrasive storage hopper before storage.
i)
In some cases sparks could be created by shot / steel blasting.